BIRI: I Industrivegen på Biri, tett inntil Moelven Mjøsbruket og adskilt fra Mjøsas bredder av E6 Lillehammervegen, ligger Madshus. Inne i den 5000 kvadratmeter store skifabrikken er de i gang med å produsere langrennsski til neste sesong. Om en måned eller to kommer de store forhåndsordrene som skal være leveringsklare til høsten, så det er årets siste kvartal som gir størst utslag på bunnlinjen til skiprodusenten. Slik har det vært siden Martin Madshus laget de første skiene i en låve på Gjøvik i 1906, men utenom det er det meste forandret.
I år er det 45 år siden de siste treskiene ble produsert i det som den gang var Madshus’ splitter nye fabrikklokale. Før 1970 hadde ikke produktutvikling vært en del av vokabularet i Madshus, men så lanserte flere østerrikske produsenter glassfiberski. Under VM i Falun i 1974 ble alle distanser utenom én vunnet av løpere på glassfiber. Magne Myrmos gull på 15-kilometeren ble historiens siste VM-gull på treski. Madshus ble nødt til å gjøre noe, og omstillingen gikk så raskt at de fire tørkene som var installert for å tørke trematerialene før de ble omgjort til ski aldri ble tatt i bruk.
Teknisk direktør i Madshus, Bjørn Ivar Austrem, ble ikke født før treskiproduksjonen var bestemt avviklet. Men det nye tankesettet som vokste i Madshus samtidig som han vokste opp, nyter han nok godt av i dag.
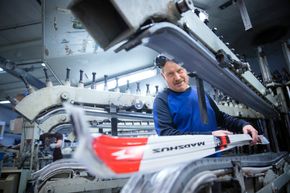
– Vi investerer for mellom 5 og 10 millioner kroner hvert år, sier Austrem, mens han guider oss gjennom produksjonslinjene i fabrikken. Før jobbet nesten samtlige av bedriftens rundt 90 ansatte i produksjonen. Nå har de fortsatt like mange ansatte, men langs produksjonslinjene er det bare 30 mennesker som jobber side om side med roboter. Kontinuerlig forskning, utvikling og automatisering står i høysetet. Det må til for at bedriften på Biri ikke skal tape i konkurranse mot østerrikske og franske gigantselskaper som Fischer, Atomic, Salomon og Rossignol.
Sensorikk og data
De siste 15 årene har Madshus fått over 26 millioner kroner i BIA-midler fra Forskningsrådet. Det
er ikke medregnet midler til prosjekter de deltar i uten å være prosjektleder for. To prosjekter er pågående: SkiAlive og Nano2Glide.
For å best forstå hva SkiAlive handler om – og hva prosjektet kan ha å si for Madshus – tar vi en tur oppom Sjusjøen før vi fortsetter runden i fabrikken. I skianlegget på Natrudstilen har Madshus rigget seg til sammen med prosjektpartner Sintef for å samle verdifulle data fra felttester, som videre skal kobles tilbake til produksjonen. En rekke skipar utstyres med akselerometere, gyroskoper og kameraer. Skiløperne får tilsvarende sensorer på armene og brystet, en gps-klokke rundt håndleddet og en høyfrekvent gps som gjør 10 målinger i sekundet festet til ryggen. Og så går de runde etter runde med forskjellige skipar. Foran en pc i smørebua sitter Sintef-forskerne og følger med.
Sensor-dataene og målingene de lagrer og visualiserer i sitt egenutviklede program SkiViewer er en videreføring fra et tidligere prosjekt som het Empower. Det endte i RFID-brikkene som har vært integrert i alle norskproduserte Madshus-ski siden 2014, og som gjør det mulig for butikker og sluttkunder å få opp informasjon om skiens spenn og smøresoner i en tilhørende app.

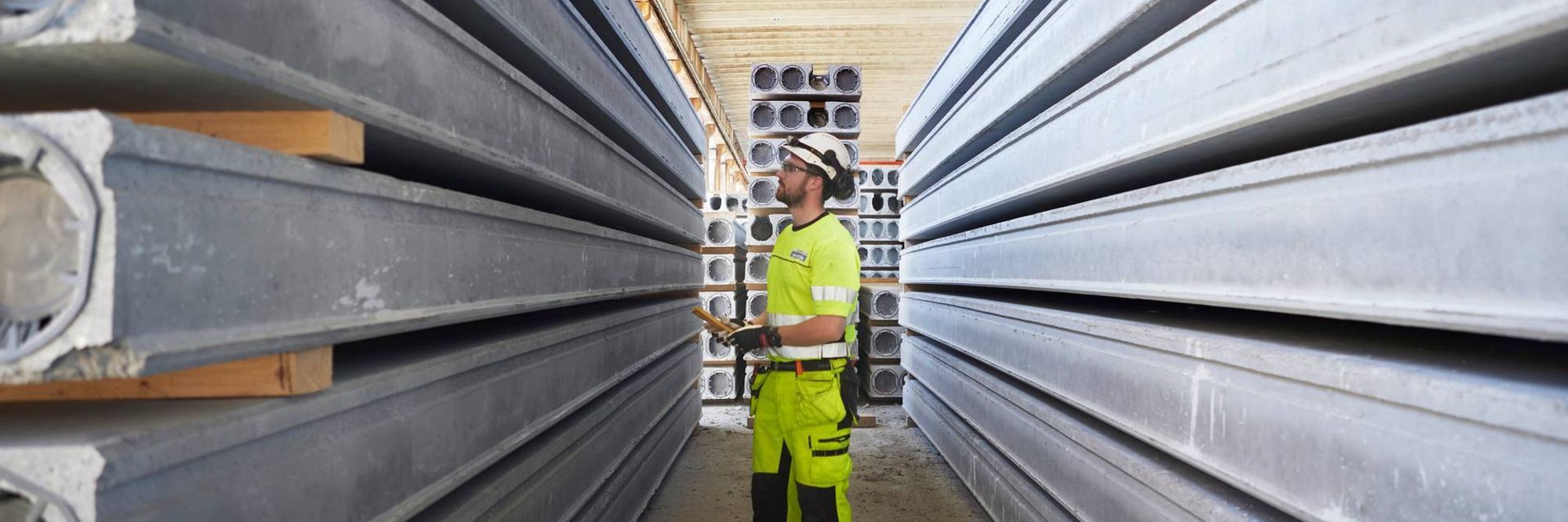
Men nå skal dataene motsatt vei – fra skiløypa og tilbake til produksjonen.
I SkiAlive skal de nemlig utvikle en digital plattform som ved å kombinere informasjonen knyttet til RFID-brikkene med objektive målinger fra felttester skal gjøre det mulig å kontrollere og styre variasjoner i produksjonen som påvirker skiens ytelse. Det skal gi bedre repeterbarhet, mer presis produksjon, færre avvik og mindre vrak.
– Informasjon fra testing med skiløpere på snø er viktig for å kunne si noe om de kvalitative egenskapene til skiene. Målet er å finne produksjonsmekanismene som påvirker produksjonen slik at man får ski med ønsket karakteristikk. Vi ønsker å bidra med metodikk som gjør at man ikke bare kan effektivisere hver enkelt delprosess, men også validere endringene som blir gjort, og se sammenhengen mellom endringene og resultatene i sporet, sier prosjektleder og seniorforsker Johannes Tjønnås i Sintef Digital, som har tre avdelinger involvert i prosjektet.
Nøkkelegenskaper
Foreløpig er prosjektet i startfasen, og det meste av tiden frem til nå er brukt på å lage strukturer for å sammenstille de store datamengdene. I tillegg til data fra produksjonen og testingen, må også all informasjon om de ulike råmaterialene, prosessene de er gjennom, og hvordan dette påvirker materialene regnes med. Det samme må snø- og værdata fra de aktuelle testdagene.
– Dette er spennende benyttelse av data for oss, og Sintef jobber veldig analytisk med å sortere all informasjonen. Håpet er selvfølgelig at vi skal finne de egenskapene eller produksjonstrinnene som kjennetegner en gullski, og automatisere prosessen slik at den oppskriften blir standard, sier Bjørn Ivar Austrem.
Tjønnås tror de skal få det til:
– Vi samarbeider godt med Madshus, og de er veldig delaktige i utviklingsprosessen. Vi har fått tilgang til deres databaser, og de har fått tilgang til vår kode. Vi ser på dette prosjektet som en prosess hvor vi skal påvirke og sammenstille data fra hele produksjonskjeden for å forbedre og lukke designsløyfa i skiproduksjon. Når du da måler skiegenskapene fra en produsert ski og justerer produksjonsprosessen, så vil dette gi en forventet og ønsket endring i egenskapene til de nye skiene du produserer, sier Tjønnås.

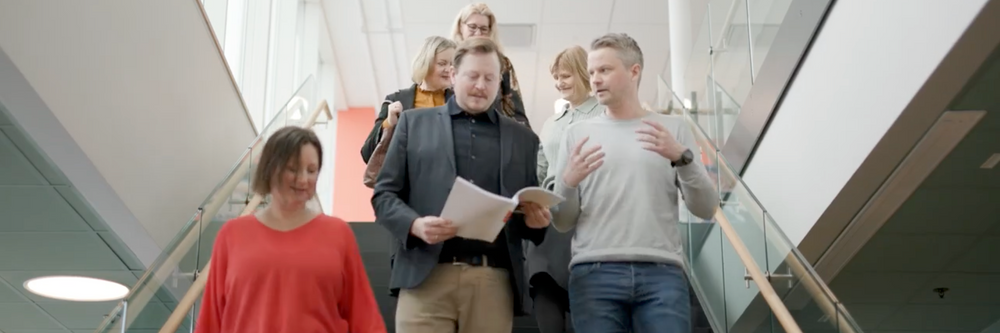
Fleksibilitet
Tilbake i fabrikken på Biri er det Kuka-roboter som har tatt over de mest repetitive oppgavene, som å flytte ski fra en maskin til en annen. Også fresing av formen på tuppen og bakenden av skiene, liming av NIS-platene bindingen monteres i, og festing av de fleste glassfiber- og karbon-forsterkningene til skumkjernene er automatisert.
Andre arbeidsoppgaver har forsvunnet naturlig grunnet digitalisering. I trykkeriet har digitaltrykk tatt over for silketrykk. Tidligere måtte de bytte silkerammer for hver eneste farge og lengde til hver eneste ski, noe som sysselsatte 14-15 personer. Nå som grafikken trykkes digitalt, er avdelingen bare bemannet av 1-2 personer.
– En av de største utgiftene på produktet vårt er naturlig nok arbeidskraft. Effektivitet er veldig viktig, og når vi investerer skal det alltid være på en slik måte at kvaliteten blir bedre og omstillingstiden kortere. Robotisering gir oss fleksibiliteten vi trenger når visjonen er én-stykk-produksjon, sier Austrem. Det betyr at produksjonen skal kjøre like fort om det kommer fire ulike typer ski på båndet, som om det kom fire like ski etter hverandre.

Her har selvfølgelig også de nevnte RFID-brikkene en viktig rolle. ID-en fra brikken registreres allerede når skien støpes, og inneholder all basisinformasjon som gjør at maskiner videre i prosessen kan styres mer nøyaktig utfra hvilken ski som kommer. Det reduserer risikoen for feil. Mer informasjon kobles til skiens unike ID etter den har vært gjennom selskapet egenutviklede spennmålemaskin, som måler hver ski 23 ganger – fra ubelastet til fullt belastet – i løpet av 20-30 sekunder under dynamisk lastpåkjenning. Denne maskinen er såpass hemmelig at vi verken får ta bilder av den eller se den på nært hold. Til våren vil Madshus runde 1 million produserte ski med RFID-brikke, og de er som sagt også avgjørende for videre digitalisering og robotisering.
Det viktige spennet
For på dette området er Madshus langt fra ferdige.
– Vi ønsker å digitalisere spenninnstillingen på skiene i støpekarusellen, sier Austrem, og snakker om støpemaskinene med 20 armer som går rundt i en sirkel, akkurat som en karusell. I hver støpemaskin kan de støpe ulike modeller i hver arm. Nå har de to maskiner som går, så de kan lage 40 modeller på en gang. Én karusell er forbeholdt racingski. Fra en ski legges i karusellen tar det 20 minutter før den er ferdig herdet, nedkjølt og kan tas ut på samme side som den ble lagt inn. Når den kommer ut av karusellen er nesten 100 prosent av skiens egenskaper bestemt. Det er derfor spenninnstillingen er så viktig.
– I dag stilles spennet ved å stramme 23 skruer bortover hele skilengden i helt riktig posisjon. Det er litt som å stemme et piano: For at det skal bli bra trenger du folk med mye erfaring og kunnskap for å gjøre det, men når det er ulike individer som gjør jobben, vil det også være subjektive tanker og ideer om hva som er riktig spenn. Nå som vi har en database med mye data har vi mulighet til å analysere mer, og teste egenskaper vi tidligere ikke har visst om. Derfor håper vi at maskinlæringsalgoritmer fra SkiAlive-prosjektet kan gjøre at vi støper toppski hver gang, sier Austrem. Som skiprodusent er det der utfordringen ligger: Før en ski er ferdig skal den gjennom nærmere 50 prosesser i fabrikk, mot normalt rundt 20 for de fleste andre produkter. Deretter – når kunden tar den i bruk – skal skien beholde de samme egenskapene når den deformes. Det kan for eksempel være fra 20 mm spennhøyde uten belastning, og ned til 0,2 mm belastet. Da er det utfordrende å ha kontroll på sluttresultatet.
– De fleste ski i samme serie produsert etter hverandre ligger normalt innenfor en tiendedels sekund i forskjell på en 20 sekunders glidtest. Men om du legger sammen en tiendedels sekund hvert 20. sekund fra Sjusjøen til Birkebeiner stadion på Birken, så blir det en del. Og det blir fort enda mer med feil lagt smøring eller feil slip eller rill, så det er veldig mange variabler – og mange av dem vises ikke før skiene er ferdig produsert, sier Austrem.
Klare algoritmer
Derfor ønsker de også å digitalisere paring av ski. Både automatisert paring og spennjustering er arbeidspakker i SkiAlive-prosjektet. For skiparing har de Matlab-algoritmer så si klare, men utfordringen er hva algoritmenes utvelgelse og sortering i praksis skal resultere i.
– En ting er å finne de teoretiske dataene det skal pares etter og lage et program for tingene som fungerer etter intensjonen, men hva skal skje med de skiene som ikke møter toleransekravene? Det er det å behandle unntakene som er størstedelen av koden og tar mest tid. Vi er nødt til å være smarte der, sier Austrem.
Den tekniske direktøren er likevel klar på én ting – det er ikke alt de kan eller vil automatisere:
– Det meste lar seg automatisere, men i noen tilfeller kan det bli veldig fastlåst og gå utover fleksibiliteten. Roboten som fester forsterkninger til kjernematerialet, tar ikke ski som er kortere enn 140 uten at vi må bygge den om eller bytte griper. Da er det mer fleksibelt å ta kortere ski for hånd. Tupp- og bakendefresen gjør heller ikke skiene 100 prosent klare – de siste millimeterne skråkant pusses manuelt. Vi har utfordret flere firma på å finne en løsning med alt fra trykksensorer til kameraer, men ennå ikke funnet noe som gjør jobben bedre enn øynene våre! Å oppdage alt av kosmetiske ting i overflaten og i sålen som gjør en ski feilfri eller ikke, det vil vi aldri klare uten skismarte ansatte, sier han.
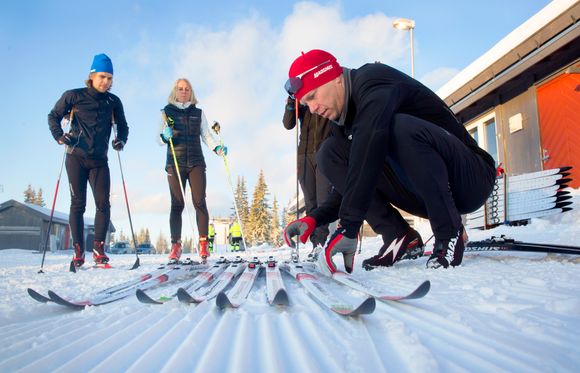
Fluorfri totalpakke
Foruten produksjonsoptimaliseringen, må Madshus også forholde seg til fluorforbudet som trer i kraft neste sesong. De jobber i et konsortium sammen med Brav (Swix), IDT, NTNU, Sintef og Olympiatoppen for å utvikle et nytt produktkonsept bestående av en ny type skisåle, kompatible fluorfrie smøreprodukter og tilpassede struktureringsverktøy. Prosjektet heter Nano2Glide, og har fått 10 millioner kroner i innovasjonsstøtte fra Forskningsrådet.
Her er Madshus’ konkrete oppgave å lage ski med såler tilsatt additiver som gjør dem mer mottakelige for smøring som ikke er fluorbasert. Så langt har de utviklet to testsåler, som Brav videre tester smøretyper på. Men de har langt igjen.
– Foreløpig prøver vi å bli flinkere på fysikken. Sålen er jo laget for å være vannavstøtende og gli godt, så da er det selvmotsigende å få ting til å hefte til den. Vi må få en konkret forståelse av hva som skjer når sålen kommer i kontakt med snøen, og skjønne tribologien, slik at vi klarer å finne gode alternativer, sier teknisk direktør i Madshus, Bjørn Ivar Austrem.
Målet er at de skal ha et produktkonsept klart til Birkebeinerrennet 2022, og ute på markedet før VM 2023. Lab-testene starter til våren. Professor Alex Klein-Paste ved Institutt for bygg- og miljøteknikk ved NTNU leder prosjektet. Han forklarer at nøkkelen ligger i å finne en fluorfri smøring som sitter godt på skisålen, men har dårlig friksjon mot snø. I tillegg er overflatestrukturen i skisålen en viktig faktor. Fordi fluor har suverene vannavstøtende egenskaper, blir overflatestrukturen enda viktigere uten fluorholdig smøring.
– Jeg er stolt av at vi har fått med et så kunnskapsrikt og mangfoldig konsortium på prosjektet, og tror det er kjempeviktig for å lykkes. Det er mange paralleller mellom konkurranser i idrett, næringsliv og i forskning. I hvert tilfelle handler det om å skaffe nøkkelkunnskap først, og klare å anvende denne. Jeg vil mene vår suksess i dette prosjektet er avgjørende for at disse norske industribedriftene skal overleve når fluorforbudet trer i kraft for fullt, sier Klein-Paste.
Slik produseres Madshus-skiene
Se trinn for trinn i bildekarusellen under.