Når vinteren nærmer seg presenterer Madshus teknologi som må være rene drømmen for ekte skientusiaster. Som første skiprodusent i verden lanserer Madshus smart-ski. Det ligger mange års utviklingsarbeid bak, støtte fra Norges forskningsråd og samarbeid med Sintef, samt en rekke leverandører.
Vinterens nye modeller av de mest avanserte skiene er utstyrt med RFID av typen near field communication, NFC.
Les om: ACT Systems automatiserer Hallingplast
Tester spenst
Gjennom brikken får både Madshus, salgsapparatet og kunden tilgang til all verdens informasjon om skien. For kunden er det viktigste at skien har vært gjennom en omfattende testing av spensten på fabrikken. Dermed er spennet dokumentert. Sammen med en nyutviklet applikasjon som blir tilgjengelig fra 1. september kan kunden finne riktig lengde på smøresonen.
Men før skiløperen står klar i skogkanten og skal smøre, må skien kjøpes. Det skal gå lettere fra kommende sesong. I butikken vil det være utstyr tilgjengelig der kunden kan taste inn en rekke parametere. Vekt og høyde skal inn, likeså om skien skal brukes til klassisk eller skøyting. Det er to førekategorier, klister- og tørrføre. Til sist kan kunden oppgi hvor avansert han eller hun er som skiløper.
Da får selgeren opp ski som skal passe den aktuelle kunden, og kan gi gode anbefalinger betydelig raskere enn med dagens systemer.
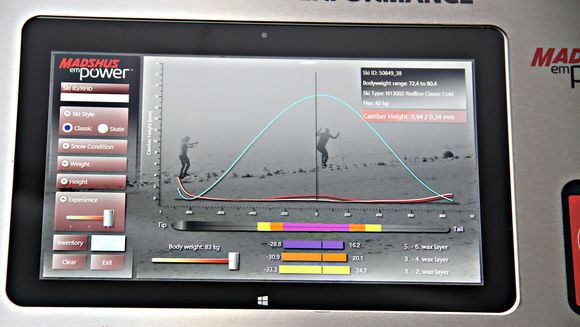
Sparer tid
– Det utstyret som butikkene har i dag for å finne rett spenn, er tidkrevende å bruke. Når det allerede er gjort og selgeren får opp de rette skiene fra en database, blir det lettere å veilede kunden, sier Bjørn Ivar Austrem, teknisk direktør hos Madshus.

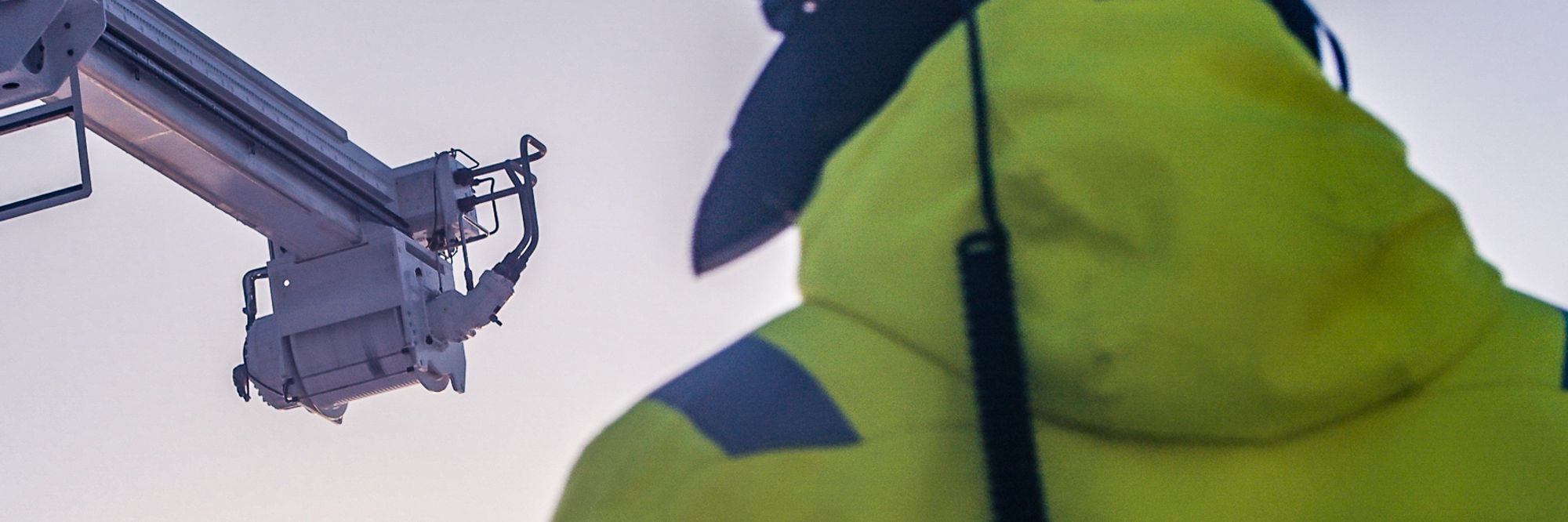
En graf på skjermen i butikken viser buen på skien og stivheten. Programvaren er utviklet av RFID-Huset i Halden. Konseptet, som omfatter både utstyret i butikken, applikasjonen og programvaren, kalles Empower. Applikasjonen kan brukes til mye, den ivrige skiløperen kan laste ned data om alle skiparene. Data fra skiturer, som hvor, når og hvordan føret var, kan også legges inn ved hjelp av samme applikasjon. Når skien er kjøpt kan kunden lese av RFID-brikken og laste inn relevant informasjon til telefonen.
Madshus har i dag en takttid på 20 sekunder. Austrem og hans folk jobber nå for å få takttiden på målemetoden ned til 20 sekunder. Etter hvert vil da alt som lages komme inn i empower-programmet.
Les også: IT-sjefene bryr seg ikke om maskinvare
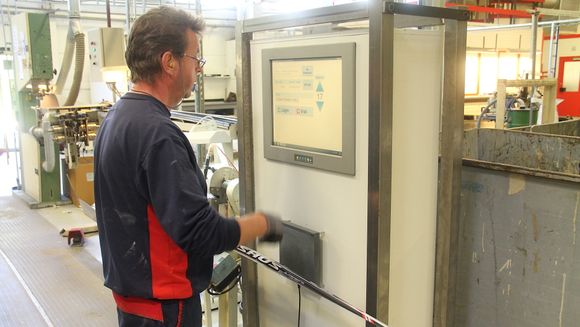
Norge mot Kina
Visjonen om smarte ski viste seg i 2006. I samarbeid med Forskningsrådet og Sintef ble det startet et fireårig prosjekt. Det viste seg raskt at Madshus var så tidlig ute at ideen ikke lot seg realisere den gang.
Da prosjektet gikk mot slutten ble de enige med Forskningsrådet om at det var verdt å fortsette, forteller Gunnar Bjertnæs. Han er tidligere teknisk direktør på Madshus og har ledet prosjektet. Nå er han delvis pensjonist og seniorrådgiver.
Madshus har ikke bare produksjon på Biri, men også i Kina. Der lages de rimelige modellene mens toppmodellene blir produsert i Norge.

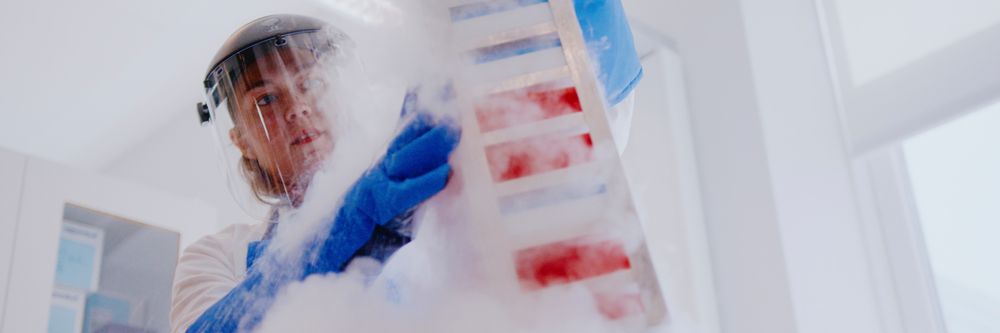
Skiprodusenten har to gode argumenter for det: De sitter på en kompetanse og ski-ekspertise få andre har, og de har systematisk gjennom mange år arbeidet frem et automatisert system som kan forsvare norske kostnader.
– For å overleve i Norge må vi tenke høyteknologi. Fabrikken vår i Kina er moderne, men likevel helt annerledes enn den vi har her på Biri, sier Bjertnæs.
Les om: Norsk industri er på et høyt nivå
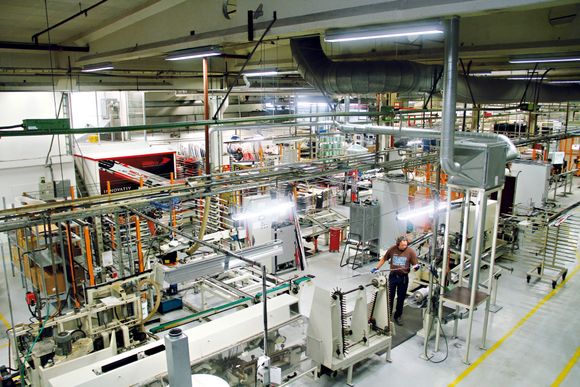
Tåler norske kostnader
Gjennom det snart åtte år lange samarbeidet med Sintef og utstyrsleverandører har Madshus utviklet en produksjonslinje som tåler norske kostnader. Nå er de klare for å vise frem resultatene, til tross for at enkelte ting ikke er på plass.
Ingeniørene jobber systematisk med digitalisering. Målet er å oppnå bedre fleksibilitet, stabilitet og å kunne håndtere materialene. Skumkjernen i en moderne ski er meget skjør, det kreves mye av roboter og styring for å kunne håndtere skumkjernene uten å skade dem.
– Leverandøren av skummet er tyske Evonik, de forteller oss at vi klarer maskinering og forming raskere enn de klarer selv, forteller Austrem.
Maskineringen av kjernen tar 10–15 sekunder per ski. Skummet kommer inn i plater som så kuttes og skjæres til. Stykker som er for korte kan enkelt skjøtes, det blir derfor lite kapp og svinn. Kjernen er viktig, formen skal stemme overens med ønsket geometri på skien.
Robotcellene kommer
Madshus har rundt 1200 skityper totalt. Austrem forteller at når de taster inn korrekt nummer, omstiller maskinen seg raskt og den riktige kjernen kommer ut. Deretter får kjernen forsterkningslag, i form av enten glassfiber eller karbonfiber på over- og undersiden. Det gir stivhet i lengderetning. Etter dette tres en strømpe på skien, igjen glass- eller karbonfiber.
– Her er det diagonale fibre, vi kaller det triaksial braiding, det gir torsjonsstivhet. Disse prosessene er manuelle og arbeidskrevende.
Austrem forteller at en robotcelle ble montert i 2013, og at planen er å montere tre robotceller til, en hvert år fremover.– Dette gjør at vi kan kjøre alle kombinasjoner av forsterkninger på kjernen, med unntak av braidingen, gjennom denne linjen.
Les også: Slik styres produksjonen av Audi A3
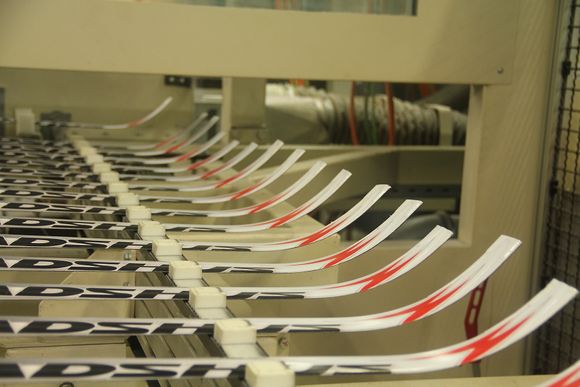
Fra tolv til to
Mens dette skjer blir dekoren forberedt. Madshus har også en teknikk som skiller seg fra konkurrentene, og det er absolutt fotoforbud. Prosessen foregår i et lukket rom.
De benytter digitaltrykk og en 0,25 mm folie av pleksiglass. Dekoren er trykket speilvendt på undersiden av folien. På folien limer de RFID-brikken.
Austrem forteller at det kun arbeider to personer med dette nå, tidligere var det 12 personer på trykkeriet.
De halvferdige skiene, med såle og folie, blir så lagt i store støpemaskiner, internt kalt karuseller. De ble utviklet og patentert av Bjertnæs på 80-tallet. Siden da er de blitt oppgradert, digitalisert og forbedret.
Les også: – Jeg tror vi får se en kraftig robotisering
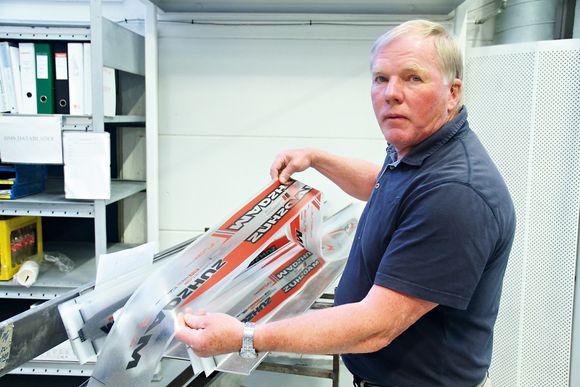
Krever fleksibilitet
Bjertnæs forteller at de er opptatt av muligheter for fremtidig oppgradering, forbedring og utvikling for alt av maskineriet.
– I tillegg ser vi på fleksibilitet, der stiller vi høye krav. Så må produksjonslinjen være rask og enkel å ta opp og ned. Alt maskineri må også kunne håndtere nye materialer, mye av råvarene vi bruker er ømfintlige og det er krevende for roboter og annet utstyr, sier han.
I de tre støpekarusellene kan Madshus håndtere 60 forskjellige skityper samtidig. Der blir det påført epoksy, som en tykk masse. Denne blir så varmet opp til 100 grader og det hele blir presset sammen med korrekt innstilt spenn. Sist følger kjøling, og nesten ferdige ski blir sendt ut. Også støpekarusellen er så full av egenutviklede lure løsninger at det ikke er lov å ta bilder.
Deretter er det sluttbehandling som består av en rekke automatiserte prosesser. Overskytende materiale skal skjæres av, sålene skal slipes, kanter likeså. Tuppene finjusteres, og feste for bindinger limes på. Til slutt skal skiene renses og poleres.