Aker Drillings nye borerigger konstrueres for å tåle værharde forhold.
Aker Drilling har bestilt to Aker H-6e rigger ved Aker Stord og har i tillegg opsjon på to til. Det er Aker fra ende til annen. Men andre leverandører nyter også godt av Akers aktivitet.
Rir på Kristin og Snorre
– Aker H-6e er bygget på erfaringene fra Snorre B og Kristin-plattformen. De gav oss et meget bra skrog, så dette konseptet bygger vi videre på. Det er selve byggemetoden vi nå høster erfaringer fra, sier prosjektleder Jan-Tore Elverhaug i Aker Kværner Engineeering and Technology.
Aker H-6e plattformene er ikke konstruert for å drive leteboring, men for å bore produksjonbrønner i værharde og arktiske strøk. Denne typen rigger er det mangel på i dag.
– Riggen en utstyrt med dobbelt ramrigg, som er særlig godt egnet for produksjonsboring. Denne typen rigg øker effektiviteten med over 20 prosent i forhold til rigger med ett boretårn, forteller Elverhaug.
Alt innendørs
Riggen er konstruert for å gå i arktiske strøk. Det setter spesielle krav til utformingen av dekket. Alt er innelukket og ekstra isolert. Elverhaug forteller at de ikke har bestemt om hele boretårnet skal lukkes inne, eller kun deler av det.

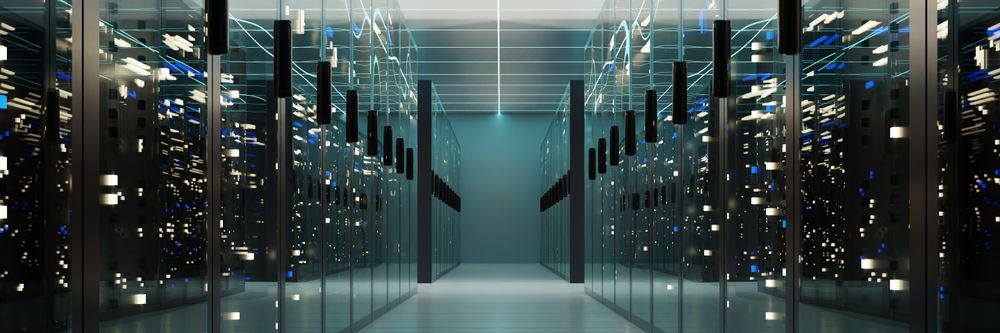
– Vi må se på hvilken skorsteinsvirkning vi får, sier han.
Alle rømningsveier er elekrisk oppvarmet. Oppholdsrom er ekstra isolert, og instrumenteringen er sertifisert for å kunne tåle de lave temperaturene. Alle rør er lagt innvendig i oppvarmede områder for å unngå ising.
Det er også andre krav som stilles når riggen skal bore i havområdene i nord. Det norske regelverket tillater ikke utslipp til sjø, rent bortsett fra det øverste topphullslaget av brønnen. Det betyr at borekaks fra de øverste 200 meterne av brønnen kan slippes på havbunnen.
All annen borekaks må fraktes til land for deponering. Så derfor går det et transportbånd fra slambehandlingsanlegget og til store lagertanker for borekaks. Denne borekaksen kan da enten reinjiseres i brønnen eller deponeres på land.
All borevæske må være vannbasert, i likhet med hydraulikkoljen som må være giftfri.
Sveises i Dubai
Opprinnelig skulle skroget bygges ved Aker Verdal. I oktober i fjor fikk imidlertid det trønderske verkstedet oppdraget med å å bygge skroget til Blind Faith-plattformenen for Chevron i Mexicogolfen, og dermed var det ingen ledig kapasitet i Verdalen.
– Jeg tror det er første gang et norsk verft bygger en rigg for en installasjon i Mexicogolfen. Det viser at vi er konkurransedyktige internasjonalt, men vi måtte ut å finne noen andre som kunne bygge skroget for oss, forteller Pål Lindstad i Aker Kværner. Han arbeder med utviklingen av selve konseptet for plattformen.
Så i stedet for Verdalen bygges skroget i Dubai. Men konstruksjon og detaljarbeider utføres av Brevik Engineering. – Vi har folk i Aker Konsernet som fortsatt har kompetanse på å konstruere skrog til borerigger. Det skal vi dra nytte av, understreker Lindstad.
Byggemetoden i sentrum
Selve dekket, som er 90 x 70 meter, skal bygges ved Aker Stord. Det bygges i seksjoner som settes sammen innendørs inntil det monteres på skroget. Blant anet skal alle hovedskjøter automatsveises.
– Vi er så heldige at vi har en stor dokk ved verftet. Den er fra den gang det ble bygget supertankere på Stord. Ved å utvide dokken noe, får vi plass til skroget i dokken. Dermed kan vi senke skroget ned og montere dekket på en enkel måte, sier Elverhaug.
Han kan fortelle at det er lagt ned mye arbeid i å finne den optimale byggemetoden. – Men vi har en het klar fordel av at vi kjenner verftet som bygger dekket svært godt. Det betyr at vi kan konstruere dekket basert på de verktøy og maskiner som finnes på Aker Stord.
I tillegg blir rørene bøyd ved Aker Verdal, hvor vi har et av verdens mest moderne kaldbøyingsmaskiner for rør. Alle disse elementene til sammen skal gi oss en god posisjon når det gjelder bygging og utvikling av store havgående borerigger. Vi håper at det skal kunne dane grunnlaget for en serieproduksjon ved Aker Stord.
Ubemannet boredekk
I Norge er regelen den at et boredekk skal være ubemannet.
Tidligere tider som gjerne glorfiseres på film eller dramatiseres i nyhetssendinger, med møkkete boredekksarbeidere, roughnecks, er fraværende på Aker H-6e. Her styres alt via skjermer i et temperert kontrollrom. Det gjelder også når rør skal heises på plass i fingerbrettet.
– Er det noe vi kan klage på, er det at det ikke er mulig å øke hastigheten på enkelte operasjoner. Det skyldes rett og slett at hydraulikksystemene har begrenset hastighet, forteller Lindstad.
Penger å spare
Men det viktigste utstyret på en borerigg er tross alt boreutstyret. Her slår Aker Drilling til med det beste de kan tilby gjennom Aker Maritime Hydraulics. Den dobbelte ramriggen har vist seg særdeles effektiv ved boring av produksjonsbrønner.
Smedvik har hatt denne boreinnretningen på boreskipet West Navion og boreriggen West Veture, som er langt mer effektive i sine boreoperasjoner enn andre rigger.
Tidsforbruket er redusert med mer enn 20 prosent. For en rigg som koster opp mot 3,5 millioner kroner dagen, er det fort penger å hente ved slike effektivitetsforbedringer
Ramriggen har to boretårn, ett for boring og et for brønnoperasjoner. Boretårnet for boring kan håndtere inn til 1000 tonn i kroken, mens det for tvillingen er mulig å håndtere 500 tonn.
Tankevekkende
For ingeniørene som konstruerer og følger opp byggingen av riggene, er det en helt annen situasjon enn å bygge produksjonsutstyr for offshoreplattformer. Riggene bygges etter høyeste klasse i Det Norske Veritas.
Det setter andre krav til dokumentasjon enn hva som er vanlig i annen oljevirksomhet til havs. I langt større grad kommer underleverandørene inn og deltar i utformingen av riggen, slik at den bir best mulig, samtidig som den blir enklere å operere og vedlikeholde.
– Ikke minst er dokumentasjonskravet langt enklere. Vi kan kjøpe utstyr som er sertifisert til å tilfredsstile kravene til DNV. Å fatte beslutninger er annerledes. Kunden stiller ikke med store lag som skal inn å kontrollere ned til minste detalj. Det er overlatt til oss som bygger. Og jeg er ikke sikker om vi får lavere kvalitet i verken produktet eller i gjennomføringen av prosjektet av den grunn, seier Elverhaug.
Stor lastekapasitet
Siden skroget i tidligere utførelser har hatt et tungt prosessdekk, som på Snorre B og Kristin, kan denne utførelsen bære en tung last, 7000 tonn.
Det er viktig dersom riggen skal operere i farvann langt fra baser. Det er derfor lagt vekt på å kunne lagre store mengder rør på dekk og i rørstativene for riggen.
Om bord på en borerigg er det til lagerplasser for rør, hver på 12 meter lengde. Et lager hvor alle rørene ligger horisontalt og et fingerstativ hvor rørene henger vertikalt. Det er disse som automatisk hentes til borestrengen og settes fast i denne.
Dersom borestrengen må trekkes opp på grunn av feil ved selve borekronen eller andre årsaker, settes rørene inn i fingerstativet. Til sammen 2700 meter rør kan få plass i dette fingerstativet.