I 130 år har Hunton vært en hjørnesteinsbedrift på Gjøvik. Hjemflaggingen av virksomheten i Polen kan bety mellom 40 og 60 nye arbeidsplasser i kommunen.
Selv om Hunton Fiber har en beskjeden andel av markedet i dag, er etterspørselen etter klimanøytral isolasjon økende, skal vi tro bedriftens ledere. Det foreløpige målet er en omsetning på 250–300 millioner kroner per år i Norden.
De dominerende aktørene på det norske isolasjonsmarkedet er franskeide Glava og danskeide Rockwool. Begge produserer mineralull basert på henholdsvis glassfibrer og steinull, og begge har milliardomsetning. Trefiberisolasjon er basert på treflis fra granskog.
Utnytter et avfallsprodukt
Den nye fabrikken til Hunton har to sluttprodukter: blåseisolasjon og isolasjonsmatter. Begge typer brukes til både nybygg og rehabilitering
Isolasjonsmattene til Hunton er noe hardere enn vanlig, mineralbasert isolasjon og må sages istedenfor å kuttes med kniv. Fordelen er at de ikke bukler seg så lett, og de verken klør eller gir ubehag i luftveiene for dem som jobber med dem. Ifølge Huntons målinger lydisolerer deres isolasjon bedre enn konkurrentenes. Trefiberisolasjonen har høyere densitet, det vil si mer masse per volum, noe som gjør at den absorberer og demper lyd i større grad enn annen isolasjon.
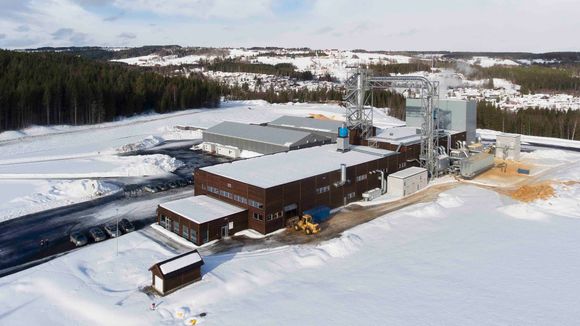
Trefiberisolasjon skal også gi et bedre inneklima fordi man slipper å bygge med dampsperre av tett plast. Fordi trefiber er et hygroskopisk materiale (det trekker til seg fuktighet), kan dampbrems benyttes i stedet. En dampbrems har som formål å bremse gjennomtrengning av damp fra innsiden, samtidig som den er åpen nok til at byggfukt kan tørke innover i rommet. Det gir raskere uttørking av overskuddsfuktighet.
Ifølge Hunton er dette spesielt godt egnet for fritidsboliger som står uoppvarmet i lengre perioder, og generelt for bygg hvor man ønsker et «godt og balansert inneklima».
Selve isolasjonsevnen skal være jevngod med konkurrentenes produkter.
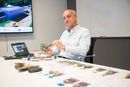
Tar avgjørelser på 400 mikrosekunder

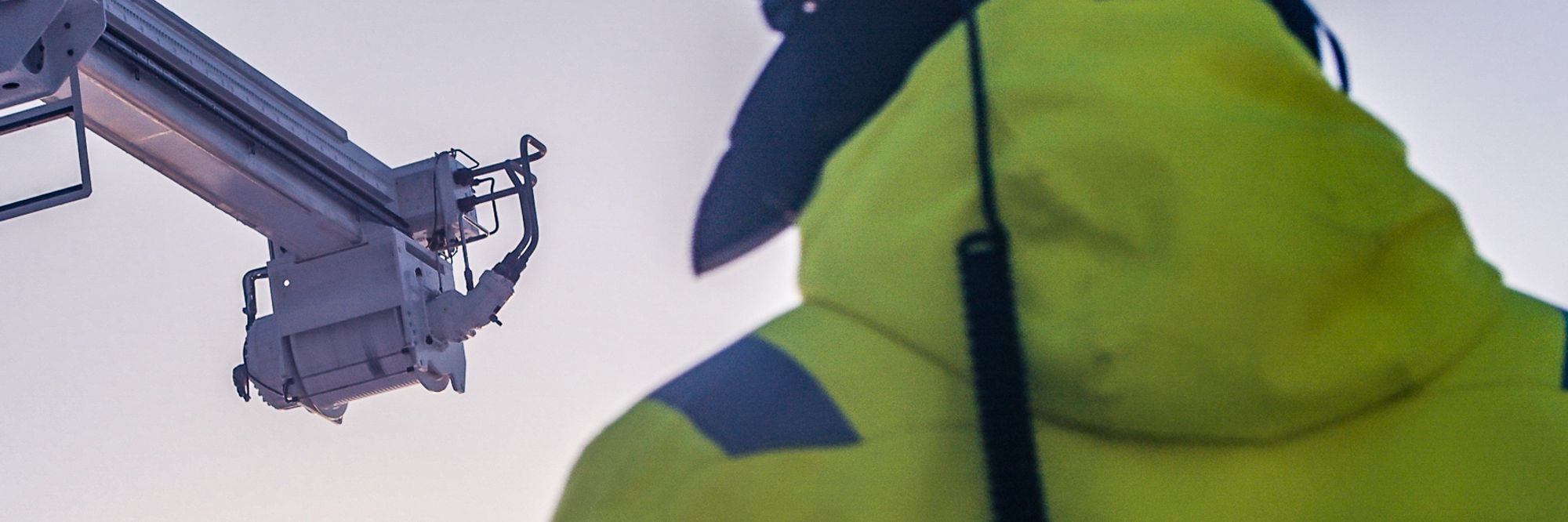
Både isolasjonsmatter og blåseisolalasjon fra Hunton er basert på trefiber fra granflis. I dag er produksjonen delt fifty-fifty mellom løs blåseisolasjon og hardpakkede isolasjonsmatter eller -plater (uttrykkene brukes om hverandre). Til sammen skal fabrikken kunne produsere cirka 100 kubikkmeter isolasjon i timen, eller rundt fem tonn. Det tilsvarer isolasjon til en gjennomsnittlig stor norsk enebolig i timen.
Ved full produksjon vil det gå med 70.000 kubikkmeter treflis per år. Treflis som ellers mest sannsynlig ville gått til spille som avfallsprodukt fra trelastindustrien.
– Vi lager et premiumprodukt av et avfallsprodukt, konstaterer Tom Wasenden, som er sjef for den nye fabrikken på Skjerven.
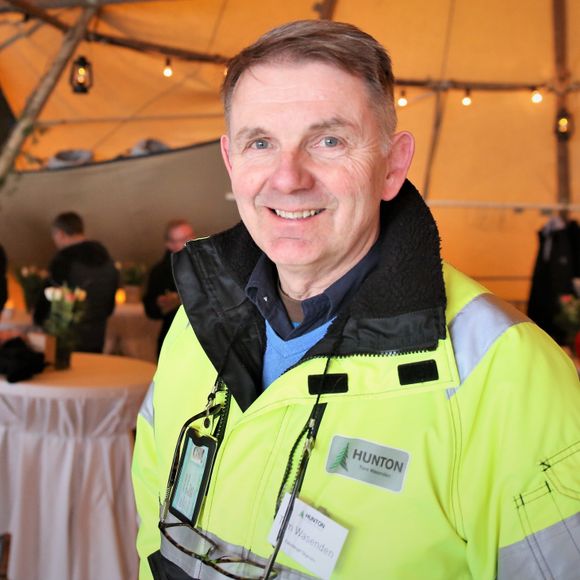
«Utdøende rase»
– Det som begrenser produksjonsvolumet, er raffinøren, hvor flisen blir malt opp og fiberen frigjort, sier fabrikksjefen og peker på en stor, blå installasjon i enden av lokalet.
Den er 22 meter høy og veier 200 tonn, opplyser han.
– Vi er heldige som har så gode raffinørkjørere fra gamlefabrikken. De hører nok til en utdøende rase, medgir Wasenden.
.png)
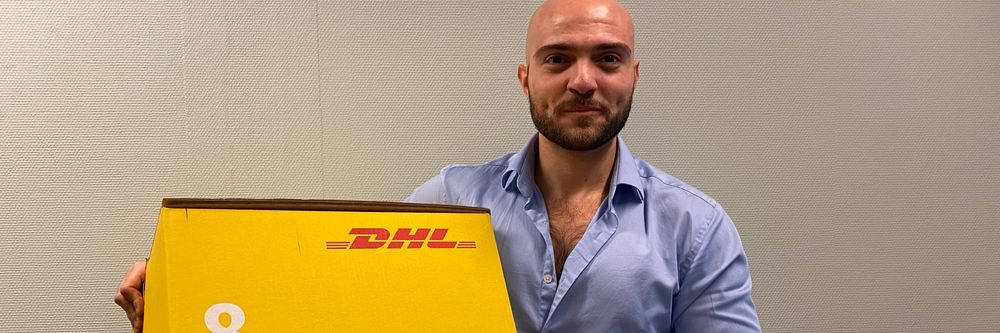
I raffineringsprosessen sørger et soldeverk for at overdimensjonert flis ikke blir med på ferden videre. Deretter plukker en kraftig magnet bort alle metallbiter, og en steinfelle eller vibrasjonsrist tar seg av jord og småstein som har sneket seg med på lastebilen fra sagbruket.
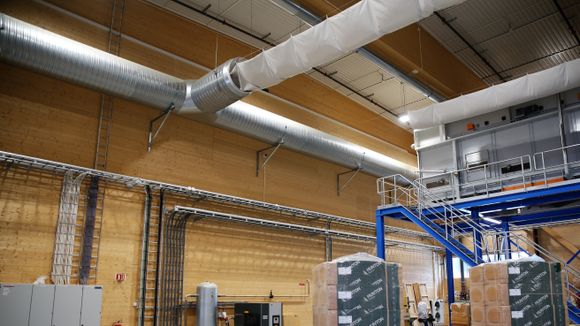
Det kanskje mest imponerende leddet i produksjonen er likevel tørkeprosessen – flashtørken. Den foregår ved at den rå flisen fra sagbruket blåses gjennom et 95 meter langt rør i hundre kilometer i timen. Røret er varmet opp til 180 grader, og etter å ha fått en runddans i et syklonrør oppe på taket, daler trefibrene pent ned i en bunker før de små fibrene skilles fra de store og fordeles til henholdsvis blåseisolasjon og plateisolasjon.
– Tørkeren vår har varmeelement på 6,9 megawatt, og er drevet av hundre prosent ren energi. Statnett-linja vår kommer rett fra vannkraftverket i Valdres, forteller Wasenden.
Takket være høy fart og temperatur tar det bare fem sekunder å tørke den rå granflisa. Flisen leveres fra omkringliggende sagbruk og kommer fra miljøsertifisert skog, hvor nye trær plantes etter hogst.
Roboter i aksjon
Mens blåseisolasjonen males fin og lett som nysnø, er fibrene til plateisolasjon på størrelse med tannpirkere. Det gjør at de binder seg lettere til hverandre. Som bindemiddel tilsettes en minimal mengde med bikomponenten Bico, som er fritt for miljøgifter, får vi opplyst.
Ved at blandingen varmes opp til 140 grader, smelter komponenten og fordeler seg jevnt i fibermassen før en maskin kjevler ut matter i ønsket tykkelse. Så kjøres mattene gjennom kaldluft, slik at bikomponenten stivner.
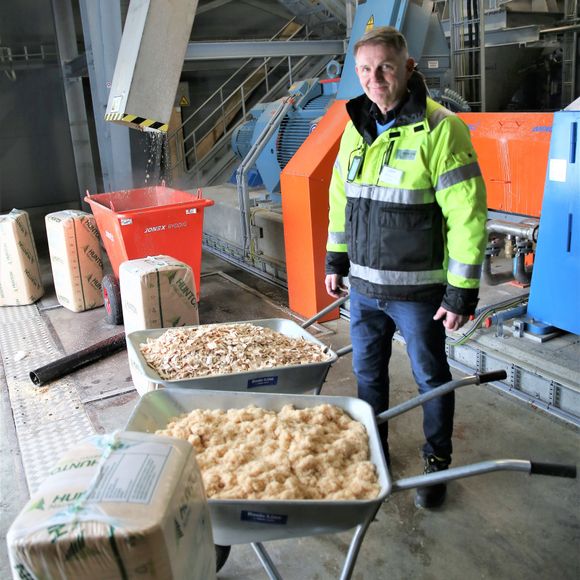
– Forsknings- og utviklingsavdelingen vår på Gjøvik jobber kontinuerlig med å minimere bruken av tilsetningsstoffer. Vi ønsker et så rent produkt som mulig, forklarer Wasenden.
Når fibrene er fordelt og plateisolasjonen skåret til, blir produktene pakket, stablet og merket i en helautomatisert prosess. Det eneste som involverer menneskehender i denne delen av produksjonen, er kontrollmåling av isolasjonspakkenes lengde samt frakten ut til lageret. Alt i alt er det ikke nødvendig med mer enn seks personer per skift.
Ettersom det tar tre timer å dra i gang alle maskinene, kjører de tre dager i strekk med tolvtimerskift nå i starten.
Denne videoen viser sluttprosessen i produksjonen av Huntons isolasjonsmatter:
Tom Wasenden forteller at før de begynte å bygge den nye fabrikken, reiste de rundt i Europa og så på fabrikker som driver med lignende produksjon.
– Det enkleste hadde vært å kjøpe en nøkkelferdig fabrikk, men vi fant ingen som kunne levere en produksjonslinje som dekket alle behovene våre. Derfor bestemte vi oss for å kjøpe maskiner fra forskjellige leverandører og sette dem sammen selv.
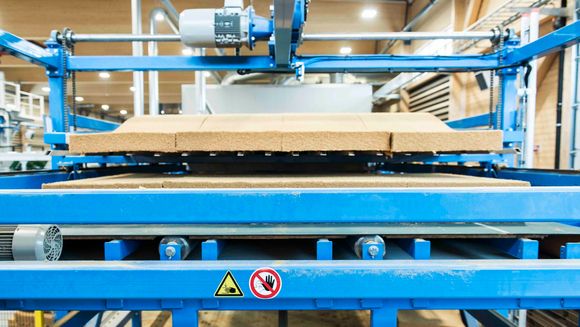
Det var en formidabel jobb å skru alt sammen, kan han fortelle, men alt gikk etter planen med god hjelp av egne og innleide maskinmontører.
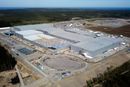
Northvolt sier opp 1600: – De har en cash burn som er helt ekstrem
– Fordelen er at vi nå kjenner utstyret vårt ut og inn. Det vil komme godt med ved vedlikehold og om vi skal skifte ut utstyr senere, sier Wasenden, som har jobbet hos Hunton siden 2008.
Reddet fra konkurs
Hunton er det første industriforetaket som etablerer seg på Skjerven utenfor Gjøvik. Det er ifølge ordfører Bjørn Iddberg starten på en ny næringsklynge i kommunen.
.jpg)
Det er på Skjerven Hunton skal produsere det mest kjente varemerket sitt, Hunton Nativo. Lokalene på 3200 kvadratmeter er bygget med Hunton-produkter og trevirke «så langt som det er mulig». Det har tatt vel to år å bygge fabrikken, og prisen endte på 250 millioner kroner.
– Egentlig er det nærmere 300 millioner – hvis vi tar med veier og alt vi har ordnet i området rundt, presiserer Huntons styreleder Frederik Mowinckel overfor TU Bygg.
Bergenseren har bakgrunn fra handels- og industribedrifter verden over og betegner seg som en «eco industrialist». Han var med på å kjøpe opp konkursboet etter at Hunton gikk konkurs tidlig på 90-tallet. I 1992 ble Hunton Fiber AS opprettet. Senere gikk også daværende markedsdirektør Arne Jebsen inn på eiersiden av bedriften, og Jebsen tiltrådte som administrerende direktør i 2009. I 2017 var selskapet oppe i 107 ansatte og driftsinntekter på 381 millioner.
Et søk hos Maxbo, en av forhandlerne av Hunton Nativo, viser at prisen for trefiberisolasjon er nesten dobbelt så høy som tilsvarende matter av glassull, som er det billigste alternativet.
.jpg)
– Forskjellen vil reduseres til rundt 20 prosent nå som vi har fått produksjonen hjem til Norge, anslår Runar Jacobsen, produksjonsdirektør i Hunton.
– Bidrar til å nå bærekraftmålene
Tirsdag 12. mars var det åpning av det nye produksjonsanlegget. Fabrikken ble offisielt innviet av statsminister Erna Solberg, som hadde følge av flere prominente gjester, blant andre Katharina Bramslev, daglig leder i Grønn Byggallianse.
– Hunton står for det vi kaller Paris-proof klimaregnskap, sa Bramslev fra talerstolen og siktet til bærekraftmålene i Paris-avtalen.
Huntons isolasjonsmaterialer er kun basert på fornybart trefiber, understreket hun, og ved å forlate Polen, hvor produksjonen har foregått de siste ti årene, er råmaterialet dessuten kortreist.
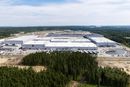
Batterigigant sliter: – En perfekt storm
– Huntons nye trefiberisolasjon vil kunne bidra til klimakutt både nasjonalt og internasjonalt, og jeg tror etterspørselen vil bli stor. Vi har nemlig utbyggere som lager stadig mer ambisiøse miljøstrategier, sa Bramslev.
«Ti tommeltotter»

I stedet for snorklipping fikk statsminister Erna Solberg æren av å åpne fabrikken ved å skjære over en isolasjonsmatte med sag. Før hun skred til verket holdt hun opp begge hendene og bekjentgjorde at hun dessverre er utstyrt med «ti tommeltotter».
– Jeg er ikke sikker på om jeg får jobb i skogbruket etter dette, spøkte hun etter at hun hadde delt isolasjonsmatten i to uten nevneverdige problemer.
– Det gikk lettere enn jeg hadde trodd. Jeg ble advart om at materialet er litt hardere enn steinull, sa hun.
Etter at alle talene og blomsteroverrekkelsene var overstått, fikk statsministeren en omvisning på fabrikken.
– Det er bare én lukt som overgår denne, og det er lukten av nyslått gress om våren, fastslo statsministeren da hun passerte treflismottaket i enden av fabrikken.
Denne videoen viser den robotiserte stablinga av de ferdige produktpakkene:
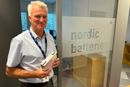
Vil tette «batterigap» med ny fabrikk