FARSUND: Hva har bilmerkene Porsche, Bentley, Mercedes –Benz, BMW, Land Rover, Rolls – Royce og Ferrari til felles?
De har avanserte aluminiumskomponenter fra Farsund. Årsak – Farsund Aluminium Castings (FAC) kan levere produkter som ingen andre støperier er i stand til å levere. De har en helt unik støpeteknologi som gjør at de kan støpe komponenter i et stykke stedet for at de må settes sammen av flere komponenter. – Vi kan levere det ingen andre kan. På grunn av vår teknologi og kompetanse kommer de til oss, sier driftsdirektør Rune Almaas.

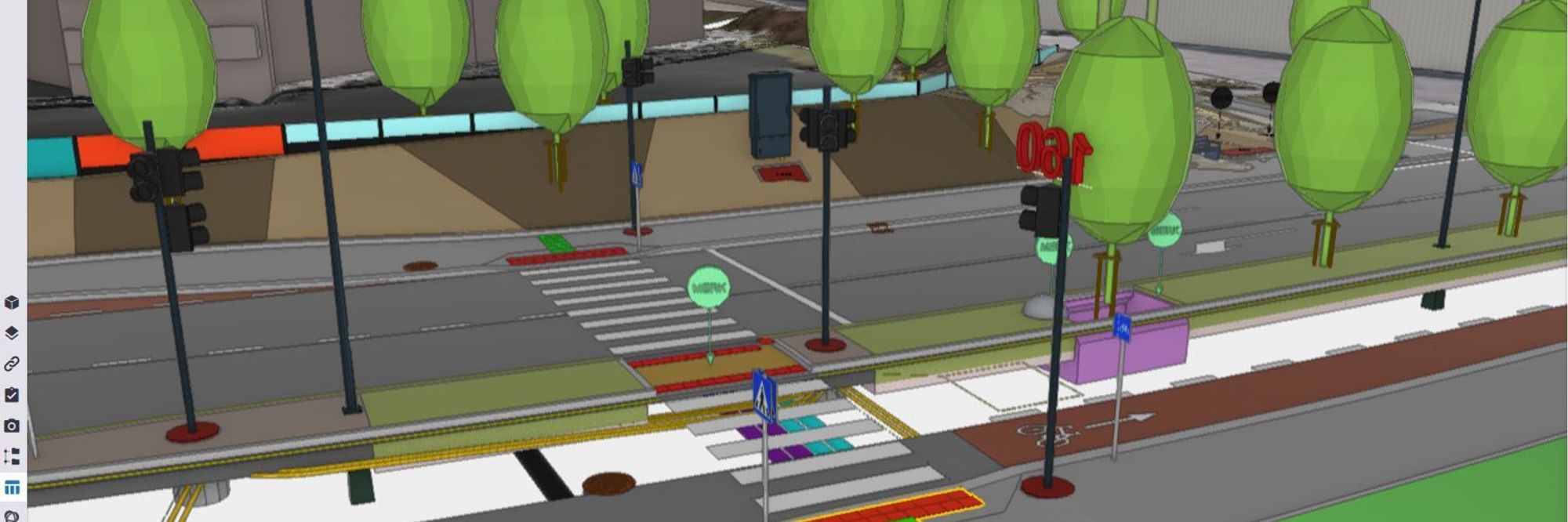
Startet med Volvo
FAC har en broket fortid. I 1996 besluttet Alcoa å investere i et avansert aluminiumsstøperi på Lista. Beliggenheten var god, kort vei til førsteklasses aluminium, kort vei til havner og sentrale Europa. I tillegg er det en flyplass på Lista.
Det hele startet med at Volvo ønsket aluminiumskomponenter til modellene S60, S80 og V70. – Det var sikkerhetskritiske understellskomponenter og i chassiset vi skulle levere. Det kom til oss på grunn av tre forskjellige elementer – Norge er verdensledende på aluminiumsteknologi, vi har meget god kvalitet på aluminiumen, og vi har tilgang på energi. I tillegg er vi gode i engelsk, noe som konkurrenter i Ungarn har vanskeligheter med, forteller dr.ing. Jan Ove Løland. Han er forsknings og utviklingsdirektør ved FAC.
Almaas forteller at utviklingen av anlegget gikk fort. – Vi hadde som mål å få første støping sommeren 1997. Det klarte vi, 30. juli kl. 23.15 var vi gang forteller han.
Reddet av teknologien
Men den globale finanskrisen krevde sitt, bilsalget stupte og støperiet på Lista fulgte med på lasset og bedriften gikk konkurs januar 2009. – Tre aluminiumsstøperier gikk konkurs omtrent samtidig, Det var oss på Lista, Fibo-støp i Holmestrand og Fundo Wheels på Høyanger. Vi hadde den fordelen av at vi hadde en unik teknologi som bilfabrikkene var interessert i, og vi fikk interessenter som så mulighetene for å starte opp igjen. Gjennom det tyske investeringsselskapet Widro GmbH og vår adm. direktør Roger Cockroft, så fikk vi kapital nok til å komme i gang igjen, forteller Almaas.
En av bilfabrikkene som de arbeidet med da konkursen inntraff var Daimler (Mercedes-Benz). Bedriften arbeidet med en spesiell komponent i chassiset som kunne støpes. – Vår støpeteknologi gjør det mulig å utvikle støpte deler med struktur slik at den tilfredsstiller kravene til støtabsorberende soner i bilen. Nå er heldigvis Daimler kommet tilbake igjen som kunde, forteller Løland.
Prestisjetung pris
I 2010 fikk FAC den europeiske aluminiumsprisen for et unikt stykke arbeid, hele bærebrua for bakhjulsopphenget til Porches luksusbil Panamera. – Denne støpes i et stykke. Det er så vidt oss bekjent ingen andre støperier som er i stand til å støpe en slik komplisert i en operasjon. Vår teknologi gjør at vi kan støpe store kompliserte løsninger som har en toleranse på pluss/minus 1 mm. I noen tilfeller mer nøyaktig enn dette også, sier Løland.
Rent metall
En av de store fordelene for FAC er at de får flytende ferdiglegert aluminium rett fra aluminiumsverket til Alcoa på Lista. Dette er et svært rent metall med mindre enn 0,07 prosent innhold av jern. – Forurensing av jern i aluminium er et problem for støperiene. Det er svært vanskelig å komme under dette fordi ovnene som brukes for å varme opp aluminiumet avgir noe jern, noe vi slipper. I tillegg har vi den fordelen at naboen Alcoa produserer svært rent metall som er meget godt egnet for støping, sier Almaas.
Han understreker også en annen fordel med nærheten til aluminiumsverket, tidsfaktoren. – Plasseringen her på Lista med kort avstand til Kristiansand og ferjeforbindelsen til kontinentet, så kan vi levere varer med kort gjennomløpstid, 14 dager fra aluminiumoksid til levert produkt i bil i Europa, forteller driftsdirektøren.

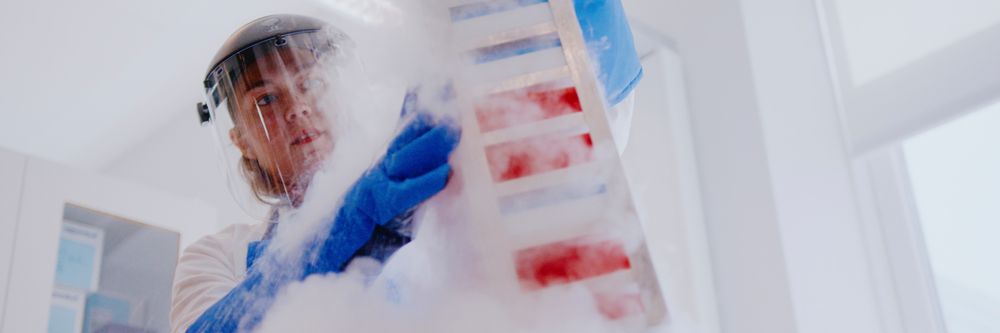
Avansert programvare
Støpeteknikken FAC brukes er lavtrykksstøping hvor metallet fylles fra bunnen av støpeformen. Teknologien er opprinnelig utviklet av Alcoa og kalles VRC/PRC (Vacuum Riserless Casting/ Pressure Riserless Casting), hvor man kombinerer både vakuum og trykk for å fylle formhulrommet i støpeverktøyet. I tillegg benyttes mange stigerør inn til formhulrommet og disse erstatter de vanlige materne som ellers måtte vært benyttet. Slik oppnår vi å bruke optimal mengde med metall, sikre en jevn kvalitet i støpen og oppnår maksimal renhet i metallet pluss at vi kan støpe kontinuerlig ved at vi etterfyller diglene kontinuerlig, forteller Løland.
Støpeformene er vannkjølte og sikrer rask nedkjøling av støpen. Det kan være inntil 90 individuelt kontrollerte kjølekretser i en støpeform for å sikre jevn avkjøling og et porefritt støpegods. – Vi har et unikt verktøy ”SutCast”, utviklet av en dr.ing. fra Iran, Dr. Reza Babaei, som simulerer støpeprosessen. Dette er bedre og raskere enn andre kommersielle programmer. Dermed kan vi kjøre flere simuleringer for å oppnå best mulig resultat i støpeprosessen, sier Løland.
Søker flere miljøer
Han legger til at de er i samarbeid med Steinar Sælid og Prediktor i Fredrikstad for å kunne bruke kunnskapen de har til optimal kontroll av støpeprosessene.
FAC samarbeider også med NTNU og SINTEF i Trondheim, Raufoss og på Møre og andre norske forskningsmiljøer pluss den svenske Gjuteriforeningen for å videreutvikle sin kompetanse. EYDE-nettverket på Sørlandet er også blitt en viktig arena for bedriften.