Goliat FPSO blir utstyrt med svært omfattende diagnostikkløsninger, som selvsagt er tilgjengelig både offshore og onshore i en enhetlig portalløsning (Ill. Eni Norge).
Da kan både vedlikeholdspersonell på flyteren (FPSO) og et nytt driftssenter i Hammerfest trolig ta pulsen på mer av det tekniske utstyret enn i tilsvarende anlegg.
Standardisert styring
Noen ganger kan det være smart å legge alle eggene i samme kurven, for maksimal homogenitet. Det tenkte operatøren Eni Norge da en og samme leverandør, ABB, våren 2010 fikk ansvaret for automatisering, instrumentering (inkludert ventiler), telekommunikasjon og elektro.
Eni spesifiserte kort tid etter at samme sikkerhets- og automatiseringssystem (ABB 800xA) og feltutstyr skulle benyttes i utstyrspakker fra alle relevante underleverandører. Resultatet er blant annet enhetlig SAS rund baut, med kun et par unntak. Uansett får både operatører og vedlikeholdspersonell et homogent system å forholde seg til, og grensesnittene mellom styringssystemene for de ulike delene på Goliat er sømløse.
- Endelig elektrodiagnostikk
Smidig drift er selvsagt avhengig av at alt utstyret spiller som forventet. Derfor blir omfattende diagnostikkinformasjon samlet i en portal, som både er tilgjengelig på flyteren og på land. Det er ikke bare tungt, roterende maskineri og utvalgt feltutstyr som skal under lupen.
- Vi har elektroniske nervetråder i alt produksjonsutstyr og hjelpesystemer, forteller Oddvar Ims hos Eni Norge til Automatisering. Han er ansvarlig for elektro, instrumentering, kontroll og telekommunikasjon i Goliat-prosjektet.
- Det blir også diagnostikkovervåking av feltinstrumentering og ventiler, via smarte ventilstillere, og selve automatiseringsutstyret, it-infrastrukturen og hele elektropakken.
Ståle Kristiansen, avdelingsleder for olje- og gass hos ABB, kommenterer litt spøkfullt at det endelig er noen som tar skrittet fullt ut med diagnostikkinformasjonen som de avanserte elektrostyringssystemene har. Integrasjonen mot kontrollsystemet snurrer via protokollene IEC 61850 (vern), Profinet IO (motorer og varmeelementer) og ABBs Drive Bus (drives).

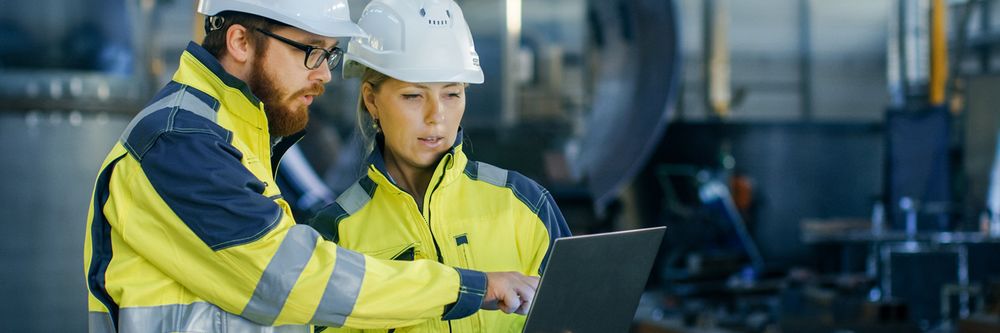
Overvåker ytelsene
Sentral styringstrio flankerer en av tre operatørarbeidsplasser, fra venstre, Ståle Kristiansen (avdelingsleder for olje og gass i ABB), Thomas Lier-Nilsen (prosjektleder i ABB) og Oddvar Ims (ansvarlig for elektro, instrumentering, kontroll og telekommunikasjon i Goliat-prosjektet hos Eni Norge).
Eni har blant annet tatt det samme grepet som BP på Skarv FPSO og den nye prosessplattformen på Valhall-feltet (se automatisering.org, søkeord ertt), nemlig ekstra instrumentering på utstyr som varmevekslere, hvis primæroppgave er tilstandsovervåking og ytelsesmåling.
- Rundt 200 objekter, som kompressorer og varmevekslere, blir utstyrt med modellbasert ytelsesovervåking. Eventuelle avvik mellom virkelige og forventede ytelser fra modellene blir varslet, med forslag til aksjoner, forklarer Oddvar Ims.
Trådløs motorovervåking
Men overvåkingspolitet stopper ikke der. Kompressorer og turbiner har selvsagt konvensjonell, trådbunden vibrasjonsovervåking. Men Eni har også vært raus med overvåking av mindre kritiske motorer. Nærmere 300 vibrasjonssensorer blir installert på flyteren i trådløse maskenettverk.
- Elektriske motorer blir utstyrt med ABBs Wimon 100 vibrasjonssensor, som kjører på WirelessHart, sier Ims.
De trådløse agentene rapporterer frekvensspekteret regelmessig. Informasjonen samles i et felles vibrasjonsovervåkingssystem som også har data fra de trådbundne sensorene. Løsningen passer som hånd i hanske for Enis kongstanke om at all vedlikeholdsinformasjon aggregeres til en felles portal. Prosjektleder Thomas Lier-Nilsen hos ABB låner kanskje et sitat fra en eller annen salgsbrosjyre da han forklarer at det handler om riktig data, til riktig person, til riktig tid. Men sjelden har uttalelsen stemt bedre.
Hjerte for Hart
Et at de store stridsspørsmålene tidlig i prosjektet var hvordan diagnostikkinformasjon fra feltutstyret skulle overføres til kontrollsystemet, for videre slusing til vedlikeholdsportalen. Oddvar Ims i Eni forteller at de var litt giret på FF (Fieldbus Foundation) i starten av prosjektet.
- Vi hadde FF som opsjon i forespørselen, da vi ikke ville snevre inn valgmuligheten, sier han.
- Etter valg av ABB som hovedleverandører, bestemte vi oss for å benytte den mest vanlige løsningen i Nordsjøen, nemlig distribuert I/O og overlagret Hart på strømsløyfene til feltutstyret.
Tar ventilfotavtrykk
Goliat blir delvis forsynt med landsstrøm, som blir levert via denne stasjonen på Hyggevatn. Et par SAS-noder blir installert her også. En redundant fiberkabel er integrert i strømkabelen som kommunikasjon mellom flyteren og onshore driftssenteret i Hammerfest (Ill. Eni Norge).
Prosessinstrumenter fra blant annet ABB og underleverandør Krohne, og over 800 smarte ventilstillere fra Metso kommuniserer via Hart. Alle pneumatisk styrte regulerings-, av/på- og nødavstengingsventiler blir utstyrt med teknologien, som overvåker og rapporterer rikets tilstand.
- Vi har satset på maksimal diagnostikk for ventilene, forteller Ims.
- Ventilleverandøren Solberg & Andersen logger for eksempel fotavtrykket, det vil si kraften som er nødvendig for å bevege ventilene, før oppstart. Når en ventil en gang i framtiden trenger med kraft for å flytte seg, blir vi varslet gjennom vedlikeholdsportalen.
Stor SAS
Sikkerhets- og automatiseringssystemet (SAS) består av 75 ABB kontrollere, som inkluderer to onshore (for landkraften, en hybridløsning med høyspent vekselstrøm fra land og gassturbin offshore) og fem mot undervannssystemene. Pakkeleverandørenes kontrollere er inkludert i tellingen. Totalt sett utgjør prosesskontrollnodene to tredeler av maskinparken. Det er 11 000 fysiske signaler tilkoplet SAS, men grunnet omfattende kollektivtrafikk (signaler på buss), er antall objekter langt større.
Robust med redundans
Goliat skal i drift i det høye nord, og er designet for drift i ekstremt vær og mørke (Ill. Eni Norge).
Kommunikasjonen med nodene offshore og driftssenteret på land gjøres primært gjennom en redundant fiber som er bygd inn i kraftkabelen. En radiolinjeløsning brukes som backup-kommunikasjon, om fibrene skulle svikte.
Alle kontrollerne har redundant CPU (central processing unit). Foruten høyere tilgjengelighet, har tilnærmingen har vært kjekk i en flat verden (hvor engineering kan gjøres globalt). Leverandøren har nemlig splittet nodene i prosjektfasen. Den ene CPU-delen står i Oslo, og den andre i India, hvor majoriteten av programmeringen og skapbygging blir gjort. I tidligere SAS-leveranser ble gjerne hele systemet satt opp for en komplett fabrikktest (FAT) hos leverandøren. Det tillater ikke tidsskjemaet. Nå møtes hele systemet på flyteren ved verftet i Korea.
Virtualiseringsfordeler
Virtualisering av serverparken er et annet tegn i tiden. Goliat følger opp, og implementerer teknologien. Hele systemet kjører på syv virtualiserte vertsservere. Ståle Kristiansen, avdelingsleder for olje- og gass hos ABB, anslår at antall servere ville vært firedoblet uten løsningen. Teknologien sparer altså både penger, plass og energi, både for drift og kjøling.
Historiske data blir lagret i en prosessdatabase fra ABB. Informasjonen blir speilet til en onshore database (PI) fra Osisoft, som er Enis globale sanntidsinfrastruktur.
Enhetlig operatørgrensesnitt
Eni har ikke gått for en storskjermsløsning i det sentrale kontrollrommet. I stedet har selskapet standardisert på ABBs utvidede operatørarbeidsplass, EOW (extended operator workplace). Ergonomien er i høysetet, og alle gode ting er tre.
- Vi valgte tre komplette operatørarbeidsplasser fra SAS-leverandøren i samråd med operatørene, forteller Oddvar Ims hos Eni Norge, som er ansvarlig for elektro, instrumentering, kontroll og telekommunikasjon i Goliat-prosjektet.
- Hver arbeidsplass har tre 52 tommers skjermer øverst og seks 23 tommers skjermer foran operatøren, alle i 16:9 bredskjermsformat.
- Operatørplassen har en rekke innstillingsmuligheter, og har blant annet en lyddusj som kan aktiveres for akustisk isolasjon.
Det vil sitte to operatører fast i kontrollrommet offshore. I tillegg er det tilrettelagt for en tredje operatør i situasjoner hvor det er påkrevd.