Bruchsal, Tyskland: Konstruktørene hadde lagt seg skikkelig i selen for å bygge verdens mest avanserte fabrikk i sin klasse.
Les også: Norfersk kjøttpakkesenter sprer ferskvare på en helt ny måte
Solskinnsproduksjon
Kommunikasjonssjef Stefan Brill forteller at miljøvennlighet var en av ledestjernene, og at de derfor installerte både solcellepaneler, solfangere og et innsamlingssystem for regnvann for bruk i produksjonen.
Strømlinjeformet produksjon var den andre store ledestjernen. Fabrikken produserer kun til bestilling. Det betyr små serier, ofte bare ett gir. De kaller konseptet enstykksflyt (One Piece Flow).
- Det hele styres av et overordnet produksjonsplanleggingssystem etter sugeprinsippet, forklarer Brill.
Les også: Roboter revolusjonerer i potetbingen, Hvebergsmoen Potetpakkeri pakker 40 000 tonn årlig
Rundebordscockpit
Kundebestillinger blir håndtert av et ordresenter. Avdelingsleder Stefan Rammelspacher forteller at fabrikken benytter et softwarebasert planleggingsverktøy som cockpit. Han drar paralleller til en rundebordskonferanse, men bordet er altså virtuelt.

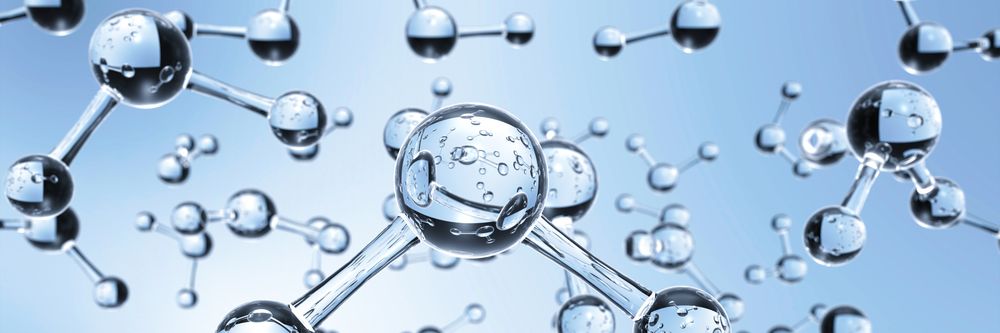
- Hos oss gjør skjermene jobben for det tverrfaglige teamet, sier Rammelspacher.
Operatørene finplanlegger hver eneste bestilling i systemet. Deretter kjører de simuleringer for å avdekke eventuelle flaskehalser. Både maskiner, lakkeringsverksted, deler og feltoperatører må være tilgjengelig. Hastebestillinger kan utføres på fem arbeidsdager.
Les også: Duun Industrier satser frist på robotsveis
Automatisk forflytning
Selv om de store og tunge industrigirene er bygget opp etter modulprinsippet, er helautomatisk produksjon neppe økonomisk forsvarlig. Det er allikevel nesten folketomt i de store produksjonslokalene.
For tyskerne har tatt solide grep for å automatisere flyttingen av deler, mellomvarer og ferdigprodukter på fabrikken. Deler for bestillingene plukkes automatisk, blant annet fra store høylagre, med heiser som farer rundt. Her går alt for seg med tysk presisjon og grundighet.
Logistikktog med vogner som trekkes av små trucker fylles opp med deler og distribuerer til aktuelt sted til rett tid.
Les også: Hver 10. "ansatt" hos Ekornes er en robot
Kontaktløs energioverføring
SEW Eurodrive har tatt i bruk rundt 1000 egne drives for å håndtere forflytning på vogner og langs palett- og transportbaner. De knallrøde motorene med integrert styring stikker seg fram overalt. Ifølge kommunikasjonssjef Stefan Brill er det blant annet en kilometer med baner som distribuerer deler fra høylageret.
Det mest fascinerende er likevel de førerløse vognene som frakter deler rundt på anlegget, uten fysisk overføring av energi eller signaler med moder jord. Her har også selskapet kjørt hardt på med egenmedisinering. Brill forteller at Movitrans har kontaktløs, induktiv energioverføring.
- Det er fast installerte elektriske ledere som brukes av en eller flere mobile brukere, eller vogner, forklarer han.
Det samme prinsippet benytter selskapet for lading av kjøretøy, både to- og firehjulinger, eller elektriske sykler og biler. I framtiden kan vi slippe mange av kablene som benyttes for lading av elektriske biler.
Les også: Robotduo pakker hundepølser uten menneskelig assistanse