ÅRDAL: I 2005 fikk årdalssamfunnet nærmest kniven på strupen, Hydros aluminiumsverk Årdal Metallverk skulle stenges ned. Nå var dette en sannhet med store modifikasjoner, men den såkalte Søderberg-hallen, ÅIII, måtte stenges ned på grunn av at utslippstillatelsene gikk ut og at myndighetene ikke ville fornye disse.
I stedet for å bygge en ny produksjonslinje med ny teknologi i Årdal, lik den som Hydro bygde på Sunndalsøra, så valgte Hydro å bygge et helt nytt aluminiumsverk i Qatar. Det var ikke tilgjengelig kraft nok til å bygge et nytt anlegg i Årdal. Daværende konsernsjef Eivind Reiten understreket at skulle Hydro bygge ut i Norge, måtte utbyggingen bli så stor at den uansett var i verdensklasse, hvis ikke ville det ikke være lønnsomt.
Måtte spare
Selv om den nyeste produksjonslinjen på Årdal skulle fortsette, var verket presset økonomisk. Driftskostnadene måtte ned skulle verket ha en mulighet til å kunne overleve. Først ble det satt en målsetting om å spare inn 100 millioner kroner, men dette ble forsterket, slik at metallverket nå må spare i 300 millioner kroner, eller 600 kroner (100 dollar) per tonn produsert aluminum.
– Aluminiumsverket her i Årdal har høye kostnader, noe som skyldes lønn og lønnsutviklingen i Norge samt høye energipriser. Med en høy kostnadsbase måtte vi finne metoder for å bli internasjonalt konkurransedyktige, forteller verksdirektør Olaf Wigstøl.
Lean produksjon
Hydro har sitt eget program for å effektivisere verket. Det går under navnet AMPS( Aluminium metal production system), som er bygget på lean prinsippet.. Lean har sin opprinnelse hos Toyota og stiller spørsmålet, hva er minimum innsats som kreves for å oppnå effektiv drift og høy kvalitet. – For oss innebar det at vi måtte se hva vi kan gjøre for effektivisere produksjonen, noe som innebærer at vi må se om vi har optimal bemanning, optimalisere prosessen og redusere feil i produksjonen slik at vi ble mer effektive, sier Wigstøl.

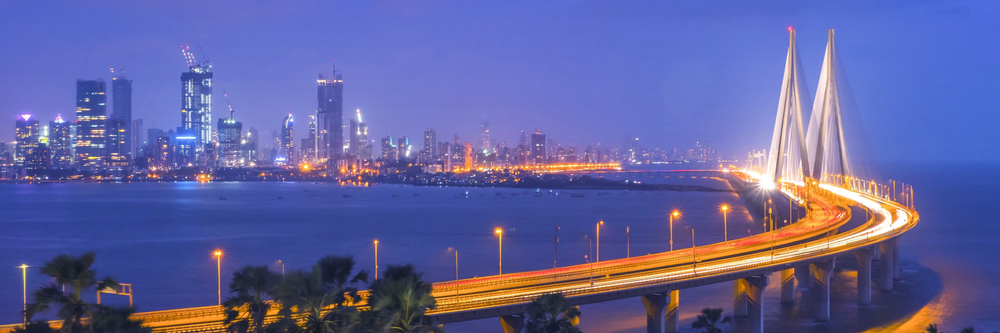
Vanligvis når bemanningen reduseres vil reduksjonen primært være antall driftsansatte. Men for å skape en balanse mellom operatører og stab, har vi redusert på stab og indirekte tjenester . – Vi må ha en flatere organisasjon, hvor større ansvar legges på den enkelte medarbeider ute i driften. En del av det tradisjonelle byråkratiet ble derfor fjernet. Dette er AMPS i praksis, og erfaringene vi har så langt viser at dette har virket positivt. Den enkelte ansatte føler større tilhørighet og er i større grad med på å bestemme over sin egen arbeidsdag, forteller Wigstøl.
– Alle er med på å finne og løse problemer, sier han.
Vekk med byråkratiet
I stedet for å ha en stor organisasjon med tunge administrative prosesser og byråkrati, og hvor løsningene kommer fra stabs organisasjonene, ble arbeidsoppgavene fordelt i forbedringsgrupper. Gruppene er mulitidispline og sammensatt av folk fra flere fag. Her skal gruppen vurdere forbedringer i prosessene, fjerne konkrete problemer og forbedre arbeidsrutiner. – Vi tror på kontinuerlige forbedringer. Vi har en klokkertro på at alle våre ansatte har noe positivt å bidra med. De som har sitt daglige virke i produksjonen vet hva som må gjøres for å forbedre tilstanden og produktiviteten i anlegget.
– Hele arbeidet som er lagt i forbedringsprosessen, AMPS, er langsiktig. Hva kan vi gjøre i dag som forbedrer oss i morgen? Hva er minimumskravene? Hele tiden må vi holde en stram linje for å sikre at kostnadene ikke løper løpsk. For i gode tider er det ofte en tendens til at bedrifter eser ut og legger på seg. Med å jobbe systematisk og langsiktig med forbedrnger etter AMPS modellen, vil vi unngå store nedbemanninger og superslanking av bedriften. Det er uheldig og en uønsket situasjon, sier Wigstøl.
Driftstavler
Før hvert skiftlag starter dagens arbeid, samles de foran driftstavlene for å gå gjennom dagens oppgaver og hva som kan forbedres. På dette møtet, som stort sett er kort, så fastlegges den enkeltes arbeidsoppgaver for dagen, det være seg driftsoppgaver, eller om det vedlikeholdsoppgaver som må gjennomføres.
– Vi kartlegger feil på en helt annen måte enn tidligere. Nå ser vi på hva som er gjengangere og hva som er enkeltstående tilfeller når det gjelder tekniske feil. Slik kan vi planlegge vedlikeholdet bedre, gjøre nødvendige korreksjoner i produksjonen og dermed oppnå større regularitet i de enkelte produksjonsledd, sier forbedrings sjef Odd Steinar Natvik.
Feilraten kraftig redusert
Et av de områdene som det er lagt stor vekt på å forbedre er produksjonen i anodefabrikken på Årdalstangen. Små feil ved anodene kan medføre store produksjonsavvik i produksjonscellene, noe som går ut over produktiviteten ved verket. – Vi har sett på alle ledd i bedriften. Vi har fått ned feilraten fra 10 til 3,5 prosent. Dette gir bedre drift og vi kan få ned kostnadene, sier Natvik.
Rutinene ble også lagt om for anodemontasjen. – Her måtte vi gjennom en hestekur. Men resultatene er gode. Vi klarer å øke produksjonen, vi får bedre styring på prosessen, fordi forholdene i de enkelte produksjonscellene varierer langt mindre enn tidligere. Små prosesstekniske forbedringer gir resultater, forteller Natvik.
Minus 23 millioner
Et viktig element i dette er de store driftstavlene hvor en rekke nøkkelparameter skrives opp og måles mot de målsettingene som er satt. Her kan vært enkelt arbeidsskift se hva deres innsats betyr. – Internkonkurranse mellom skriften er viktig. Her kommer yrkesstoltheten fram og ikke minst øker det tilhørigheten til bedriften. Totalt har vi redusert vårt kraftforbruk iår fra 14,6 kWh per kilo metall til 14,3 kWh per kilo metall, og målet er å komme ned i 14.2. Det alene sørger for at vi sparer 23 millioner kroner i årlige energiutgifter, sier Olaf Wigstøl.
Medarbeiderne er nøkkelen
Wigstøl legger vekt på at det skal være en synlig ledelse både internt og eksternt. – Hver dag må ledelsen ut i bedriften ogi kommunisere med de som daglig drifter anleggene, for å få en bedre forståelse for problemene i prosesser og skape forståelse og engasjement om sikkerhet og kvalitet på arbeidsplassen. Arbeidsplassene blir sikrere med standardiserte prosesser og rutiner, og danner grunnlaget for optimal kvalitet. Med å få en god dialog omkring forbedringer, og aktiv bruk av AMPS, skaper man grunnlaget for å få fram det store ubenyttede potensialet som ligger i kompetansen og kunnskapen hos våre medarbeidere, sier han.
Ved Årdal Metallverk er ledelsesfunksjonen rendyrket. Det faglige blir håndtert av fageksperter som er tilgjengelige for alle arbeidsgrupper. Gjennom den flate organisasjonen er 120 stillinger fjernet. Skal kravet om å nå en kostnadsreduksjon på 300 millioner kroner i løpet av to år nås, må ytterligere 25 – 30 årsverk reduseres. . Da er antallet ansatte kommet ned i ca. 620 medarbeidere.
Færre personskader
Omfattende sikkerhetsarbeid er gjennomført som følge driftsomleggingen. De ansattes bevegelser, og den interne logistikken er gjennomgått og forbedret. Ved hver start på arbeidsdagen gjennomgås sikkerhetsrutiner sammen med arbeidsoppgavene. – I tillegg til alt dette har hver enkelt medarbeider fått sin dedikerte plass i organisasjonen. De føler større tilhørighet og ansvar for å nå de oppsatte mål og resultater. Det ikke lenger så lett å la være å gå på jobb, og det er langt færre fraværskader enn tidligere. Hittil i år har vi hatt 750 000 timer uten en personskade i bedriften, sier Odd Steinar Natvik.