Water is a major challenge for oil producers. Too much produced water on older platforms, because the water cut has become high, means low production capacity and may prevent new and smaller fields coming into production. Kværner Process Systems (KPS), in collaboration with Statoil, Hydro and BP, has developed a new coalescer that gives older platforms extended lifetimes. The Compact Electrostatic Coalescer, (CEC) can operate under both high and low pressure as well as be installed on subsea installations. In other words, the CEC can also be placed ahead of a first-stage separator.
"Previously the electrostatic coalescer was always placed at the final stage of a separation process. This is probably because it was the most complicated unit, and the oil companies wanted to protect it by installing it where the pressure is lowest," says Arne Gulbraar of KPS.
Larger water droplets
A coalescer's primary task is to increase the size of the water droplets in an oil-water fluid flow. The coalescer is not very effective if there is gas in the fluid flow.
"Using a CEC on subsea wells can reduce the need for chemicals in and thus provide a far greener solution for field developments. All the chemicals that have to be added to prevent the formation of hydrates that can stop up a pipeline can be eliminated when using a CEC.
In use on Petrojarl 1
KPS has designed CEC to fit into a standard four or six-slot subsea template. A CEC can have the capacity to treat up to 35,000 barrels of well stream per day. Excess water can be returned to the reservoir via an injection pump installed on the same template.
Statoil has already put the new coalescer to use on board the FPSO Petrojarl 1, which is to produce oil from the Glitne field. The coalescer has been placed between the third and fourth stage separators on the ship. The CEC is a simple flow-through unit that has neither temperature gauges, volume gauges nor level gauges.
"That is why it can easily fit into existing process facilities and help to raise the production rates of marginal and mature fields," Gulbraar points out.
Horizontal tank
The CEC consists of a horizontal tank with tube-shaped channels that can vary with the volume that is to flow through the coalescer. Each of the channels has anodes that create the electrostatic field that causes the oil droplets to coalesce. Because the number of channels varies with the volume of fluid that flows through, there will always be consistency in droplet formation in the coalescer. The technology also involves a specially developed insulation system that ensures that the CEC avoids short circuits.

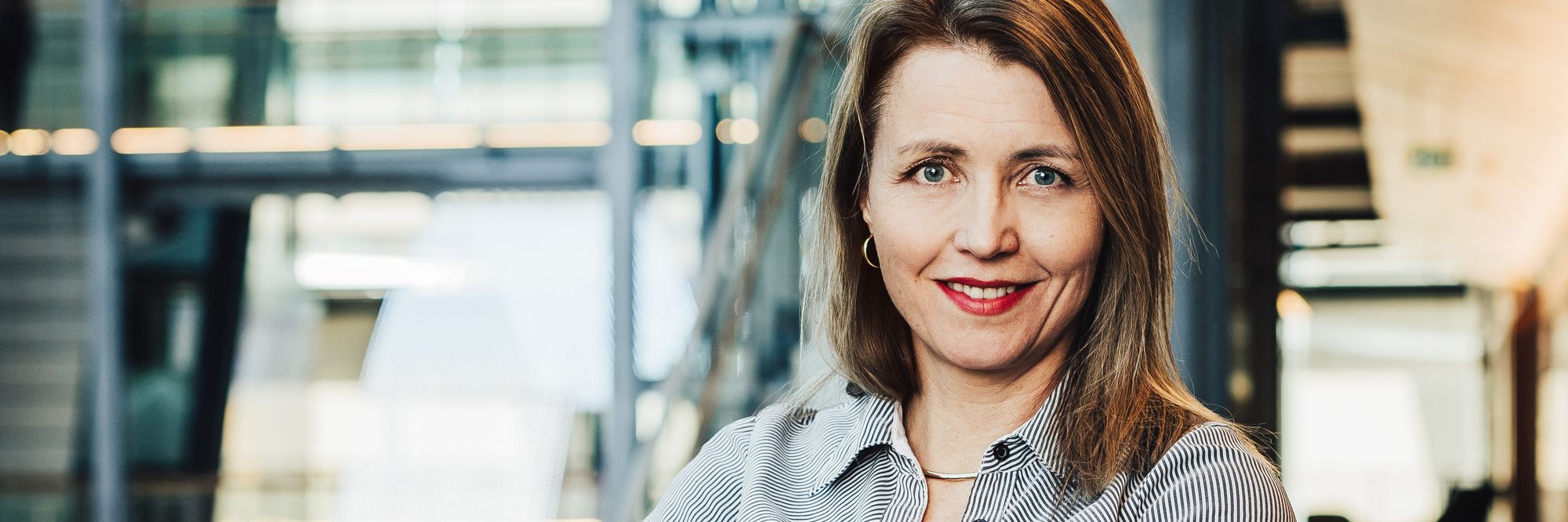
The fluid flows through from the top of the CEC. The electrostatic field causes larger water droplets to form. From the CEC the fluid enters an ordinary gravity separator to separate the water and oil. The time it takes to go through the CEC is only 10 seconds.
Compared with hydroclyclones, the CEC is more efficient. It can operate under a far wider variation in water volume and tolerates much larger water cuts than is the case with today's technology.
Advantages of the CEC:
Compact, low weight
Low installation cost
Simple design
Can be used under high pressure
Collects water droplets efficiently with low energy consumption

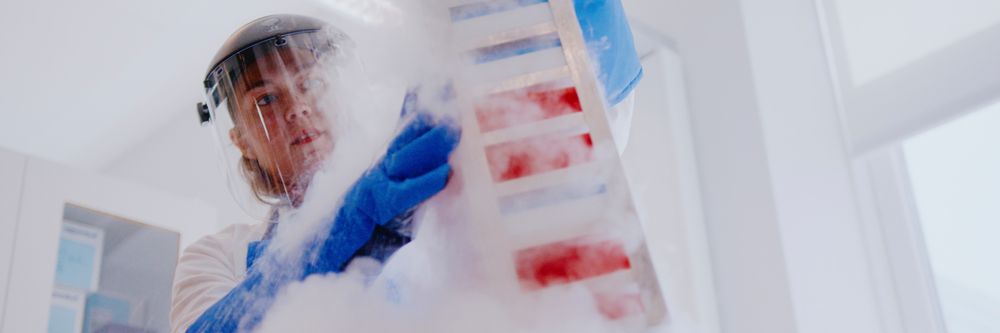
No moving parts
Reduces the need for chemicals
Can be used on subsea installations