Lav effektivitet på utstyret (OEE, Overall Equipment Effectiveness) og sløsing med materialer er hovedårsaken til (for) høye produksjonskostnader i svært mange bedrifter. Vi har tidligere nevnt at OEE i norske produksjonsbedrifter ofte ligger i området 20 til 40 prosent.
Tapsanalyse
Det betyr at 60 til 80 prosent av tiden operatørene betales for å være på jobb, ikke gir inntjening til bedriften! Dersom vi i tillegg taper materialer under produksjonen, blir kostnadsbildet enda verre. Analyseres i tillegg hvilken verdiskapning arbeidsoppgavene til den enkelte i produksjonen bidrar med, blir ofte bildet riktig skremmende.
Måling av OEE er en del av tapsanalysen. Tapsanalyse går ut på å kartlegge hvor det tapes penger i produksjonen, med utgangspunkt i det maksimalt teoretisk mulige utbyttet fra produksjonen; basert på utstyrets designede kapasitet, 100 prosent feilfrie produkter og 100 prosent utnyttelse av materialene.
Et viktig poeng, i tapsanalysen, er å omgjøre alle tap til kroner og øre, slik at vi kan sammenlikne alle tap på samme grunnlag. Konvertering av alle tap til penger gjør det også lettere å prioritere forbedringsaktiviteter og investeringer, i tillegg til at det blir lettere å beregne hvilke kostnadsmessige resultater forbedringer og investeringer har gitt. På den måten blir forbedringsaktivitetene i produksjonen omgjort til et språk også økonomene (ledelsen, styret etc.) forstår.
Riktig registrering
Selv om OEE er en vital parameter i produksjonen, er det bare et ”tall”. Det forteller ikke hvor skoen trykker. Tapsanalysen er løsningen. Den viser hvorfor OEE ikke er 100 prosent. Mens OEE kan beregnes relativt enkelt ut fra produsert volum, tilgjengelig tid og linjens designhastighet, krever tapsanalysen detaljert registrering av årsakene til tapt effektivitet. Denne registreringen kan kun gjøres i umiddelbar nærhet til der problemene oppstår, og av de som ser problemene; på produksjonslinjen av operatørene.
For å ha sagt det med en gang; noen velger å benytte automatisert (hel eller delvis) datafangst i sin tapsanalyse. Dette kan gi ganske nøyaktig tapstall for linjen. Faren er derimot at operatørene, som skal jobbe med forbedringene av tapene på sin linje, blir fremmedgjort overfor de problemene som eksisterer på deres linje.
Halvautomatisk datafangst
Operatørene får dermed ikke så stort eierskap til sine egne problemer, og forbedringstakten har en tendens til å gå ned. Det finnes mange eksempler rundt om i verden på bedrifter som har kastet ut sitt automatiserte datafangstsystem, og gått tilbake til registrering fra operatørene.

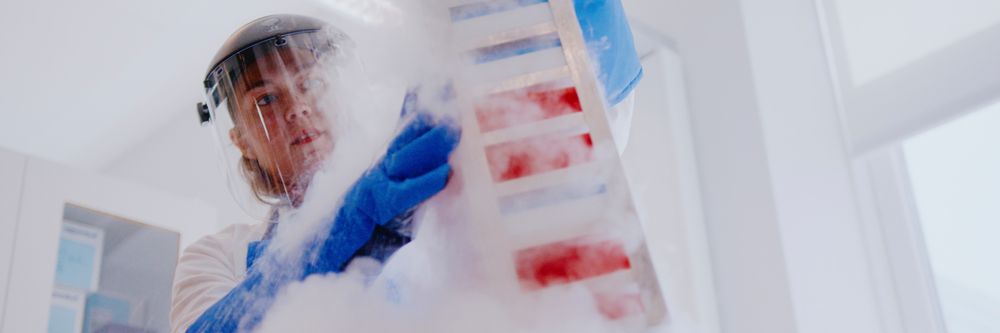
Når det er sagt, kan en kombinasjon av automatisk datafangst og operatørregistrering være veien å gå. Automatikken kan for eksempel logge start/stopptidspunkter, telle antall produserte enheter osv., mens operatørene registrerer stoppårsaker. Nedtrekksmenyer i et skjermbasert system eller scanning av strekkoder kan være en effektiv metode for operatørdatafangst.
Kategoriser tapene
Tidstapene, i OEE, deles gjerne opp i kategorier. Det blir lettere å gi ansvar i organisasjonen, på de ulike tapene, samt velge riktig forbedringsverktøy for de ulike oppgavene. Typiske tapskategorier i OEE er:
- Havari
- Omstilling/produktbytte (SMED)
- Oppstart/nedkjøring av linjen (se SMED)
- Småstopp
- Hastighetstap (linjen kjøres med lavere fart enn den er kjøpt inn/designet for)
- Vrak, eller kvalitetsforringelse som krever ekstraarbeid
I tillegg til effektivitetstap, finnes også andre typiske svinn i produksjonen. Disse kan være sløsing med materialer (svinn), kostnader til energi, kostnader til vedlikehold og deler.
Perfeksjoner prioritering
For å kunne sammenlikne alle tapene, i kroner og øre, må tidstapet (fra tapt OEE) beregnes om i kroner. Dette gjøres enkelt ved å multiplisere timene tapt med produksjonskostnaden per time for linjen. For arbeidsintensiv industri, blir fort produksjonskostnaden per time 450 – 600 NOK/time per operatør på linjen, inkludert indirekte kostnader. I kapitalintensiv industri blir raskt timekostnaden 10 000 NOK.
Når tapene kartlegges på denne måten, er det enkelt å prioritere hvilke forbedringsprosjekter som skal ha fokus. Det blir også vesentlig lettere å vise konkrete resultater, i kroner og øre, av gjennomførte forbedringer og investeringer.
Det bør lages et oppsett for hver enkelt produksjonslinje, slik at både operatører og ledere har samme oppfatning av hvor det tapes penger, og hva det må jobbes med for å bli bedre. Forbedringsgruppene i TPM må så styres mot å jobbe med de største tapene som de kan påvirke/forbedre.
Aktiv målstyring
En god tapsanalyse gir ledelsen et godt verktøy for å prioritere forbedringsprosjekter. Samtidig hjelper den alle i organisasjonen å ha fokus på de elementene der det tapes mest penger, slik at alle jobber mer strukturert med det som gir de beste resultatene for bedriften.
Denne styrte forbedringstakten kan forbedres ytterligere ved å målstyre de viktigste tapene på hver linje. En god tapsanalyse gir også større mulighet til å følge opp at forbedringsprosjekter og investeringer gir tilstrekkelige resultater.
Tapsanalysen gir dermed mulighet til å tallfeste, i kroner og øre, forbedringsaktivitetene i produksjonen. Forbedringsaktivitetene kan dermed sammenliknes med andre kostnadsforbedringer ellers i bedriften, f.eks. innkjøp.
Les også de andre artiklene i "Perfekt produksjon!":
Del 2: Forbedringsgrupper dobler produktiviteten
Del 5: Pitstopp produktbytte med SMED
Del 7: Operatørvedlikehold: Selvgjort er velgjort