Det reduserer reduserer småstopp og øker effektiviteten (OEE).
Vedlikeholdsproblemer
Nedetid går for å være effektivitetens værste fiende. Hvorfor havarerer maskinene, og hvorfor er vi plaget med småstopp? Er utstyret utslitt, feildesignet, eller kanskje dårlig vedlikeholdt? Det er gjort mange undersøkelser for å kartlegge årsakene til problemene. Men, tallene det vanligvis refereres til, skriver seg fra bilprodusenten Nissan.

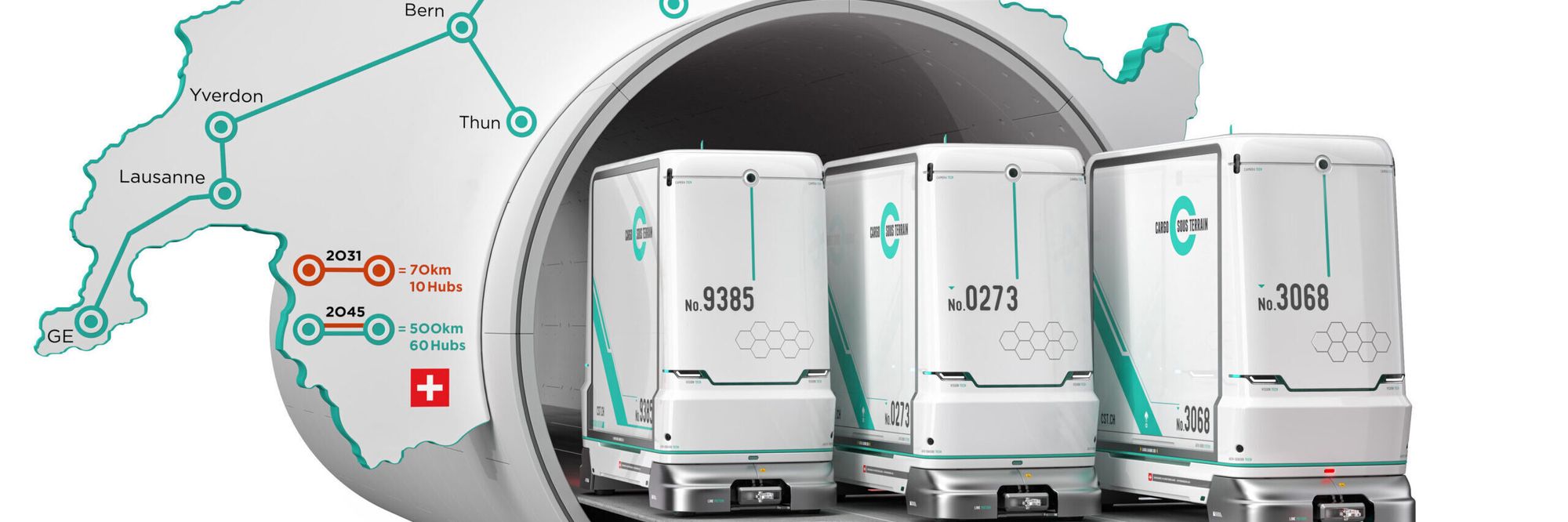
Feil betjening utgjør nesten annenhver stopp eller havari. Den nest største synderen, med hver tredje stopp/havari, kan tilskrives vedlikeholdsrelaterte årsaker. Selv om verken varighet eller kostnader er kjent, er det for mange et stort forbedringspotensial når gjennomsnittlig 9 av 10 hendelser er relatert til betjening eller vedlikehold.
Reddende engel
Og det er her operatørvedlikehold kan komme inn, nesten som en reddende engel. For det er ingen som kjenner produksjonsutstyret like godt som operatørene.
Operatørvedlikehold er en systematisk tilnærming for å gripe fatt i de viktigste stoppårsakene for en maskin/linje, hovedsaklig:
- maskinen blir betjent feil
- det mangler smøring
- det er bolter/mutrer som er løse
- vi er plaget med støv eller vanninntrengning i maskinen
Operatørenes vedlikehold deles gjerne inn i 8 trinn, eller fra trinn 0 til 7. Se eget avsnitt, "Fire forbedringstrinn", i separat sak på høyre side, for detaljer om de fire første trinnene.
5S og forbedringsgrupper først
Før det i det hele tatt vurderes å begynne med operatørvedlikehold, må 5S være gjennomført som en innarbeidet arbeidsform. Dette skyldes at 5S danner basisen for det arbeidet som skal gjøres i operatørvedlikeholdet. Gjennom 5S oppnås en god standard for orden og systematikk i områdene rundt maskinen/linjen. Samtidig er ansvarsområder mellom operatørene fordelt. I operatør-vedlikeholdet går vi videre til å fokusere på maskinen/linjen. Standarden skal heves, ved å gi operatørene ytterligere oppgaver og ansvar for produksjonsutstyret.
Gjennom 5S har vi også fått godt fungerende forbedringsgrupper. Disse gruppene har lært seg å jobbe selvstendig med forbedringer, og har lært å dokumentere og styre arbeidet sitt med hjelp av tiltaksliste. I operatørvedlikeholdet vil forbedringsgruppen bli utfordret til mer krevende oppgaver. En godt fungerende forbedringsgruppe er derfor vitalt for å få til en god prosess med operatørvedlikehold.
Ansvar og avdeling
Det er viktig å presisere at det er den enkelte leder som er ansvarlig for hvordan avdelingen arbeider og resultat som oppnås. Dette inkluderer operatørvedlikeholdet. Det må derfor aldri være noen tvil om at det er linjeledelsen som er ansvarlig for resultat og gjennomføringen av hele TPM og operatørvedlikehold.
Vedlikeholdsavdelingen er limet i operatørvedlikeholdet. Denne avdelingen skal gi operatørene nødvendig opplæring innenfor operatørvedlikehold. Det er også de som skal beskrive hvilket forebyggende vedlikehold som kan tas av operatør.
Sammen med operatøren, skal teknisk/vedlikeholdsavdeling lage instruksjoner for hvilken rengjøring, smøring og inspeksjon som skal foretas, og når og hvordan. Operatørvedlikeholdet har fokus på hva operatøren selv kan gjøre, men erfaringsmessig blir det fortsatt ”nok” oppgaver igjen for vedlikeholdsavdelingen. I oppstarten, av operatørvedlikeholdet, må det derfor beregnes en økt belastning på vedlikeholdsavdelingen.
Rå resultater
Dersom tapsanalysen avdekker at småstopp og havarier utgjør de største tapene i kroner og øre, er operatørvedlikehold høyst aktuelt. Men det er sjelden snarveier. Som nevnt ovenfor, må 5S og forbedringsgrupper være på plass. Dessuten tar selve prosessen med operatørvedlikehold tid før resultatene kommer.

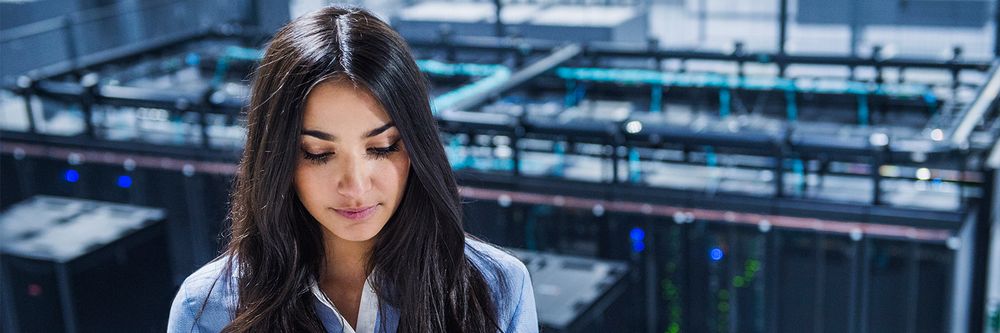
Start gjerne med et begrenset område, for eksempel en maskin eller en del av en produksjonslinje. Med tilstrekkelige ressurser, vil det typisk ta 6 – 12 måneder å klare de fire første trinnene (0 – 3).
Det er også viktig å presisere at det i utgangspunktet ikke skal være operatørvedlikehold på alle maskiner/linjer. Det er først og fremst flaskehalsene i produksjonen som skal under lupen (eller smørekannen, fastnøkler etc.).
Og det blir lønn for strevet. Effektiviteten vil øke. Det er ikke uvanlig at OEE øker inntil 10 prosent for hvert trinn med operatørvedlikehold som innføres!
Forebyggende vedlikehold
TPM ble tidligere ofte betegnet som Total Preventive Maintenance. Vedlikehold var i fokus. Konseptet ble utviklet av JIPM (Japanese Institute of Plant Maintenance) i 1971, basert på et amerikansk program, ”Preventive Maintenance”, som kom til Japan på 1950- og 60-tallet. Nippondenso Company, et selskap i Toyota-gruppen, var den første som tok det i bruk.
I dag benyttes uttrykket TPM i stor grad om Total Productive Management, eller en bedrifts produksjonssystem. Forbedringsprogram benyttes over hele verden, i alle industrigrener.
Les også de andre artiklene i "Perfekt produksjon!":
Del 2: Forbedringsgrupper dobler produktiviteten
Del 5: Pitstopp produktbytte med SMED
Del 6: Tapsanalyse setter en pris på tapene