Tekst: Petter Bjerkeli, Novotek
Sting skrev sangen ”History Will Teach Us Nothing” (album: …Nothing Like the Sun) på 1980-tallet. Tittelen var ironisk.
Og basert på historielærens svar på artistens spørsmål om hva elevene skulle lære av historien. For det er selvsagt mye å lære av både konvensjonell historie og historiske data, samplet i produksjonsprosesser.
Definer målet
Vi illustrerer sistnevnte i en stegvis tilnærming. Definer målet i startgropen. Hva skal vi ha ut av dette? Det er like mange svar som produksjonsprosesser, men vi jobber oss kjapt gjennom noen eksempler under.
Optimal produktkvalitet
Produktkvaliteten kan av og til være ujevn. Kanskje sammenhenger i historikkdata kan avdekke hvorfor? Og i så fall er det kanskje mulig å utvikle en løsning som hjelper operatørene med å ta bedre beslutninger? En sammenligning av kvaliteten, før og etter en tenkt løsning, gir en pekepinn på hva som kan spares.
Prediksjon av prosessparametre
Visse prosessparametre analyseres gjerne på lab. Dette kan gi forsinket justering av prosessen. Kanskje historikkdata kan gjøre susen? Ved å utvikle en løsning, basert på produksjonshistorien, kan operatørene få kontinuerlig informasjon om tuning av aktuelle prosessparametre.

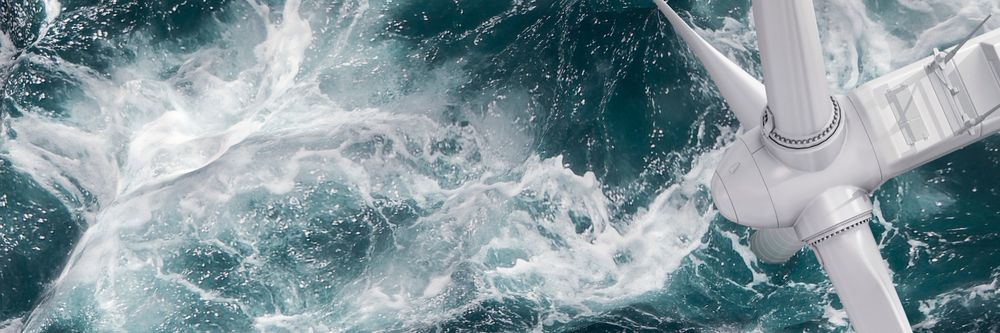
Golden batch
Noen produksjons-batcher blir bra, og andre ikke. Hvorfor? Kan vi finne svaret i historikkdata og kan vi gjøre noe med det i det hele tatt? Ikke usannsynlig!
Optimalt skiftlag
Skiftlag kjører prosesser forskjellig. Er en metode å foretrekke? Kan vi utvikle en løsning som gjør det lettere for alle å produsere på samme måte?
Optimal prosess
Komplekse, multivariat-prosesser kan ha mange motstridige kvalitetsparametre. Kan vi utvikle og teste en ny styring som tar hensyn til alle data, og foreslår settpunkter slik at prosessen optimeres?
Vedlikehold av maskiner
Det utføres periodisk vedlikehold på maskiner. Noen ganger føles det kanskje bortkastet, fordi det enten er unødvendig, eller at maskinene uansett går i stykker, mellom serviceintervallene. Kanskje prosessdata kan benyttes i en løsning som indikerer når det virkelig er behov for service? Eventuelt sammen med tilstandsbasert overvåking av maskiner og utstyr.
Finn datagrunnlaget
Historiske prosessdata lagres ofte på ulike steder, Eksempler er industrielle, tidsserie prosessdatabaser, relasjonsdatabaser, vedlikeholdssystemer, laboratoriesystemer, tekstfiler etc. Når historikkdata skal benyttes, for analyse og prosessforbedringer, er verktøy som kombinerer informasjon fra flere kilder og samplingsintervall vitalt. Det er også essensielt å kontrollere at kun relevante data er med. Å filtrere vekk produksjonsstopp og annen råtten informasjon kan være nødvendig.
Analyser!
Å manuelt finne sammenhengen, mellom data, ved å legge opp noen trendkurver, kan funke, men er ikke alltid den beste metoden. Det kan være lett å bli lurt opp i stry ved å se på en tidsbegrenset periode, og kanskje trekke feil konklusjon.
Med moderne verktøy, for prosessanalyse, kan oppgaven være en smal sak. Det holder å fortelle systemet hvilken datamengde som skal undersøkes, og hva det skal lete etter. Systemet gjør resten. Etter analysen rapporterer systemet hvilke sammenhenger som har blitt funnet, og hvor store de er.
I praksis bygger analysen opp en modell som beskriver prosessen. Et slikt verktøy dekker typisk forskjellige analysemetoder og ulike produksjonsprosesser, for eksempel kontinuerlige prosesser og batch.
Kombiner kunnskap
Med masse ny prosesskunnskap, er det bare å evaluere avkastningen på oppgradering av automatiseringsløsningene, eller annet utstyr for den saks skyld. Det er også smart å kombinere ”gammel” prosessinformasjon med eksisterende erfaringer og ekspertkunnskap. Det er selvsagt nødvendig å involvere de som skal benytte eventuelle nye løsninger, inklusiv operatørene.
Velg å implementere løsningen i en stabil og velprøvd plattform. Det er enkelt å overføre analyseresultat, få oversikt over hva som skjer, og den lett kan forstås av mange. Altfor mange gode automatiseringsløsninger implementeres i et unødvendig komplekst miljø.
Simuler!
Hvordan forsikre seg om at den nye løsningen vil fungere som tenkt? Her kommer historikkdata igjen til nytte. Simulering gjør susen, istedenfor å koble seg direkte til prosessen. Benytt en plattform som gjør det mulig, og enkelt, å skifte mellom historiske- og sanntids prosessdata.
Implementer og dokumenter
Dokumenter nå resultatet. Det beste er selvfølgelig å dokumentere både før og etter. Hvor stor ble forbedringen? Hva innebar det i sparte kroner? Det blir lettere å få bevilgninger til neste prosjekt på denne måten.
Online prosessjustering
Noen systemer utnytter de matematiske modellene, som har blitt skapt i analysen, og gjør det mulig å implementere en mer online løsning. Dette karakteriseres av at systemet kontinuerlig overvåker og styrer prosessen. Resultatet er en ”intelligent” styring som kan korrigere prosessen, før det oppstår problemer. Et eksempel er Proficy Cause+ fra GE Fanuc Intelligent Platforms.