Fokuset er på bruk av automatiske IT-løsninger. De nødvendige endringsprosessene dekkes i mindre grad. Første del dekker beregning, bruk og forberedelser av OEE, samt automatisk datafangst av hendelser i styringssystemene.
Identifiserer alle tap
Overall Equipment Effectiveness, forkortet OEE, er måling av den totale effektiviteten til en maskin, produksjonslinje, anlegg eller selskap. Målemetoden baseres på å identifisere alle ”tap”, som deles i tre hovedkategorier:
- Tilgjengelighet (andel av teoretisk planlagt tid for utstyret)
- Ytelse (andel av teoretisk, maksimal produksjonskapasitet eller syklustid/takttid)
- Kvalitet (andel godkjente produkter/produksjon)
Implementering av OEE kan ikke sammenlignes med å løse en mattematisk oppgave, men er mer som å skrive en stil. Det bør lages en disposisjon, og selve innholdet blir selvsagt individuelt. Ettersom det ikke finnes et ”fasitsvar” for OEE, dekker vår ”ABC” hovedprosessene og oppgavene som er aktuelle å vurdere i forbindelse med implementering og bruk av konseptet.
Slik beregnes OEE
Hovedkategoriene (se ovenfor) beregnes i prosent, og OEE er produktet av disse tre. OEE vil derfor alltid være mellom 0 og 100 (prosent).
Et lite regneeksempel: en maskin har tilgjengelighet på 70 prosent (0,7), ytelsen ligger også på 70 prosent (0,7), mens kvaliteten ligger på 98 prosent (0,98). Produktet blir 0,48, eller OEE på 48 prosent.
Bruk av OEE
Mange fokuserer naturlig nok på selve OEE-tallet. Men vi har sett flere eksempler fra norsk næringsliv som oppnår gode resultater uten å legge stor vekt på selve måletallet. Innholdet i målingene, både sanntids (online) og historisk, benyttes primært som verktøy og hjelpemiddel for operatører, vedlikeholdspersonell og andre som har nytte av lett tilgjengelig og detaljert informasjon om både produksjonen og produksjonsutstyret.

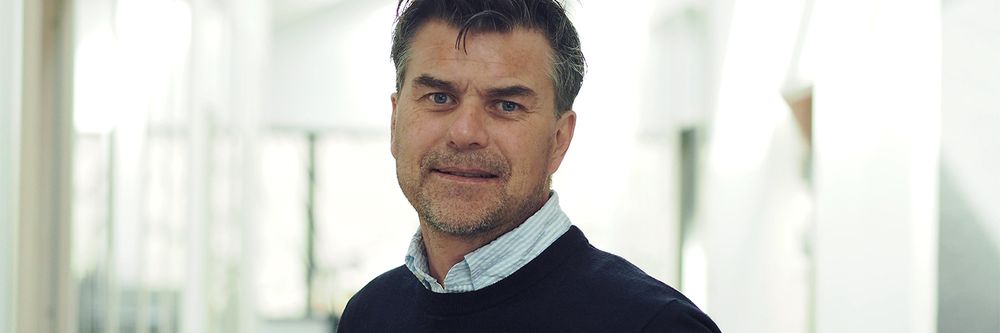
Det ligger normalt store mengder detaljer bak OEE-tallene, som med fordel kan analyseres og korreleres på utallige måter. Bare behov og fantasi er begrensende faktorer.
Flust med formål
OEE kan med fordel benyttes til helt andre formål, med svært gode resultater. Eksempler på dette er:
- Dokumentasjon/kalkulasjoner for å evaluere om nytt utstyr, for eksempel en ny maskin, virkelig er nødvendig. Dersom OEE er lavt, kan en vesentlig mindre investering kanskje redusere de største ”tapene” (tilgjengelighet, ytelse og/eller kvalitet) slik at en ny maskin er unødvendig.
- Rettferdiggjøre investeringer i nytt utstyr. Dersom en produksjonslinje har identifiserte flaskehalser som utgjør store OEE-tap, kan en estimert økt OEE benyttes som dokumentasjon for nødvendige investeringer.
- Kontraktsfesting av ytelser og kapasiteter for maskiner og utstyr som kjøpes inn. Dette kan for eksempel gjelde betalingsbetingelser som er koplet til et visst OEE-tall i forbindelse med igangkjøring eller driftsgarantier (en viss OEE over gitte perioder).
- Overvåking av utstyrets effektivitet gjennom hele livssyklusen. Dersom en stabil og høy OEE går ned eller begynner å svinge, indikerer dette behov for ekstra vedlikehold eller ettersyn.
- OEE-målinger og motivasjon av operatører til å prioritere forbedringer i utstyret gir økt eierskap som igjen normalt vil gi økt effektivitet.
- Automatisk datafangst, rapportering og overføring av produksjonsdata til andre IT-systemer reduserer ”papirarbeid” (les: kostnader), øker kvaliteten (statistisk sett er et par prosent av alle punchinger feil) og fører til raskere og potensielt bedre beslutningsstøtte.
- Operatørmotivasjon og økt eierskap til produksjonsutstyret.
Også for prosessindustri
Målemetoden har sitt opphav i Japan på 1960-tallet, men det tok rundt 20 år før den kom til Vesten. OEE er spesielt populært innen stykkproduksjon (industriproduksjon, trykkerier etc.), men er like relevant for prosess og batch. I stedet for fullstendig produksjonsstopp, benyttes gjerne redusert produksjonshastighet (process slow-down). Uttrykket Overall Process Effectivesness, OPE, brukes ofte i prosessindustrien.
OEE benyttes gjerne som måletall i en større sammenheng, for eksempel ulike kontinuerlige forbedringskonsepter. Ett av disse kalles Total Productive Management (TPM), som også har sine røtter i Japen. For å komme opp i ”verdensklasse” (OEE på 85 prosent), er det normalt nødvendig med et konsept som TPM.
Informer og kartlegg
Selv om vår ABC for OEE har hovedfokus på teknologi, starter vi med litt organisasjonspsykologi. Å involvere alle som blir berørt av OEE-målinger, samt grundig planlegging, er essensielt for en vellykket implementering. Det er mange individuelle spørsmål som må adresseres og besvares i forkant, blant annet:
- Hvorfor gjør vi dette?
- Hvilke anlegg/produksjonslinjer/ maskiner skal måles?
- Hva vil vi oppnå?
- Hvem berøres, og på hvilken måte?
- Hvordan skal det gjøres?
- Hvordan skal informasjonen brukes?
- Hvordan distribueres informasjonen (til andre enn primærbrukerne)?
Kartlegging av både brukernes behov og eksisterende utstyr og systemer er et annet viktig element som bør gjøres tidlig i prosessen. Dette kan inkludere tverrfaglige intervju av produksjonsarbeidere, operatører og ledelse innen for eksempel vedlikehold, produksjon, drift, IT, økonomi og administrasjon. Og hva med styret?
Registrere produksjonshendelser
Hvordan skal informasjon om for eksempel type produkter, antall produserte enheter, stopp- og vrakårsaker registreres? Her kan det velges mellom to hovedtilnærminger:
- Manuell registrering av operatører, ved hjelp av for eksempel nedtrekksmenyer i et lokalt operatørpanel/skjerm eller scanning av strekkoder for de ulike årsakene. Selv om det legges opp til størst mulig grad av automatisk datafangst (se under), er det vitalt å kunne legge inn stopp/vrakårsaker manuelt. Dette gjelder for eksempel stopper utløst av stoppknapp/nødstopp. Det blir raskt ønskelig å finne ut hvorfor den høye ”søylen” i stoppårsaksrapportene (som viser stoppknappen) egentlig er trykket inn. Dette skyldes ofte utenforliggende årsaker, noe manuell tasting må derfor gjøres.
- Automatisk datafangst fra styringer av maskiner og produksjonslinjer. I praksis er en kombinasjon med manuell registrering (punktet ovenfor) trolig nødvendig i de fleste tilfeller, spesielt registrering av manuell stopp/nødstopp.
Stor grad av automatisk datafangst fra produksjonssystemene kan redusere driftskostnadene for OEE-målingene, samt øke kvaliteten og detaljgraden på informasjonen. Det er to hovedretninger å følge for slik automatisering:
- Benytte eksisterende styringssystemer for maskiner og produksjonslinjer. Selv om de fleste styringer, enten det dreier seg om CNC, PLS eller prosesskontrollsystem (se ordliste i grå boks til høyre), er fleksible og programmerbare eller konfigurerbare, reiser tilnærmingen spørsmål som må kartlegges og vurderes, blant annet: kan utstyret kommunisere? Er det nettverkt til alle aktuelle maskiner og produksjonslinjer? Hvilken informasjon, om for eksempel stoppårsaker, kan overføres? Hva kreves for å endre styringene? Er det nødvendig med ekstra sensorer eller lignende? Hvilke konsekvenser vil endringer i styringene ha? Påvirkes eventuelle garantier? Se også egen sak om dette.
- Etablere et frittstående datafangstsystem med relevante sensorer, moduler for innsamling fra disse, og kommunikasjon til et systemet som utfører OEE-målingene.
Både sanntids- og historisk OEE-informasjon, og bakgrunnsdetaljer, bør være tilgjengelig for alle som kan ha nytte av det, fra produksjonsmiljøet til styrerommet. Administrative brukere bør ha informasjonen tilgjengelig via sine vanlige PC-er. I produksjonen bør det være operatørterminaler tilgjengelig på alle ”naturlige” steder. Det er viktig å velge utstyr som er designet for det aktuelle industrimiljøet, både med tanke på betjening (tastatur, trykknapper, touch-skjerm etc.) og selve miljøet, støv, fuktighet, vibrasjoner, temperatur og elektromagnetisk stråling.
Automatisk datafangst?
Automatisk datafangst av antall produserte enheter og stopp/vrakårsaker kan for eksempel gjøres ved å modifisere eksisterende styringer i maskiner og produksjonslinjer. Dette er noen av oppgavene som må gjøres ved en slik tilnærming:
- ”Gratis” innganger/utganger i styringene? Undersøk på et tidlig tidspunkt om hvilke innganger og utganger som kan hentes nesten "gratis" i PLS-en. Dette kan hjelpe til med å komme raskt i gang med å hente ut de viktigste signalene som stopp, nødstopp, i drift, venter, tellere, takt/syklustider etc.
- Det bør på et tidlig tidspunkt lages en felles "datainnsamlingsblokk” (modul) i PLS-ene. Modulen bør være lik for alle maskinene. En slik fellesstruktur sparer svært mange timers programmering.
- Må det legges til ekstra sensorer og maskinvare i styringene (PLS) for å håndtere datafangsten?
- Programmene i styringene (PLS) må utvides til å håndtere relevant informasjon til OEE-systemet (mye kan håndteres i de to første punktene ovenfor).
- Hvordan kvalitetssikre at automatisk registrering av årsaken stemmer? Det kan være en følgefeil. Hvor kritisk er dette for hele totalløsningen?
- Hvordan kan styringene kommunisere? Finnes nettverk? Hvis ikke, hva skal velges? Skal det benyttes såkalte feltbusser (eks. Can, DeviceNet, Fieldbus Foundation, Interbus, Profibus) eller (industrielt) Ethernet? Det finnes flere ulike kommunikasjonsprotokoller for industrielt Ethernet, pass på at alt utstyret kommuniserer. Utstyr med ulikt ”språk” kan for eksempel integreres med protokollkonvertere (gatewayer), gjerne en ”black box”, eller ved hjelp av PC-basert OPC (Openness Productivity Communication) software. Bedriftens automatiseringsavdeling og maskinleverandører er normalt en god informasjonskilde.
- Dersom det ikke finnes infrastruktur for nettverk, skal det benyttes tradisjonell kobberkabel, fiberoptikk, eller trådløs kommunikasjon? Sistnevnte kan redusere installasjonskostnadene, men kan være sårbare og upålitelige i visse produksjonsmiljøer. Selv om anskaffelseskostnadene er høyere for industrielt kommunikasjonsutstyr, kan økt pålitelighet og potensielt lavere livssykelkostnader ofte rettferdiggjøre dette.