Til høsten skal det første 787 Dreamliner-passasjerflyet fra Boeing leveres til lanseringskunden ANA.
Svaret fra erkekonkurrenten Airbus heter A350 XWB og skal være drøyt tre år unna flyplassene.

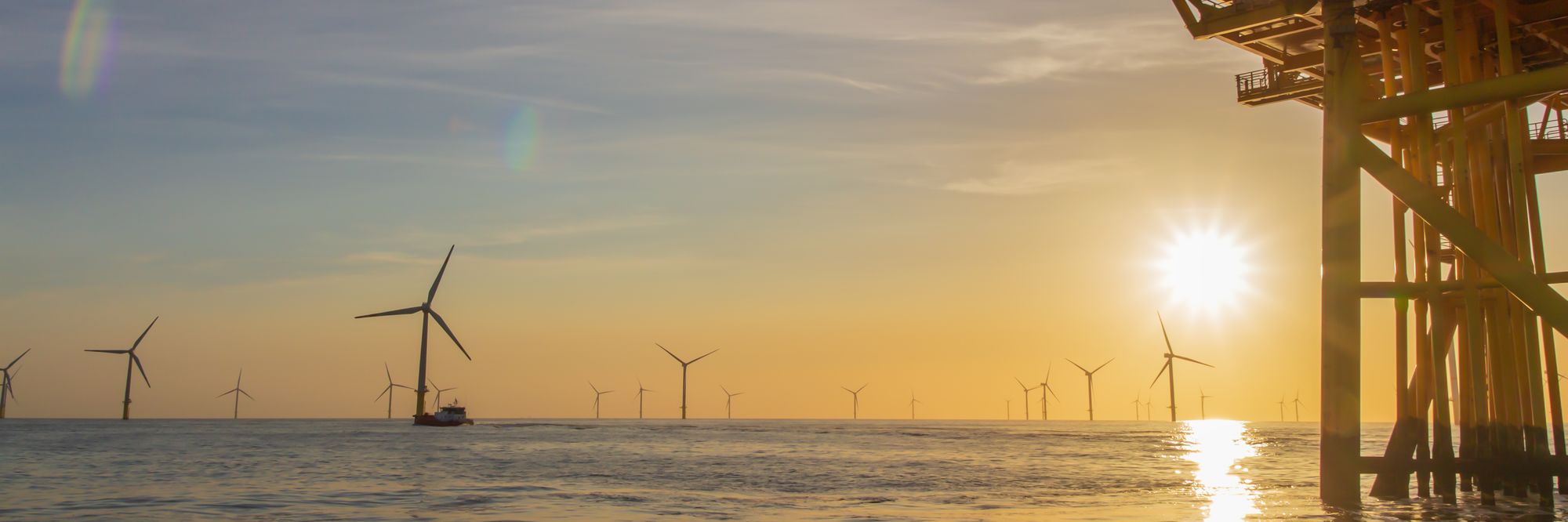
De tomotors langdistanse-bredbuksflyene ligner hverandre på flere måter. Ikke minst i materialbruken. B787 blir det første kommersielle flyet der halvparten av vekten består av komposittmaterialer. A350 vil ha enda mindre metall om bord.
Les også: Plastfly skal gi luftherredømme
Vekt/styrke-forhold
Pådriveren for flyprodusentenes materialvalg er naturligvis effektivitet. Å fly flest og mest lengst mulig for hver dråpe hydrokarbon.
Lavere vekt gir bedre bæreevne, rekkevidde og drivstofforbruk som igjen gir lavere driftskostnader. Det er en åpenbar forutsetning at også motorene er effektive.
Målt i egenskaper delt på vekt, slår komposittmaterialer meget heldig ut.
Les også:
– Å handle fly er vårt beste klimatiltak
30 tonn
En A350-1000 vil være om lag 30 tonn lettere enn en B777-300 som har aluminiumsskrog. Airbus hevder at vekten per sete på en A350 reduseres med 14 prosent sammenlignet med B777, mens reduksjonen er 12 prosent for B787s del.
Så å si hele det ytre skroget er laget av karbonforsterket plast. Med visse unntak må du inn i den indre strukturen på flyene for å finne tradisjonelle materialer som stål og aluminiumlegeringer. På motorfestene og understellet er det titan som dominerer.
Komposittmaterialene er ikke utsatt for spenningskorrosjon, et problem for tradisjonell flyaluminium. Selv om en høyere E-modul (stivhet) gir lavere tøyninger lokalt og gode utmattingsegenskaper, er problematikken med sprekkdannelser langt fra eliminert med plastmaterialene heller.
Sprøtt
Riktig design og fiberplassering er viktig for å unngå skader som delaminering og oppsprekking. Liming og sammenføyning er også sentrale temaer for å sikre suksessfull innføring av kompositter i så store andeler av flystrukturen. Spesielle hensyn må tas til å forebygge skader fra for eksempel lyn og lignende.

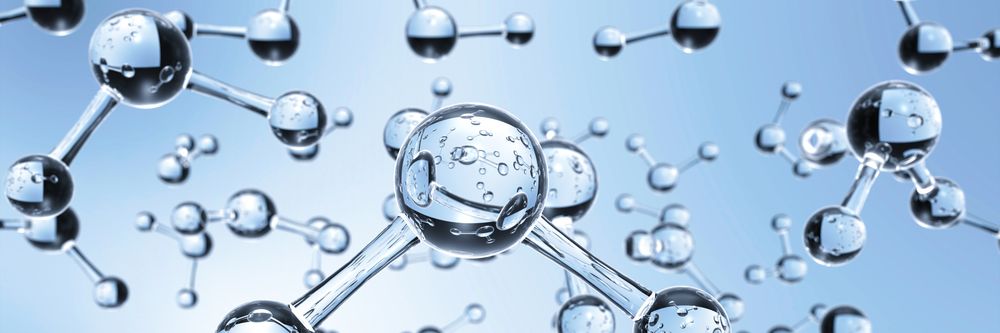
Når det gjelder lavtemperaturegenskaper, har aluminium, og ikke minst aluminium-litium, hatt de beste kortene på hånda. Jo lavere temperatur, jo større styrke og duktilitet, altså formgivningsevne.
Disse metallene har bedre egenskaper i minus 60 grader i lufta enn de har på bakken i pluss 20.
På polymermaterialene har en av utfordringene vært at egenskapene er motsatt. De fleste polymerer blir litt sprøere i kulde.
80 prosent i volum
Mens 787 består av 50 prosent komposittmateriale i flyets vekt, utgjør disse materialene cirka 80 prosent av flyets volum.
Forrige lanserte Boeing-fly, 777 i 1994, har om lag ni prosent av vekten sin i komposittmaterialer.
Airbusene har utviklet seg som følger: A300 (i lufta siden 1974) har i underkant av to prosent komposittmaterialer. Forrige nylansering, superjumboen A380 som fløy første gang i 2005, har cirka 25 prosent kompositter.
A350-900 vil bestå av 62,5 tonn karbonfiberforsterket plast (53 prosent av tomvekten som produsenten oppgir til 118 tonn). I Dreamliners grunnversjon, 787-8, utgjør komposittmaterialer ganske nøyaktig halvparten av tomvekten på 110 tonn, altså 55 tonn.
Små forskjeller - stor effekt
Den økte styrken i skroget har også sine mer trivielle fordeler for oss som sitter på. Komposittene tillater større vinduer. På Boeing 787 måler vinduene cirka 27 x 47 centimeter, sammenlignet med 27 x 39 cm på forgjengeren 767.
Forskjellen kan høres liten ut, men effekten er stor. Den ekstra høyden på vinduene stikker over stolryggene og gir utsikt på begge sider av kabinen uansett hvor du sitter i Norwegian-flyet (for eksempel).
BILDESERIE: Her bygges Boeing-flyene
Mye titan
Et annet trekk ved materialene på disse to flymaskinene, er den utstrakte bruken av titan. Det sterke, lette, og kostbare, metallet benyttes i for eksempel motorfestene på vingene, i landingsstellet, i dørrammene og i viftebladene på RR Trent-motorene på B787. Til sammen 16 tonn per fly.
Sett med norske øyne er dette interessant. Ett selskap er Norsk Titanium, hvis forretningsidé er å lage komponenter i titan basert på sveising (PTA). I fjor fikk de en avtale med Airbus-morselskapet EADS som skal bistå med å godkjenne teknologien for titankomponentproduksjon for fly- og forsvarsindustrien.
I den andre enden av verdikjeden befinner gruveselskapet Nordic Mining seg. De planlegger å utvinne titan fra rutil på Engebø i Sunnfjord.
Les også:
Airbus kan få norske titankomponenter
Forskjellige skrogdesign
Det er mange års forskning og utvikling som gjør at flyprodusentene nå føler seg fortrolige nok med hvordan komposittmaterialene oppfører seg og at prisen har sunket. De har skaffet seg erfaring på design, fabrikasjon og bruk.
Selv om både A350 og B787 har komposittskrog, er byggemåten ganskje forskjellig. På B787 er skroget satt sammen av tønneformede kompositter i ett stykke. På A350 er de tre skrogseksjonene igjen delt inn i fire paneler som monteres sammen.
Les også:
Forsinket
Sluttmonteringen av 787 skjer på Boeings fabrikkfasiliteter i Everett utenfor Seattle.
Nå er dessuten noe av komponentproduksjonen hentet hjem etter at svakheter i de japanske komposittdelene, i strukturen som forbinder skroget og vingene (wingbox), som ble oppdaget for et par år siden og som førte til store forsinkelser.
Boeing: 737-erstatter innen 2020
Frykter nye Dreamliner-forsinkelser
Boeing setter Dreamlinerne på bakken
Det er ingen tvil om at Airbus har fulgt nøye med på pionérarbeidet til Boeing og prøver å lære av amerikanernes feil.
Når det gjelder framstillingsmetoder, er den største enkeltkomponenten til A350 et imponerende eksempel. Dette 20 meter takpanelet til midtseksjonen er produsert i USA utenfor autoklav (uten trykkoker med en varmeovn med mulighet for å sette på trykk).
Norsk sprekkdeteksjon
Sprekkdannelser er den store stygge ulven i flyindustrien. Det har det vært siden verdens første passasjerjetfly, DH Comet, styrtet to ganger i 1954 med skrogkollaps etter tretthetsbrudd rundt vinduene som følge av trykkforandringer.
Ikke-destruktiv testing er en utfordring når det gjelder polymerbaserte komposittmaterialer. Materialenes sammensatte natur gjør at inspeksjon og tolkning av resultater blir mer komplisert enn for et tradisjonelt flymateriale som aluminium.
Kanskje blir kommende testteknologi norskutviklet? Iallfall har Nasjonalt senter for komposittkompetanse gående et forskningsprosjekt, blant annet i samarbeid med Nammo, Kongsberg, FFI og Ragasco for å bygge opp kompetanse på ikke-destruktiv testing (NDT) av avanserte komposittmaterialer.
Optonor i Trondheim har bygget et helt nytt utstyr for holografi og shearografi for prosjektpartnerne. Airbus benytter allerede lignende utstyr.
Kilder: Airbus, Boeing, Ragnar Sandmark, prosjektleder ved Nasjonalt senter for komposittkompetanse, Hans Jørgen Roven, professor ved institutt for materialteknologi, NTNU