–Norsk industri må få opp øynene for moderne dataverktøy. Vi opplever at industrien foreløpig ikke har god nok tro på modellbasert simulering. Det koster penger, og industrien ser ikke besparelsene, sier prosjektingeniør Olav A. Johnsen ved HTP.
Nå står simuleringsgruppen fram med sine erfaringer for å bidra til å skape større forståelse i industrien.
– Å gjøre endringer på et produksjonsanlegg etter at det er bygd, er svært kostbart. Ved å bygge en modell i tredimensjonal grafikk og simulere fabrikken i en datamaskin, kan du prøvekjøre og verifisere fabrikken allerede før du støper grunnmuren.

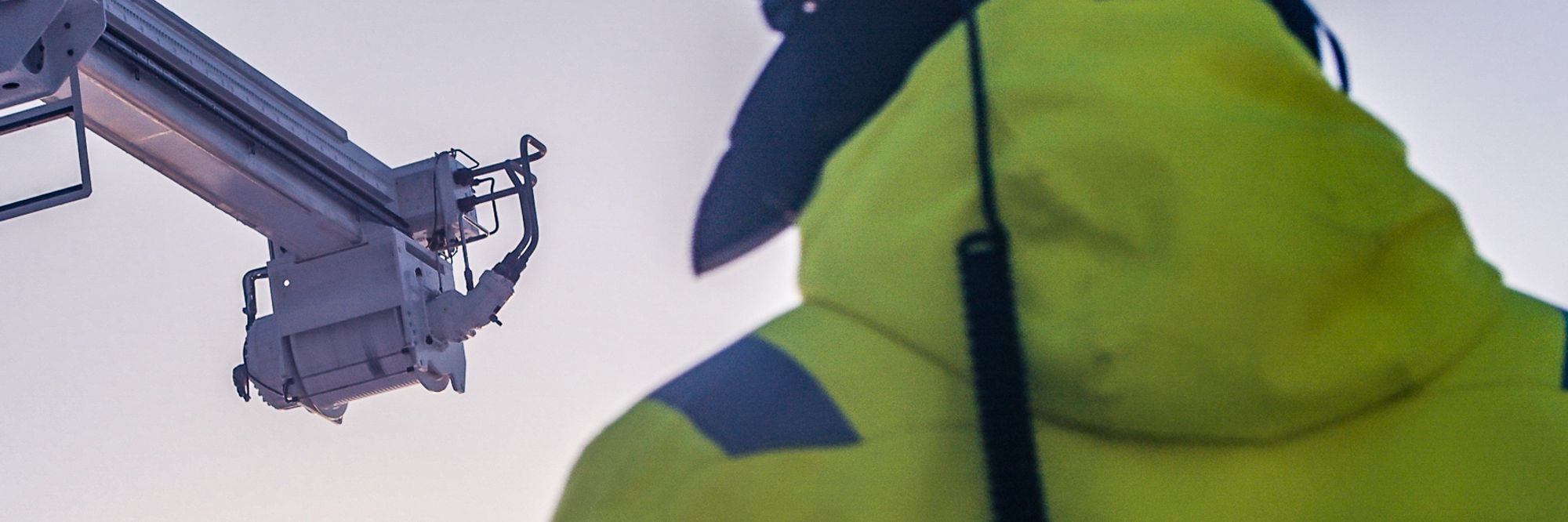
Skeptiske mellomledere
I USA bruker over 90 prosent av industriselskapene simuleringsverktøy, ifølge Johnsen. Også i Sverige er det langt mer vanlig enn i Norge.
Kostnaden med å gjennomføre et simuleringsoppdrag ligger mellom en prosent og tre prosent av de totale prosjektkostnadene. Hydro-gruppens erfaring er at bedriftenes toppledelse stort sett er positive, mens mellomlederne er mer kritiske. Prosjektene har ikke akkurat kommet rekende på en fjøl. Johnsen og hans kolleger har selv måttet selge simuleringsoppdragene inn i prosjektene.
– Kunder som har gitt oss oppdrag tidligere kommer tilbake. Det blir stadig lettere å få aksept for kostnadene. Hydro Aluminium Metal Products (Hamp) er blitt særlig ivrige etter å benytte modellbasert simulering, sier Johnsen.
Avslører feil
Med modellbasert simulering legges alt utstyr, operasjonstider, syklustider, ordrelister, nedetider og andre parametere i en produksjonsenhet inn i en simuleringsmodell. Testingen kan avsløre eventuelle flaskehalser, underkapasitet, eller om det er for mye utstyr. På eksisterende anlegg kan feil og mangler synliggjøres.
Johnsen og hans kolleger Arvid Skogseth, Christian Peder Braarud og Julien Desjardins var blant de første i Norge som tok i bruk verktøy for logistikksimulering; avdelingen ble etablert i 1997.
Mange besparelser
Noen tall på hvor store besparelser som kan oppnås med hjelp av modellbasert simulering, kan ikke gruppen gi.
– Det er vanskelig å tallfeste besparelsene. Prosjektets ledetid blir redusert – det gir utslag på bunnlinja. I noen tilfeller finner du ut at du kan redusere utstyrmengden, for eksempel en herdeovn eller en kran mindre. Det gir ikke bare innkjøpsbesparelser, men også reduserte driftskostnader. Du kan også se det som en forsikring på at anlegget vil fungere som det var tenkt, sier Braarud.
3-D simulering kan også brukes til å understøtte intern markedsføring av nye ideer ved å visualisere ideene, og til å skape bedre prosessoperatører; operatøren kan se hva som skjer om de gjør ulike inngrep, uten at den virkelige prosessen påvirkes. I aluminiumsindustrien kan simulering også brukes til å verifisere gassutslipp i elektrolysehallen.
Teknologiutvikling
– Simuleringssystemer kan visualisere tankesprang som du bare har vage begreper om, sier senioringeniør Sigmund Gjerven, som utvikler ny teknologi for aluminiumproduksjon ved Norsk Hydro.
Gjerven har nytte av verktøyet til å klargjøre hvordan framtidige anlegg vil fungere. Han bruker det også til å vise folk i organisasjonen som ikke er involvert i prosjektene hvordan tingene virker, og eliminerer dermed diskusjoner om hva som er mulig og umulig å få til.
– Problemstillingene er lettere å forstå når de fremstilles i virkelighetstro tredimensjonalt format.
Gode data nødvendig

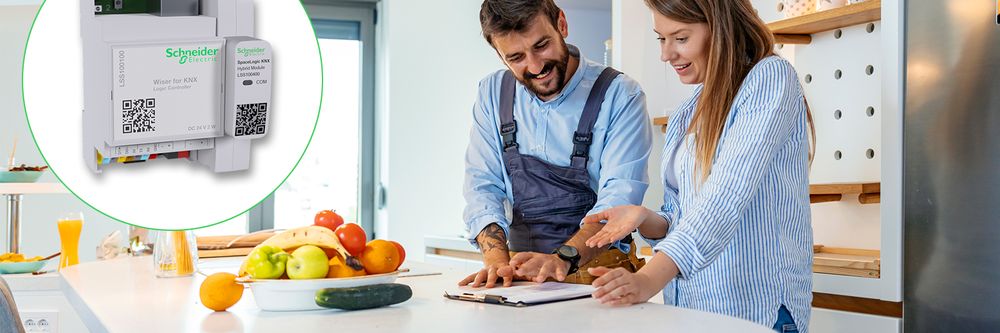
– Innsamling av data er uhyre viktig og en stor utfordring. Informasjonen som blir matet inn i modellen er kritisk for resultatet. I alle systemer er det en viss grad av slump. Når tilgjengelige data er utilstrekkelige, kan du komme fram til forslag som ligner på virkeligheten, sier Braarud.
Som regel er informasjonen spredd på mange forskjellige steder. I startfasen av et simuleringsprosjekt besøker representanter fra simuleringsgruppen fabrikken for å intervjue nøkkelpersonale; hele veien fra toppledelsen ned til arbeidere som jobber ute i produksjonsanleggene. På den måten samler de inn informasjon og skaffer seg et helhetlig bilde av fabrikken. Ting settes i system og mangler kan påpekes før simuleringen startes.
– Vi får et fugleperspektiv på hvordan ting henger sammen og avdekker årsaksforhold. Ofte får vi bedre oversikt enn noen av de som jobber på fabrikken, hevder Christian Peder Braarud.
De vanligste feilfaktorene i et simuleringsprosjekt er feil informasjon, feil bruk av distribusjoner, dårlig definerte objektsett og mangelfull deltakelse fra kunden –det vil si fabrikkens egne folk.
Amerikansk system
Hydro-gjengen bruker et simuleringsprogram som heter Automod fra det amerikanske selskapet Brooks Automation. Skandinavisk distributør for programmet er det svenske selskapet Xdin AB.
– Vi testet mange systemer, og valgte et som er fleksibelt og anvendelig for både store og små prosjekter med både enkle og komplekse modeller, som utvikles bra, og som brukes av de virkelig store produsentene i verden, sier Olav A. Johnsen.
Prisen på et slikt program er omlag 15.000 dollar for en startpakke, pluss 5000 dollar per modul som legges til. Neste mål for simuleringsgruppen er å koble simuleringssystemet til prosesstyresystemene og begynne med online-simulering i sanntid; emulering.