Mer penger mellom hendene øker lysten på ny båt.
Noen vil ha fart, mens andre setter komfort og sikkerhet i høysetet.
Familien foran
Hydrolift har stort sett konsentrert seg om den første kategorien, men nå satser Fredrikstadbedriften også på båter med familieverdier.
Ideen til den nye familiebåten dukket opp i august i fjor, og beslutningen om å bygge båten ble tatt. Så ble alle former og verktøy produsert, og nå er den satt i produksjon. Det er kanskje ny rekord for serieproduserte båter.
Nytt marked
– Vi ville lage en ny 27 fots båt beregnet på familier. Det innebar at vi designet en båt som var bredere og hadde mer plass enn de tradisjonelle båtene våre. Den skulle også ha en kabriolet som kunne brukes i alle hastigheter. Og en kabriolet er ikke en kalesje, understreker designer og Hydrolift-eier Bård Eker.
Båten har fått to lugarer, en stor for foreldre og en mindre for barn. Den bredere formen går litt ut over toppfarten, men Eker vil ikke ut med hva den er.

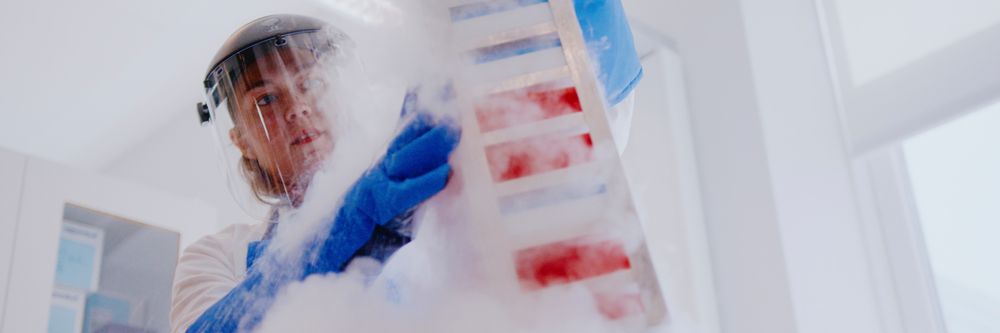
Karbon-alternativ
– Denne båten handler ikke om fart. Det har vi andre båter til, sier Eker, men de som vil betale, kan få den støpt i karbonfiber i stedet for glassfiber.
Det sparer 170 kilo og gjør hele skroget mye stivere.
– Vi har laget en båt med et nytt og moderne formspråk. Selv om den er fire fot kortere enn vår største modell, er den fem cm bredere. Vi har satt sikkerhet og kjøreegenskaper i høysetet, og kjøperne får kjørekurs med på kjøpet, sier Eker.
Raskt
– Det første vi startet med var en modell av båten i 1:10. Vi bygget den i polyuretan og brukte mye tid på å få alle mål og kurver så perfekte som mulig, sier Victor Rosenvinge som er sjefsingeniør i Bård Eker Industrial Design (BEID). Et annet av Ekers selskaper.
I september var alle fornøyd med modellen, og neste trinn var skanning. Modellen ble skannet i en tredimensjonal skanner som genererte en sky av koordinatpunkter. Denne punktskyen var utgangspunktet for det som skulle bli en tredimensjonal DAK-modell, men den kunne ikke puttes rett inn i programvaren. Til det var den altfor grov.
Punktskyer
– Vi trengte det vi kaller A-klasse flater for å kunne jobbe videre, og det laget vi ved å bearbeide punktskyen i et flatemodelleringsprogram. Vi brukte et som kalles Isemsurf og med det kunne vi bearbeide punktskyen til en kvalitet på flatene hvor det ikke er steg eller hull i overgangen mellom de ulike flatene, sier Rosenvinge.
Den flateoptimaliserte modellen var utgangspunktet for den videre bearbeidingen i DAK-programmet som i dette tilfellet er Catia v5 på PC.
- Her jobbet vi videre med flatene og kunne montere inn alle komponentene. På dette trinnet er arbeidsmåten den samme enten vi jobber med en ny båt, en bil, eller for den saks skyld en tøffel eller telefon. Stort sett får vi DAK-filer fra de ulike underleverandørene av komponenter. Hvis ikke, tegner vi dem inn selv. Alt skal inn i modellen, slik at vi kan gjøre alle mulige beregninger og tester på dette nivået. Vi bruker 3D-verktøyet så langt det er mulig før vi setter noe i produksjon.
Parallelt
Når 3D-modellen var klar, ble de ulike komponentene bygget som en såkalt plugg. Den består i at man freser ut en isoporkloss som så blir belagt med polyuretan. Det harde belegget blir så frest og finslipt til det er perfekt.
Denne positive formen er så utgangspunktet for selve pluggen som er den negative formen. Den blir støpt utenpå den positive og er det verktøyet hvor alle de nye båtkomponentene blir støpt.
For å rekke de knappe tidsfristene ble arbeidet konsentrert om skrogverktøyet og de store komponentene som inngår i den nye båten. Da de store komponentene var ferdig designet, gikk designerne løs på de mindre komponentene som ble fremstilt i selskapets egen tredimensjonale fres.
Virtuell trening
Når prosjektet utvikles så raskt som i dette tilfellet, må en rekke operasjoner gjøres samtidig. Til og med montørene får sitt første bekjentskap med den nye båten som en 3D-modell.
– Det betyr selvfølgelig ikke at de er fullt utlært når de første delene kommer, men det at de kan gjøre seg kjent med de ulike komponentene på skjermen, se hvordan de skal settes sammen og få besvart spørsmål, gjør overgangen til produksjon raskere og enklere. Dette viser hvordan 3D-modeller kan utnyttes langt mer enn i selve konstruksjonsfasen. I disse dager er det tre uker fra vi får de første delene til den første båten skal stå klar, sier Rosenvinge.
Til neste år
Selv om utviklingsprosjektet har gått fort, vil det ikke bli produsert mange båter i år. Hydrolift produserer bare på ordre, og det betyr at det neppe blir laget flere enn et titalls båter i år. Neste år legges det opp til en produksjon på mellom 35 og 50 av den nye familiebåten.