Olje- og gassindustrien er avhengig av å separere råvarer ved hjelp av destillasjon for å få ut råoljeprodukter som bensin, diesel og parafin og naturgassprodukter som metan, etan, propan osv.
I prosessindustrien brukes destillasjon til en rekke separasjonsoppgaver for kjemiske blandinger der man vil trekke ut enkelkomponenter eller grupper. Destillasjon er også brukt i farmasøyt- og næringsmiddelindustrien. På bilder fra raffinerier og prosessanlegg er det destillasjonstårnene som er de høyeste og mest synlige prosessenhetene.
Raskere til målet
I dag skjer separasjonen gjennom kolonner som er koblet i sekvenser – hver med sine kokere og kondensere. Hver kolonne produserer to produkter eller mellomprodukter.
Nå går utviklingen mot en ny type integrerte kolonner som gjør dem energisparende. To til tre tradisjonelle kolonner kan erstattes av en enkelt som har innvendige vertikale skillevegger. (Engelsk: ”Dividing Wall Column”.) Flere produkter kan separeres ved hjelp av færre kokere og kondensere, og med betydelig lavere totalt energiforbruk. Det er også mulig å koble om eksisterende kolonner for å oppnå tilsvarende gevinst uten å bygge om innmaten.
I dagens kolonner skjer det et tap når mellomproduktene går fra en kolonne til en annen: De separerte væskene blander seg litt igjen før prosessen fortsetter med å skille dem.
– Man kan sammenligne dette med en fjelltur der målet er en stor topp i horisonten. På veien må man passere en rekke småtopper med demotiverende dalsøkk før hver ny stigning. Den nye kolonnen representerer som en slags bru mellom toppene: man slipper å gå ned i dalene, forteller Ivar Halvorsen på SINTEF IKT.
I 2001 tok han doktorgrad på energieffektive kolonner – i tett samarbeid med miljøet rundt NTNU-professor Sigurd Skogestad. I etterkant har han jobbet med styring og andre utfordringer som den nye kolonneintegrasjonen fører med seg.
– Presis styring blir viktigere enn før på grunn av tettere integrasjon. En endring et sted i kolonnen, fører til at det må kompenseres et annet sted. Men med dagens teknologi er dette løsbart i praksis, sier han.
Flere fordeler
Halvorsen mener de nye kolonnene må sees på som ren miljøteknologi.

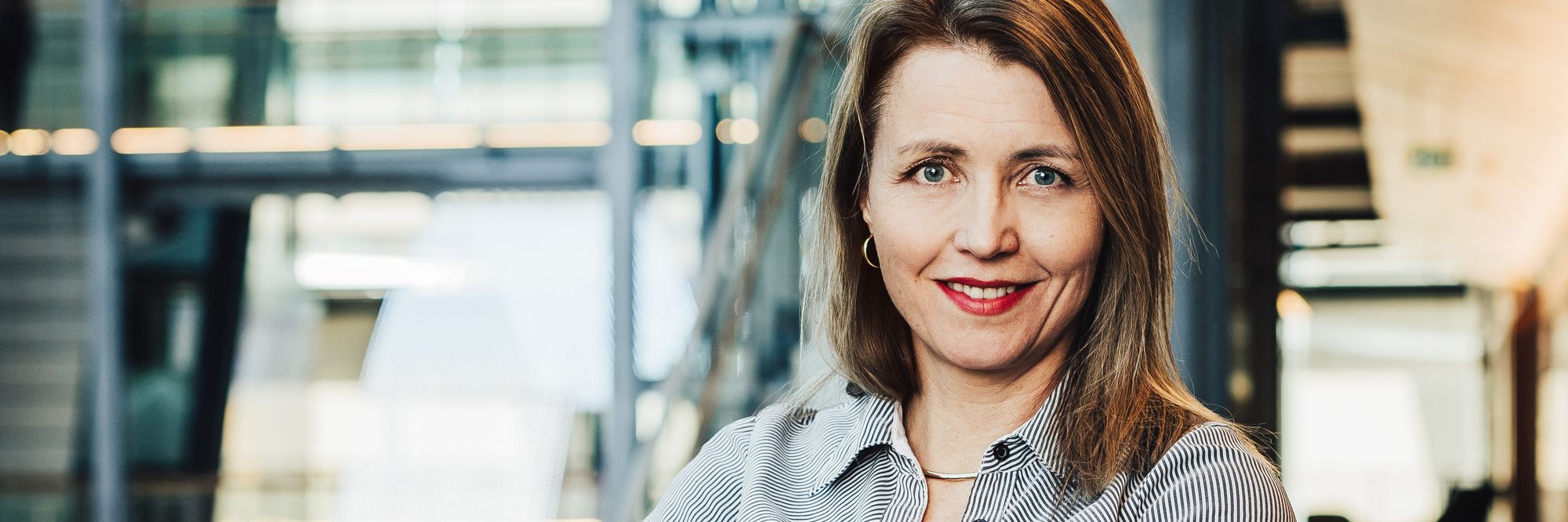
– Ikke bare spares det energi i prosessen, men siden energien (varmen) til kolonnene kommer fra forbrenningsanlegg, men man får samme prosentvise besparelse i CO2-utslipp.
Han viser til en kolonne på Kårstø som kanskje har ca hundre trinn. Her kan et tettere integrert anlegg ved å koble om kolonner på en ny måte, føre til stor energisparing.
– Et tredje pluss er at når man reduserer energibehovet, minskes også den innvendige dampstrømmen fra kokeren, og dermed kan dimensjonene på kolonnen slankes. Dette, sammen med at det brukes færre kokere og kondensere fører til at kapitalutgiftene for slike kolonner er lavere enn for tradisjonelle løsninger. Det vanlige er jo at jobben med energikutt fører til nye kostnader på grunn av nytt utstyr, som for eksempel vil man måtte øke arealet i en varmeveksler for å få mer effektiv energioverføring
I drift
Den nye kolonnetypen er allerede i drift enkelte steder. Det store kjemikaliekonsernet BASF i Tyskland har mer enn hundre i gang. Her har forskeren Gerd Kaibel vært drivkraften for å bygge kolonner med interne vertikale skillevegger fra 80/90-tallet. Kolonnene integrerer funksjonen til flere tradisjonelle kolonner i en. BASF har funnet at de tjener på dette både fordi det gir både lavere energibruk og reduserte kapitalutgifter, og gjort dette til en del av sitt standard utstyr fordi det gir dem et konkurransefortrinn.
– Men i Norge er det stille, sier Halvorsen. - Man sitter på gjerdet og venter. På 90-tallet var det en del usikkerhet rundt design og styring. Men det er det ikke i dag. Nå har vi såpass mye erfaring fra BASF at vi ikke støter på overraskelser lenger. Og både USA og Japan er i gang med å ta teknologien i bruk. Europa, ved Tyskland og BASF var først ute, og vi behøver ikke vente på andre.
I følge Halvorsen er det ikke snakk om noe månelandingsprosjekt. Heller som å lande på en flyplass man ikke har vært på før. Litt ny navigering er nødvendig, men det er rimelig trygt, og det koster ikke milliarder av kroner. Tvert imot vil det lønne seg med en gang.
– Utfordringen er å få formidlet at denne teknologien er tilgjengelig sånn at de nye energibesparende løsningene tas i bruk nå i stedet for at man bruker samme løsning som i forrige prosjekt, sier Halvorsen.