TJELDBERGODDEN: – Vårt mål er å ha god og stabil drift og derigjennom levere metanol med høy kvalitet, forteller direktør ved Statoils metanolfabrikk, Jofrid Klokkehaug.

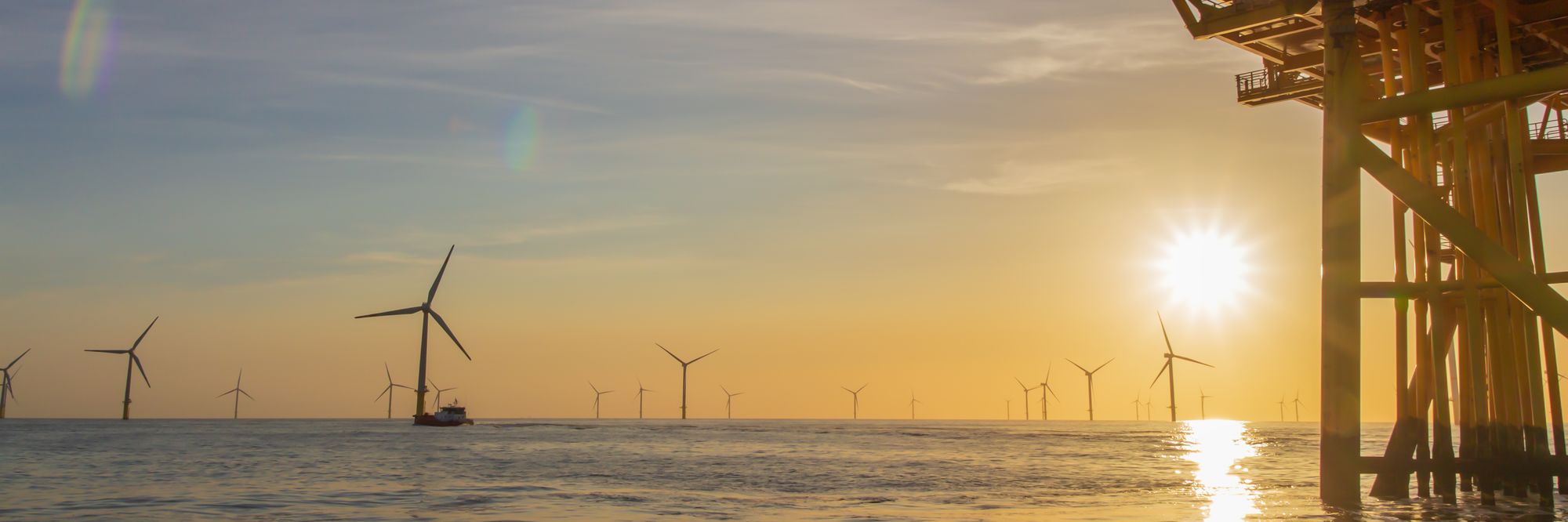
– Vi produserer i dag rundt 900 000 tonn metanol årlig og er Europas største metanolprodusent, forteller hun. I tillegg til metanol produserer anleggene i Aure Kommune på Nordmøre også noe LNG, samt flytende industrigasser som oksygen, nitrogen og argon. LNG og industrigasser selges av AGA som er et Linde-selskap.
Jubilere
5. juni neste år er det 15 år siden fabrikken ble offisielt åpnet, mens de første leveransen av gass fra Heidrun gjennom Haltenpipe startet allerede i desember 1996, slik at det før jul er 15 år siden det ble gass i anlegget.
Selv om Statoil og partnerne på Heidrun må fornye driftslisensene for feltet i henholdsvis 2024 og 2025, så er ikke det ensbetydende med at feltet stenger ned. Statoil som operatør på Heidrun, er godt i gang med å utvikle nye produksjonsplaner for feltet, og har allerede i år økt den daglige produksjonen fra 56 000 fat til 75 000 fat oljeekvivalenter.
Gjennom bruk av blant annet ny boreteknologi skal utvinningsgraden økes fra opprinnelige 35 prosent til 53 prosent. Det innbærer drift og produksjon på Heidrun fram til 2045 som er utløpet på neste konsesjonsperiode for feltet. Så foreløpig kan 2045 bety et endeligt for anlegget på Tjeldbergodden. Få andre industrianlegg kan skilte med et så langt perspektiv.
Lave utslipp
Metanolfabrikken er Europas største, og den mest miljøvennlige. Da anlegget ble konstruert ble det lagt stor vekt på energigjenvinning slik at varme fra prosessen genererer store deler av forbruket av elektrisk kraft. – Da anlegget ble bygget var vi det største enstrengs (dvs. et prosesstog) som var bygget med vår kapasitet på 2500 tonns produksjon om dagen. Nå ser vi at det bygges anlegg med dobbelt så stor kapasitet. forteller Lars Bjørnar Lynmo, leder for forretningsutvikling.

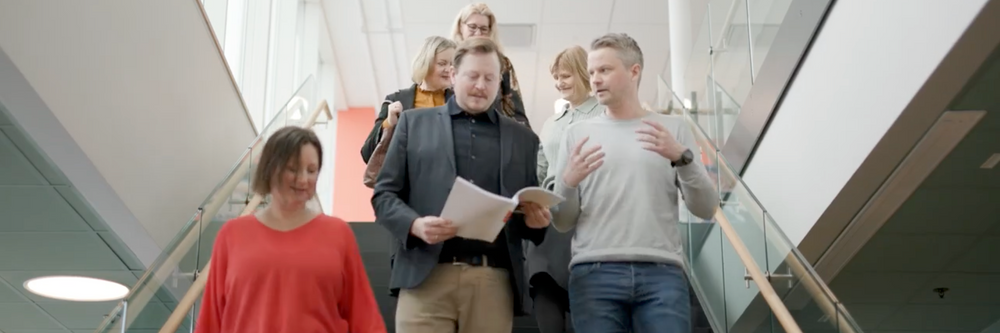
– Vi er det eneste anlegget i Norge som bruker naturgass som råstoff, og det er ingen som produserer metanol med så lave CO 2-utslipp som oss, sier Klokkehaug.
Flerfaglige
Fabrikken drives effektivt. Det er i alt 140 ansatte ved anlegget samt rundt 20 lærlinger. Operatørene går en syvskiftsordning.
– Noe av det vi legger vekt på er at de ti personene som til enhver tid er på skiftet som betjener anlegget også får med seg en lengre dagskiftperiode i løpet av året , slik at de blir en integrert del av den øvrige driftsorganisasjonen og ingeniørstaben. Vi legger også stor vekt på at operatørene er mulitidisipline og dekker flere fagområder. Det gjør hverdagen mer spennende og utfordrer de ansatte på en positiv måte, sier Klokkehaug.
– En av de store fordelene er at vi i motsetning til de fleste sammenlignbare anlegg, har kontrollrommet i administrasjonsbygningen. Det medfører at det blir tett kommunikasjon mellom ingeniørene og operatørene. Vi mener det gir sikrere og bedre drift fordi det er korte kommunikasjonsveier, sier Klokkehaug.
Mange lærlinger
Metanolfabrikken på Tjeldbergodden fungerer i likhet med Statoils andre landanlegg, som en god opplæringsinstitusjon. Til en hver tid er det to kull med lærlinger innen industrifag som mekanikere, automatikere, elektrikere, prosessoperatører osv.
– For oss er det mye enklere å ha lærlinger på et landanlegg enn offshore. Der et det alltid plassutfordringer og ikke alltid like enkelt å ha med seg en lærling ut i havet. Her er det enklere og mer oversiktlig i tillegg til at vårt prosessanlegg er langt mer komplisert enn anleggene offshore. Vi mener derfor at lærlingene får en bedre opplæring her. Noe som gjør dem i bedre posisjon når de en gang skal søke på jobber i Statoil eller hos andre, sier Klokkehaug.
Selvforsynt med energi
Prosessen for å danne metanol fra naturgass krever mye energi i form av varme og damp. Gassen som kommer gjennom Haltenpipe trykkavlastes fra 140 bar til 50 bar. Det første som gjøres med gassen er at den renses for svovel, deretter går den gjennom en totrinns reformering, først med damp og deretter med oksygen for å danne en syntesegass. I begge disse reaktorene kreves det varme og damp.
Selve dampsystemet er et lukket system hvor mye av energien gjenvinnes over en turbogenerator. Denne er i prinsippet stor nok til at metanolanlegget er selvforsynt med elektrisk energi.
Syntesegassen sendes videre til en metanolreaktor som danner råmetanol som deretter blir raffinert til metanol med 99,85 prosent renhet. Syntesegassreaktorene er basert på teknologi fra Haldor Topsøe i Danmark, mens metanolreaktoren er fra tyske Lurgi. Rafineringsprosessene er basert på teknologi utviklet av DuPont og Statoil.
Nær markedet
– Anlegget her på Tjeldbergodden ligger gunstig til og nær markedene i Europa, stort sett et døgns seilas fra oss. Det betyr at vi har en stor markedsfleksibilitet i forhold til våre konkurrenter, forteller Klokkehaug.
En vanlig last til Europa er på ca. 7 000 - 8000 tonn metanol. Det betyr at det kan være skipsanløp hvert andre eller tredje døgn.