Biri:
Norsk skiindustri er ikke som den var. Det er ikke lenger én produsent i hver vinterbygd, og de gamle hickorybearbeiderne er historie. Nå er det bare én stor produksjonsbedrift igjen, og den er ikke en gang norskeid. Madshus, som ligger på Biri ved bredden av Mjøsa, ble kjøpt av amerikanske K2 for ti år siden. Allikevel klarer den tradisjonsrike bedriften å hevde seg i den intense internasjonale konkurransen. Ved å satse på teknologi har de sakte, men sikkert klatret opp til å bli verdens nest største produsent av langrennski.
I 1990, da Madshus ble kjøpt av K2, lå norsk skiindustri langt nede. Markedet var dårlig for det som kalles nordiske ski, det vil si langrennski. Mange nye konkurrenter sloss om markedet.
Fra laminat til kompositt
Madshus ville hatt store problemer hvis det ikke hadde vært for K2, som investerte flere titalls millioner kroner i fabrikken på Biri, forteller teknisk direktør for Madshus, Gunnar Bjertnæs. – En viktig årsak til fusjonen var en gjensidig interesse for teknologien hos moder- og datterbedriften. K2 hadde utviklet en treaksial fiber-veveteknikk, og vi hadde utviklet en avansert støpeprosess. Begge selskapene ønsket å lage ski basert på tredimensjonal komposittkonstruksjon i stedet for de laminatbygde ski som var vanlig på den tiden, sier Bjertnæs.
I 1994 var den nye konstruksjonen ferdig. Det store gjennombruddet kom da Thomas Alsgaard tok olympisk gull med disse skiene samme år. Seieren gjorde sitt til at salget av nordiske ski igjen begynte å ta seg opp.
I plastskall
Etter fusjonen med K2 ble Madshus også et betydelig produsent av slalåmski og produserte opptil 85.000 par i året. Dette markedet har utviklet seg negativt på grunn av større konkurranse og at flere kjøper snowboard i stedet for ski. I dag produseres ikke lenger slalåmski i fabrikken på Biri.
Allerede i 1990 lanserte Madshus den teknologien de kaller Cap, som ikke er noe avansert akronym, men som står for noe så enkelt som en hatt. Teknologien går ut på å lage et skall i hard PMMA-plast, mer kjent som pleksiglass, og støpe skien inne i denne. En av fordelene som den 0,2 mm tynne gjennomsiktige plasten byr på, er at fargen og mønsteret kan trykkes på innsiden der den er beskyttet mot riper.
–- På den tiden tok vi også i bruk moderne DAK/DAP-teknologi som gav oss mye mer nøyaktige langrennski.
Hjemmestrikket

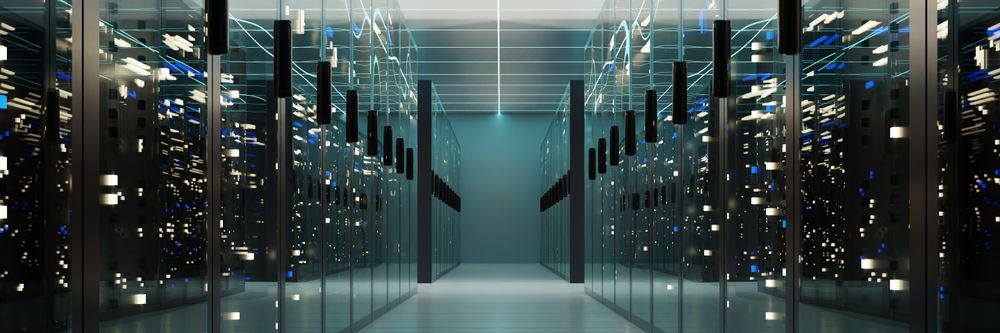
Frem til 1994 ble ski bygget opp som laminat med lagene oppå hverandre. Det året lanserte fabrikken de første modellene bygget med den nye treaksiale veveteknikken. Metoden går ut på å "strikke" en strømpe av glassfiber som omslutter kjernematerialet i skien. Det gir en helt annen tredimensjonal stabilitet fordi fibrene armerer skien i alle retninger og ikke bare i lengderetningen.
De dyreste modellene i dag har en kjerne av superlett polymetacrylimidskum, PMI, og karbonfiberlameller som virker som bladfjærer.
– Du kan se på en ski som en bjelke som skal fordele kroppsvekten best mulig i forhold til snøtypen. Derfor er bjelkens stivhetskarakter vesentlig, og den bestemmes av materialvalg og måten vi bygger opp skien på, sier Bjertnæs.
Den andre viktige parameteren er forholdet mellom snøen og sålen. I tillegg til skismøringen er materialene i sålen og utformingen av den viktig.
Forsker-samarbeid
For å kunne lage best mulig ski har Madshus lenge støttet seg til forskningen. Materialteknologene ved Sintef i Oslo har samarbeidet tett med bedriften og hjulpet til å forbedre materialene og utvikle metodikk for stivhetskarakterisering av ski. Madshus registrerte tidlig varemerket Compuflex, som er en metodikk for å karakterisere spennet i skiene så de passer til brukerne og forholdene de skal benyttes under. – Alle våre toppmodeller som vi selger i dag, er karakterisert slik at de kan velges ut etter ulike spennkurver, sier Bjertnæs.
Et doktorgradsarbeid ved NTNU har vært viktig for å forstå samvirket mellom snø og ski og har gjort det mulig å lage bedre såler.
Mer skreddersøm
Ulike stilarter og krav gjør at kjøperne stiller stadig større krav til skiene. Ski som benyttes til skøyting, er blitt svært forskjellige fra vanlige ski. Tidligere var slike ski helt rette, men i dag har de en spesiell innsving, samtidig som de har større sidestivhet enn vanlige ski.
– Det er viktig at spennkarakteristikken på slike ski passer til innsvingsformen. Ski til skøyting må også ha en mye større vridningsstivhet som vi har løst ved en slags rørkonstruksjon, sier Bjertnæs.
Tidligere produserte Madshus lange serier av samme modell i en måned av gangen. I dag er produksjonen svært fleksibel. Opptil 25 ulike modeller lages hver dag. Ifølge Bjertnæs vil markedet kreve stadig mer skreddersøm, og Madshus er godt forberedt på denne trenden.
I løpet av få år har Madshus blitt verdens nest største produsent av langrennski. Til sammen selger bedriften 175.000 par i året. De billigste modellene blir laget i utlandet, men 75 prosent av den omsatte verdien kommer fra produksjonen på Biri.
Et bevis på at nordmenn ennå kan lage ski, får vi fra et ledende skimagasin som nylig testet 11 toppmodeller for skøyting. De slår fast at noe bedre produkt enn modellen fra Biri finnes ikke. – Ingen andre produsenter slår oss på teknologi, slår Bjertnæs fast.