ABB has signed two contracts worth a total on NOK 1.9 billion to provide technology, power supply and drive systems as well as a new compressor module for Statoil's Troll A platform. The project is also a breakthrough for use of ABB's HVDC Light technology in an offshore context. The new solution has been engineered and tested in close collaboration with Statoil. Work on the two contracts will be over a 3 1/2 year period. Troll A is the first plattform fully power supplied from the shore based, hydro driven norwegian electricity network.
High-voltage direct current
The contract for the DC system is for NOK 600 million and is to be delivered by ABB's Process Industry Division. The newly developed power transmission system is well suited to offshore use due to its compact size and low weight.
The contract includes design work for building two HVDC Light-based drive systems for the two compressors to be installed on the platform. The project includes preparations for delivering and installing rectifier stations in Kollsnes, DC cables (70 km) to Troll A and inverter stations and motors on the platform itself. The two motors, each 40 MW, will drive the compressors to be installed.
The electrical drive system, which is to power the new compressors on Troll A, is based on several newly developed technologies in the area of high-voltage power transmission. Although all the technologies have been previously used in other projects from ABB, in this project the components will be assembled for the first time into an electric drive system.
High-voltage motor
A big advantage of the system is that a transformer is not required on the platform, since the high-voltage motor (60 kV) is fed directly from the inverter, yielding significant weight reductions compared with a traditional system based on AC and large transformers.
In 1997 ABB launched a new technology for DC power transmission based on voltage-fed converter technology - HVDC Light. It uses pulse-width modulation (PWM) for generating a fundamental harmonic voltage. Using the PWM technique, the amplitude and phase angle of the voltage can be freely controlled within certain limits. This permits independent and very rapid regulation of the active and reactive power output.
The component offering the most intriguing possibilities for the DC power system is a so-called insulated-gate bipolar transistor (IGBT). This is a metal-oxide semiconductor (MOS) that requires minimal control power. The power can be taken from the main circuit via attenuation circuits across each IGBT, making possible a serial connection of IGBTs with good voltage distribution even with switching frequencies in the KHz area. The high switching frequencies mean that only relatively small filters are necessary.
Cost-effective cable
The concept includes another innovation: the HVDC Light cable, an extruded polymer cable. For high-voltage AC there has been a shift in technology from paper-insulated to extruded polymer cables. A similar development for producing an extruded HVDC cable has yielded a flexible, cost-effective product that is an important part of the entire concept.

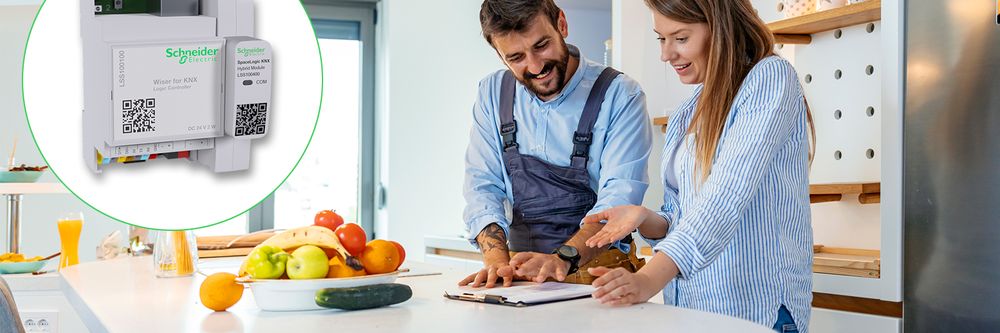
Operating experience confirms quick and precise control of active and reactive power output in step with variations on the grids. The favourable experience with the transmission systems already installed also show that HVDC Light stations can be designed so that shutdowns for maintenance are necessary only every other year - and then only for a few days. The installation's lifetime is more than thirty years and predicted availability is above 99 percent.
High-voltage DC offshore
"With offshore use of high-voltage DC, we have to concider that the systems, components and resources being used are well known from land-based projects, but provide new challenges when they are assembled into a drive system offshore," says project director Olav Hagen with ABB's Process Industry Division. Besides the technical challenges presented, the project will focus particularly on safety in order to live up to Statoil's mandated zero-injury philosophy during project implementation and to ensure reliable operation during the installation's lifetime.
On an offshore installation, the amount of weight that can be added as well as any spare space is limited and is therefore precious to the operator. The equipment must be compact with a minimum weight. That is why the voltage-fed converter technology has particular advantages over classical high-voltage DC. The filters are small and there is no need for a rotating phase advancer.
The new type of motor (Motorformer) uses round instead of square conductors in its windings. Although the superiority of using round conductors in high-voltage systems is well known in theory, practical use has presented problems. The Motorformer is a synchronous motor that is based on a new cable technology.
Protected by over 200 patent applications, this new technology makes it possible to dispense with a number of components normally found in conventional installations with motors. This means lower costs for service, maintenance and spare parts.
Avoids emissions
ABB Offshore Systems has the NOK 1.3 billion contract to deliver the 4,000 tonne compression module. Since the reservoir pressure in the Troll field is falling, there will be a need in 2005 to compress the gas. The compressors will increase today's capacity to process gas on Troll A from 85 million to 100 million standard cubic metres of gas per day, counteracting the effect of the sinking pressure in the Troll field's gas reservoir.
"Unlike the conventional gas turbines traditionally used to generate power for compressors offshore, using an electric drive system will mean avoiding high levels of CO 2 and NOx emissions," says Rune Finne, head of ABB's Process Industry Division in Norway.