I september åpnet Corvus Energy ny fabrikk i Bergen, fullautomatisert med kun to ansatte i produksjonen. Tyske Siemens startet også ny produksjon av batterier i Trondheim i januar. Begge fabrikkene er automatiserte langt ut over det som er vanlig i norsk industri, begge leverer batterier til maritim industri og begge fabrikkene er nye.
Så har de ytterligere én ting til felles: Intek Engineering på Raufoss har utviklet og levert automatiserte produksjonsanlegg til begge to.
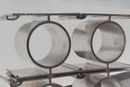
Bruker aluminium til ny skredsikring
Fleksibilitet
– Fortsatt bruker de aller fleste produksjonsbedriftene tradisjonelle produksjonslinjer, sier salgsdirektør Sølvar Flatmo hos Intek Engineering. Han var ansvarlig for de to leveransene.
Administrerende direktør Anita Hager i Intek Engineering synes det er flott å bli nominert til Norwegian Tech Award.
– Det er en anerkjennelse for den jobben vi gjør. Så er det ekstra hyggelig at det er knyttet til de to batterifabrikkene. Det er her vi har gjort de største nyvinningene, og det til en grønn industri, sier Haga til TU.
Hun sier at det er ekstremt krevende å utvikle et system som består av mange robotceller som skal «prate sammen» og koordineres.
– Roboter er ikke noe nytt. Nyvinningene ligger i alt det du ikke ser. Alt er kobla til alt – og alt skal samkjøres, koordineres og kommunisere og kobles til kundens ordresystem, sier Hager.
Legger inn feil
Gisle Frydenlund, driftsdirektør hos Corvus, forteller at det var både norske og utenlandske selskaper som viste interesse. Totalpakken til Intek skilte seg ut, og kravet til fleksibilitet var godt ivaretatt. Intek valgte en matriseløsning med ni produksjonsceller med 13 roboter og ni autonome små trucker som frakter komponenter fra celle til celle. Det åpner for raskere endringer eller utvidelse av kapasiteten.

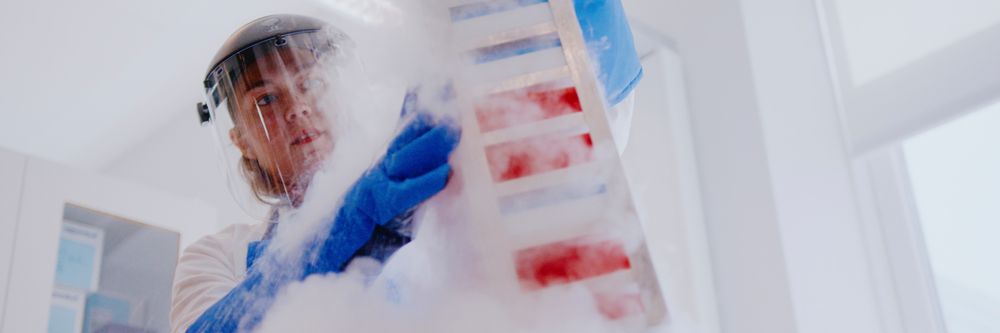
Nye produksjonslinjer krever alltid innkjøring. Det er forhold som må justeres og tilpasses, av og til endres. Det er ikke uvanlig at innkjøringsperioden strekker seg over måneder, men slik er det ikke i Bergen.
– Vi har kjørt for fullt nå fra midten av oktober, sier Frydenlund.
Da Teknisk Ukeblad besøkte fabrikken i Bergen, noen dager før full produksjon, hadde Intek flere ingeniører i lokalene. De var ikke der for å rette feil.
– Vi provoserer frem feil og legger inn feil med hensikt. Det gjør vi delvis for å trene, men også for å kunne luke ut flest mulige feilkilder før produksjonen går for fullt, sier Frydenlund.
Kontrakten med Intek ble signert i november i fjor. Å begynne installasjonen et halvår senere og sikte mot full produksjon mindre enn et år etter å ha vunnet kontrakten, er uvanlig raskt. Det var et av kravene fra Corvus.
– Enkelte av de mulige leverandørene klaget på tidsfristene, er alt Frydenlund vi si om det.
Automatisert eskeåpner
Den høye automatiseringsgraden er uvanlig selv i internasjonal sammenheng. Slettaløkken peker på at i mange industrialiserte land med langt høyere robottetthet enn Norge, er det vanlig å automatisere opp mot 70 prosent av operasjonene.
Årsaken til det er at industriarbeiderlønningene i de fleste landene er lavere enn her hjemme. Et slikt oppsett ville vanskeliggjort batteriproduksjon i høykostlandet Norge.
En typisk manuell jobb i et delvis automatisert anlegg er håndtering av esker. En industriarbeider henter esker med komponenter, åpner esken og setter den på en angitt plass.
– Vi har nå utviklet en eskeåpner som automatiserer hele operasjonen. Dette er en nyvinning vi ser kan brukes i en rekke oppsett og produksjonslinjer, sier Flatmo.
Maskinlæring
Både Flatmo og administrerende direktør Antia Hager i Intek er stolte av hva de har fått til med kunstig intelligens og maskinlæring. Tradisjonelt har roboter utført enkle repeterende oppgaver, AI, eller kunstig intelligens var inntil nylig nærmest et buzz-ord med lite konkret innhold. Slik er det ikke lenger. Intek Engineering bruker det i praksis.
Robotene vet hvilke toleranser som er akseptable. Om for eksempel 13 mm avvik er innenfor, og tre av dem er brukt i et tidligere steg i produksjonen, så vet den aktuelle roboten at nå har den ti millimeter å gå på. Denne løsningen bidrar til å redusere svinnet og også å redusere stans i produksjonen.
– Vi bruker kunstig intelligens og maskinlæring i deler av prosessen. Målet er å få maskinene til selv å forstå prosessene de utfører og gjøre tilpasninger, sier Flatmo.
Han forteller at dette er nyttig for eksempel der det er ubetydelige variasjoner i komponenter. Hvis en ny sending fra en leverandør kommer med en annen farge på deler av komponentene, vil den ikke bli gjenkjent uten kunstig intelligens. Flatmo forteller at det fort ville krevd 200 timer med programmering i et tradisjonelt system. Men i Bergen ser roboten at det faktisk er samme komponenten, og produksjonen går videre uten behov for omprogrammering eller produksjonsstans.
Her ligger det store innsparingsmuligheter. Ikke minst fordi det inngår et sted mellom 50 og 100 komponenter i et batteri. Nøyaktig antall er en bedriftshemmelighet, men Frydenlund røper at de har klart å redusere antallet komponenter til en fjerdedel av opprinnelig antall.
Hjelp meg!
Under utviklingsarbeidet dukket det av og til opp pussigheter.
– En morgen vi kom på jobb stod en av de autonome truckene ute på plassen og ropte på hjelp. «Jeg vet ikke hvor jeg er, hjelp meg», ropte den. Den hadde klart å snike seg ut porten uten at det ble oppdaget, sier Flatmo.
– Vi fikk den inn igjen, og rettet feilen.
Disse små autonome truckene er en av sidene ved leveransene ingeniørene hos Intek er mest stolte over.
– Flåtestyring av AIV-er, autonomous intelligens vehicles, er helt nytt. Vår bestilling til Omron var den største de noen gang hadde fått i Europa.
De små truckene kjører på kryss og tvers, systemet sikrer at de er på rett plass til rett tid. Samtidig må de unngå å kollidere, og skal selv kople seg til lader. De kjører til ladestasjon når det passer best, ikke når batteriet når et på forhånd definert nivå.
– Det var vanskelig. Det er nybrottsarbeid, og vi måtte lage et tillegg til flåtestyringsprogrammet som ligger i bunn, sier Hager.
Palettene med komponenter som truckene henter, ser ut som enkle aluminiumplater. Men bak overflaten skjuler det seg kunstig intelligens.
– Med en gang de har hentet en palett så vet truckene hva som er på, og hvor de skal frakte den, forteller Bjørn Morten Orderløkken, som har hatt hovedansvaret for programvareutviklingen i prosjektet.
Flere og færre ansatte
Intek har økt fra 32 til 50 ansatte som følge av de to batterikontraktene. Nå, som begge går mot slutten, er likevel ordrebøkene fulle, forteller Hager. Intek har eksportert gjennom norske kunder, men ikke mye.
– På noen års sikt skal vi ut i verden. Det meste vi gjør er helautomatisering, og der er vi gode. Foreløpig ser vi sterk vekst i Norge, og vi ser at mange henter produksjon hjem, sier Hager.
Et mulig eksportprosjekt kan bli Corvus Energys fabrikk i Canada. Der står rundt 30 medarbeidere for en produksjon som kan sammenlignes med den to personer håndterer i Bergen.
– Det er ennå ikke tatt noen beslutning, men den fabrikken står foran en oppgradering. Vi har en samarbeidsavtale med Intek, og vi har dialog med dem om leveranser til Canada, sier Frydenlund.