FARSUND: – Vi er ekstreme på å utnytte Lean-tankegangen i vår virksomhet. Måten vi organiserer oss på er spesiell. Så langt råd er bruker vi de ansattes kompetanse for å hele tiden oppnå forbedringer. Vi bruker kompetansen de har i praksis, sier verksdirektør Kai Rune Heggland til Industrien.
Han styrer en ekstremt flat organisasjon med kort vei fra operatører til øverste ledelse. Mange mellomledd er kuttet ut. Bedriften har i dag 293 ansatte, hvor det kun er 15 personer som har lederansvar. Alle lederne har et resultatansvar, ikke bare ansvar for en oppgave. – Om kvelden og natten, helger og helligdager har vi kun operatører i arbeid som leder sitt eget arbeid. På denne måten drar vi nytte av den enkeltes kompetanse inn i driften av aluminiumsverket.

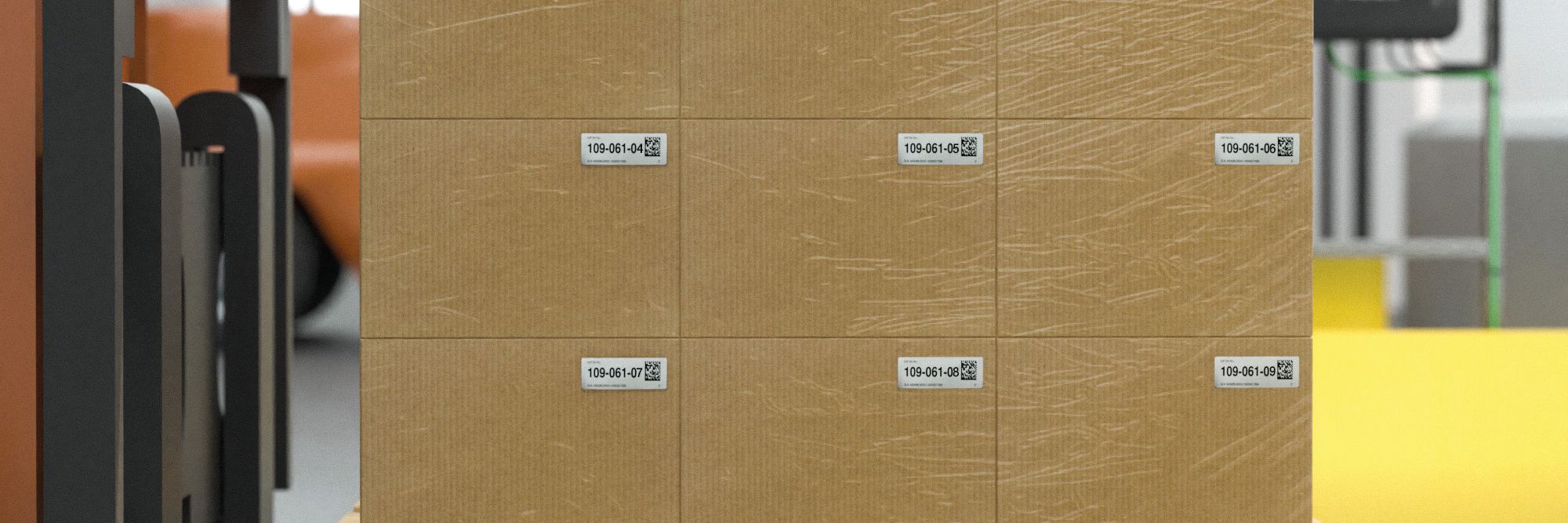
Bruker realkompetansen
– Vi er blant de tre beste på å gjennomføre Toyota-tankegangen i Alcoa. Vi har holdt på med dette siden 1997 og driver fortsatt på. Lean-metodene er bygget inn i driftsmodellen og utnytter de ansattes realkompetanse i praksis når vi overfører ansvar ned til hver enkelt ansatt, sier Heggland. Han mener det er viktig å sikre eierskap til de forskjellige prosessene blant de ansatte. Det gjøres gjennom klare roller, klare standarder og kommunikasjonssystemer med klar og entydig oppfølging og tilbakemeldinger, samt et definert opplæringssystem blant de ansatte. – Vi har et nært samarbeid med skolene for å sikre oss lærlinger i distriktet i tillegg til at vi tar inn ungdom i sommerjobb og lærer dem opp. Slik sikrer vi framtidig rekruttering, sier Heggland.
Ingen overflødige
Gjennom forskjellige rasjonaliseringstiltak, økt grad av automatisering og aktiv bruk av Lean-tankegangen, har Alcoa Lista redusert bemanningen fra 752 personer i 1992 til dagens nivå på 293 personer. Da er noen oppgaver satt ut, som rengjøring, vakttjeneste, kai og kantine.
– Vi har kuttet ut all overflødig bemanning. Men vi har beholdt fleksibiliteten. Vi hadde ingen permitteringer under finanskrisen, forteller Heggland.
Bruker Søderberg
I motsetning til andre aluminiumsverk i Norge, har Alcoa Lista Søderbergovner fortsatt. Mens Hydro har stengt ned sine Søderberglinjer både på Karmøy og i Årdal så går ovnene i hallene på Lista for fullt. Forskjellen er at Lista har lukket ovnene slik at de skadelige gassene fra tjære som blant annet inneholder fluorforbindelser ikke slipper ut i ovnshallen eller til atmosfæren.
Alcoa Lista er det eneste smelteverket med Søderberg-linjer som har lyktes med dette. Derfor har de også lyktes med å overføre teknologien til Alcoas to verk i Spania, og Alcoas Søderbergverk i Brasil. Teknolgien er også solgt til russiske Rusal i forbindelse med et større moderniseringprograv for dere aluminiumsverk. Alcoa er også i forhandlinger med andre aluminiumsprodusenter som ønsker å bruke dere teeknologi for lukkede Søderbergovner. – Vi vil ha full kontroll på teknologien, derfor må de som kjøper teknologien kjøpe alt eller intet.

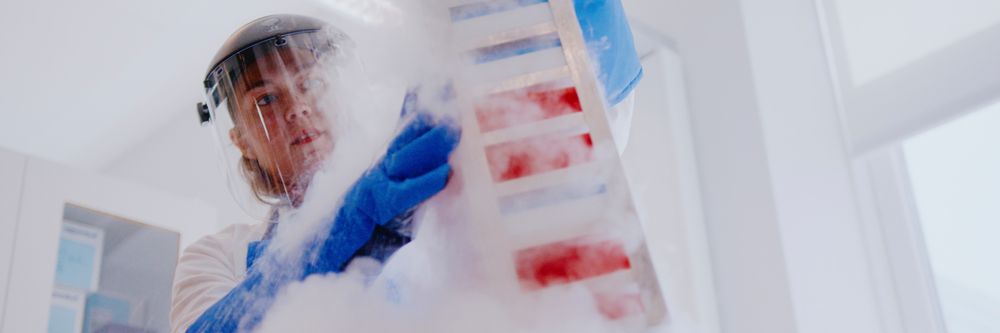
Kutter CO
– Vi har utviklet teknologien for å lukke ovnene selv. Ved å lukke ovnene kan vi brenne avgassene kontrollert og dermed redusere de skadelige utslippene. Dette og andre tiltak har medført at vi har redusert klimagassutslippene fra 540 000 tonn CO 2-ekvivalenter i 1990 til 190 000 tonn i år. 350 000 tonn av dette kommer av endrete prosessbetingelser, forteller Heggland.
Som første smelteverk er Alcoa Lista sertifisert for sin energiledelse av Det Norske Veritas etter normen EN 16001. Bedriften samarbeider blant annet Alstom for å resirkulere varmestrømmene på verket.
Framtidens aluminiumsverk
Et av de mest spennende tilbake på Lista er den planlagte utbyggingen med et prøveanlegg for den karbotermiske framstillingsprosessen for aluminium. Denne har vært utviklet i samarbeid mellom Elkem og Alcoa og er i dag heleid av Alcoa etter at de kjøpe opp Elkems aluminiumsaktiviteter. Prosessen har hittil vært testet ut ved Fiskå i Kristiansand, mens en oppgradert versjon er planlagt bygget ved Alcoa Lista.
Denne prosessen reduserer energibehovet med 30 prosent sammenlignet med elektrolysen som brukes i dag. CO2-utslippene kan elimineres, da prosessen kun slipper ut CO som kan brukes i andre industrielle prosesser eller til energiproduksjon. En annen stor fordel er lavere drifts og investeringer, samt at den er langt mindre arealkrevende, og dermed gir muligheter for småskalaproduksjon av aluminium.