TJELDBERGODDEN: Regnet pisker på den nordmørske kysten. Frode Roness lar seg ikke affisere. Entusiastisk slår han ut med armene, peker og forklarer hva slags rolle hvert bidige rør og hver boks spiller i Reinertsens fullskala testanlegg for membranbasert hydrogenproduksjon.
I ett år framover får Reinertsen lov til å tappe syntesegass fra Statoils metanolfabrikk og kjøre gjennom sin membranseparator.
Reinertsens pilotanlegg, offisielt kalt «Mobile test unit for hydrogen production with CO2 capture», står bare og venter på at Statoil åpner ventilen og slipper på gass.
– Vi er ikke i tvil om at teknologien virker også i fullskala. I løpet av det kommende året skal vi «fintune» og optimalisere drift og komponenter, sier prosjektleder Frode Roness.
Se 360/VR-video hvor Roness forteller om anlegget øverst i reportasjen.
- Krever 186 millioner ekstra: Den 50 meter høye prestisjedammen ble vanskeligere å bygge enn planlagt.
100 prosent rent hydrogen
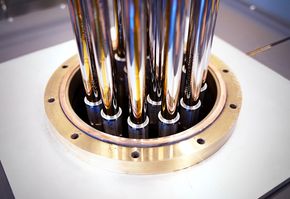
Nøkkelen til det som er en liten teknologisk revolusjon står «gjemt» inne i en stålsylinder.
Det er syltynne palladiummembraner trukket over perforerte rør. Sintef har utviklet teknologien for å lage tynne membraner av grunnstoffet palladium.
Reinertsen har sammen med Sintef utviklet teknologien for å legge noen mikrometer tynne palladiumflak på rørene.

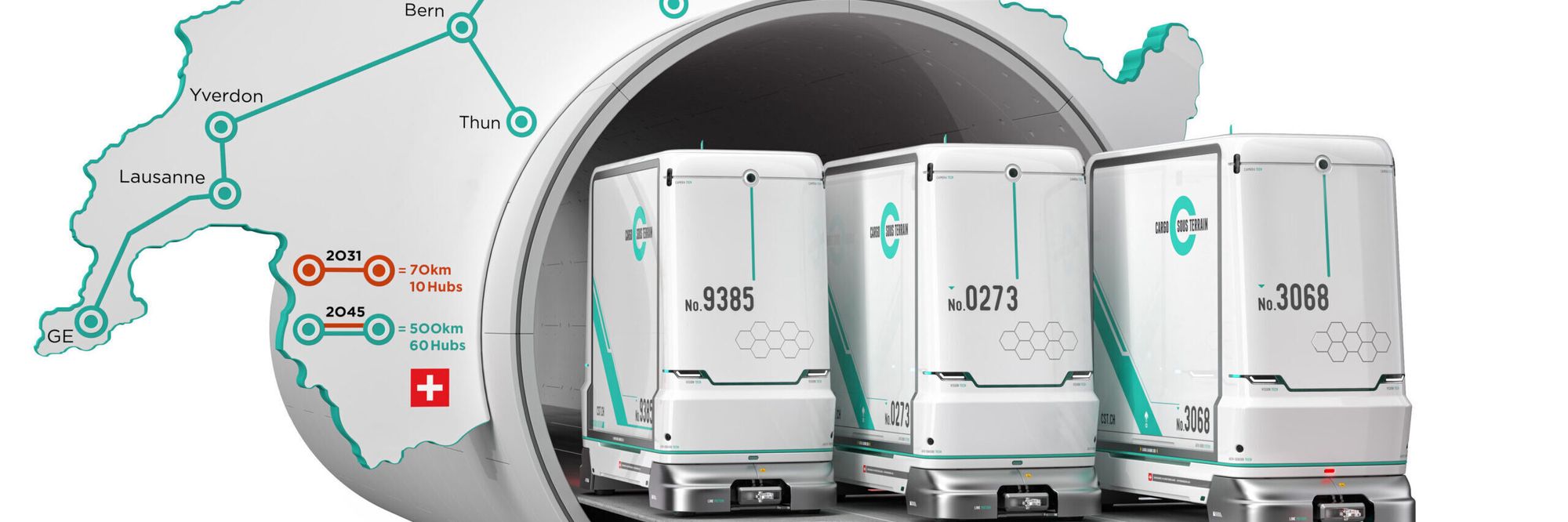
– Palladium er 100 prosent effektiv og slipper bare H-molekyler igjennom. Utfordringen er å få alle sammenføyninger helt tette slik at vi ikke får forurensning i hydrogen-strømmen, sier Roness.
Som et kinderegg
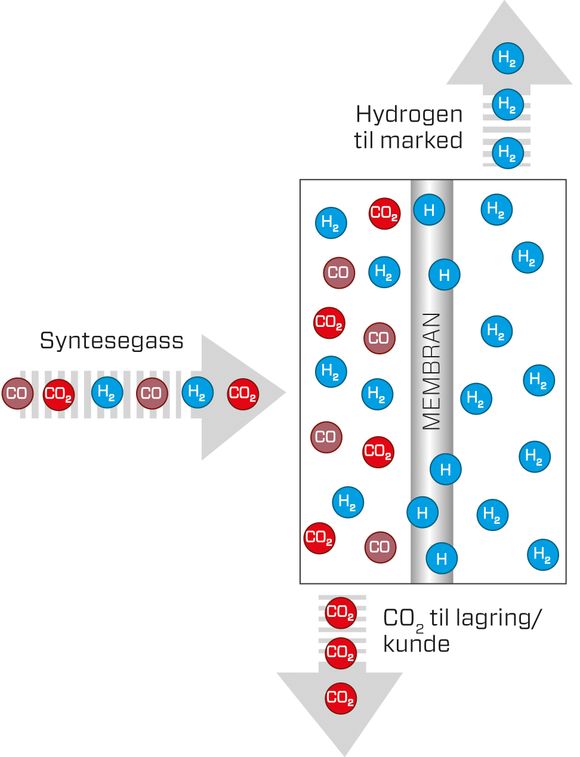
Testanlegget består av en membranmodul med tilhørende rør og ventiler for å ta i mot syntesegass med et trykk på 30 BAR og en temperatur på rundt 320 grader.
Inni et 2,5 meter høyt tårn befinner det seg 19 rør med membran med et areal på cirka tre kvadratmeter.
Syntesegass består hovedsakelig av karbondioksid (CO2), karbonmonoksid (CO) og hydrogen (H2). Når hydrogen fjernes, sitter man igjen med nesten ren CO2, eventuelt med noen rester av metan og CO. Testanlegget kan fange 0,5-2 tonn CO2 per dag.
Det kan se ut som et kinderegg.
CO2 kan lagres i tette formasjoner under havbunnen eller selges til industrielle prosesser. Hydrogen kan brukes som brenngass i kraftverk, til oppvarming, som drivstoff i biler, ferger, skip og tog, eller som drivstoff i brenselceller til strømproduksjon. Restproduktet, eller «eksosen», er vann, H2O.

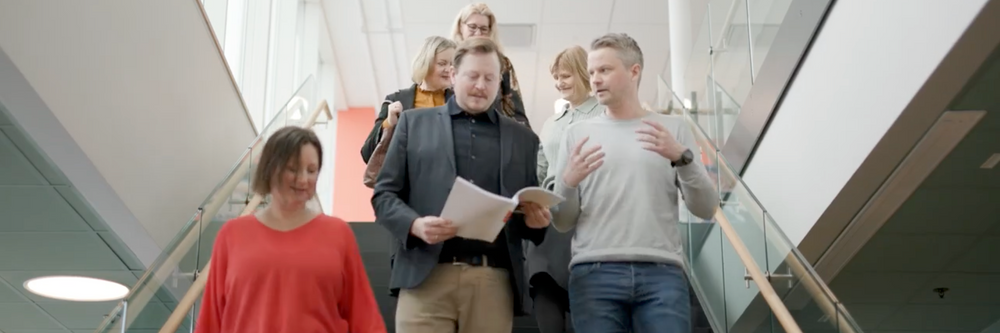
- Oljekrisen får skylden: Om 20 år kan Norge ha 57.000 overflødige ingeniører
Ville bidra til månelanding
Sintef har utviklet teknologien, men manglet en industriell aktør.
Konsernsjef Torkild Reinertsen hadde vært på miljødirektør Nils A. Røkke i Sintef og spurt om de hadde teknologi som egnet seg for CO2-fjerning.
Reinertsen ville bidra til «norsk månelanding», som daværende statsminister Jens Stoltenberg lanserte i 2007.
– Første gang jeg spurte Sintef, hadde de bare amin-teknologi for å fjerne CO2 fra eksos. Det var jeg ikke interessert i, forteller Reinertsen til Teknisk Ukeblad.
I 2011 snakket han igjen med Sintefs miljødirektør Nils A. Røkke, og da hadde forskningsstiftelsen utviklet palladium-membranen. Sintef manglet en industriell aktør som kunne ta utviklingen videre.
Reinertsen så potensialet og kjøpte rettighetene til teknologien. Han fikk Gassnova med og startet kommersialisering av hydrogenproduksjon og CO2-fangst med membran. Myndighetene har støttet prosjektet via CLIMIT-programmet.
Nå er det investert totalt cirka 100 millioner kroner i teknologien. Gassnova og Climit har bidratt med rundt 70 millioner kroner og Reinertsen har selv brukt rundt 30 millioner kroner.
Før Reinertsen kan starte den virkelige verdiskapingen, som også innbefatter oppbygging av en fabrikk i Orkanger for produksjon av kjerneteknologien, membraner og rør i trykkammer, må første fase av testingen på Tjeldbergodden gjennomføres.
- Hydrogen vs batteri: – Bra at Musk og Spetalen slår hverandre i hodet
Arbeidsplasser
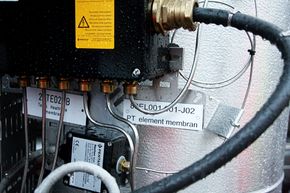
– Vi har fått veldig mange henvendelser og interessenter, men alle venter på resultatene fra demoanlegget, sier Reinertsen.
Reinertsen danner nå et nytt selskap, Hydrogen Mem-Tech AS, og bygger opp en fabrikk på Orkanger der den patentbeskyttede teknologien produseres.
Fabrikken blir dermed plassert midt mellom testanlegget på Tjeldbergodden og Trondheim, der Reinertsen har hovedkontor.
– Vi har lokaler og tomt og har begynt rekruttering. Vi må imidlertid få på plass finansiering fra eksterne investorer på cirka 50 millioner kroner, sier Reinertsen.
– Ligger et par år foran
Han kaller samarbeidet med Sintef et innovasjonsmiljø i verdensklasse.
– Vi har flinke folk hos oss som samarbeider godt med dyktige Sintef-ingeniører. Vi ligger et par år foran konkurrenter og må holde innovasjonstempoet oppe, sier Reinertsen-sjefen.
I tillegg til utvikling av teknologi i det nye selskapet, jobber Reinersten nå med flere studier av hydrogen/CCS-anlegg.
– Vi tror at også dette blir bra forretning ettersom studiene går over i detaljprosjektering og gjennomføring (EPC), sier Reinertsen entusiastisk.
- Unik oversikt: Dette er ryddejobben på norsk sokkel
Plug and play
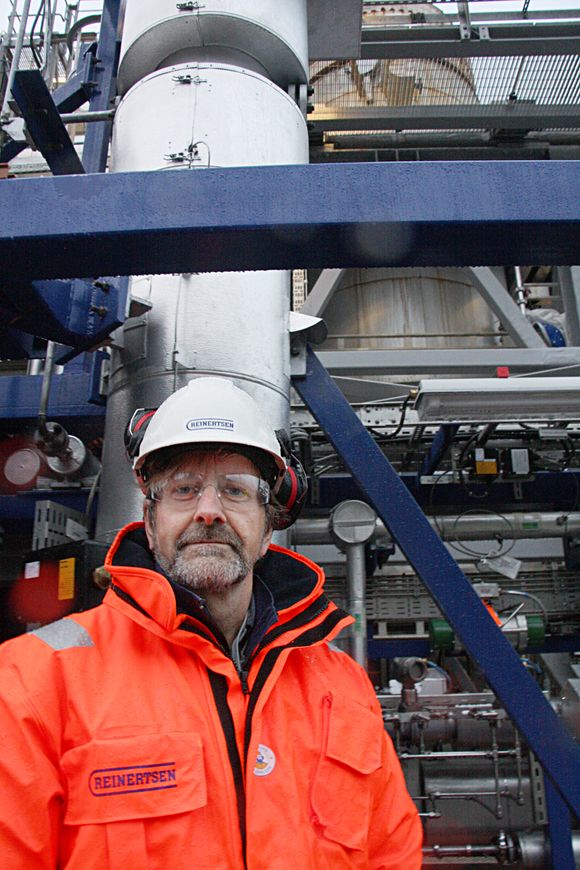
Prosjektleder Frode Roness sier at de under testperioden i tillegg til funksjonsoptimalisering, skal se på en mer hensiktsmessig utforming av et kommersielt anlegg.
– Produksjonskapasiteten på fullskalaanlegg økes ved å sette sammen anlegg med flere membrantårn, sier Roness.
På Tjeldbergodden er testanlegget blant annet laget slik at tårnet med membranrørene kan frakobles og vippes ned for transport tilbake til Orkanger.
– Det har sine utfordringer og begrensninger å operere inne på et prosessanlegg som Tjeldbergodden. Ved å ta med membrantårnet til fabrikken, kan vi gjøre modifikasjoner i kontrollerte omgivelser, sier Roness.
– Noe helt annet å teste i et reelt industrielt miljø
Torkild Reinertsen er svært fornøyd med å få tilgang til Tjeldbergodden. Han roser Statoil for samarbeidet.
– Det var en utløsende faktor for å komme videre med utviklingen. Vi har laboratorietester som viser at dette fungerer også i fullskala, men det er noe helt annet å teste det i et reelt industrielt miljø, sier Reinertsen.
Før Statoil stilte opp, så Reinertsen på muligheten for å bygge et eget lukket syntesegassanlegg for testing i Orkanger, eller å gjøre det i Italia.
– Det ville bli veldig dyrt å lage et eget syntesegassanlegg og reising til Italia var ikke ønskelig. Det ville fordyre og sinke testingen.
Roness tror at Reinertsen fikk lov til å teste på Tjeldbergodden på grunn av selskapets inngående kjennskap til metanolanlegget.
– Vi var med å bygge opp i 1995 og har hatt vedlikeholds- og modifikasjonskontrakt her i 20 år, sier Roness.
- Verftsgiganten skulle gjøre alt i deres makt for å stoppe dødsfallene: Nå går det mot en ny, dyster rekord
Marked utvikles
Statoils prosessoperatør Ken Tommy Lium følger interessert med når Frode Roness forklarer hvordan anlegget er bygget opp.
– Det er svært interessant og spennende å få være med på. Dette er jo litt historisk, sier Lium.
Inne i driftsbygningen sitter driftssjef på Metanolfabrikken, Jostein Voldset.
– Vi er veldig stolte av å kunne bidra til å utvikle hydrogen-teknologien, sier han.
Hydrogen er spådd å bli en viktig energibærer i tida framover. De fleste tenker på hydrogenbil. Torkild Reinertsen sikter ikke mot personbilmarkedet. I hvert fall ikke i Norge hvor vi så å si kan tappe vannkraft rett på batteriet.
– I første rekke er målgruppene storforbrukere som gasskraftverk og kraftkrevende industri. Transport, både ferger og store kjøretøy, er også mulige kunder, sier Reinertsen.
Han ser også for seg at hydrogen kan gå direkte til husholdninger eller produseres og brukes på offshoreplattformer.
Ned i 10-15 kroner kiloen
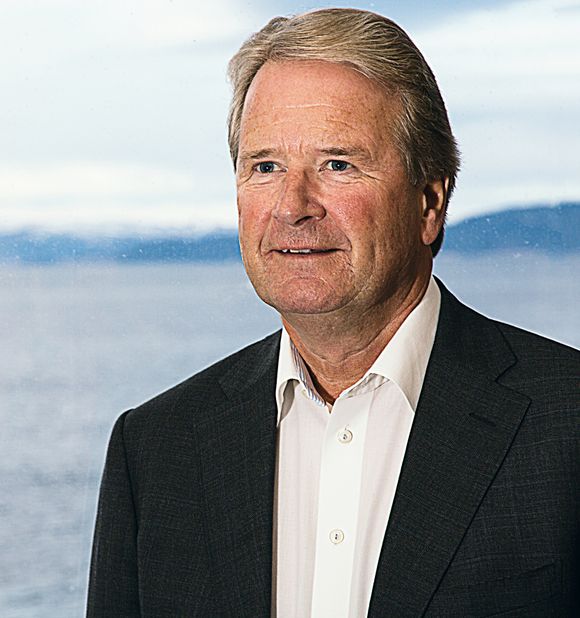
I dag produseres det aller meste, det vil si rundt 95 prosent, eller 500 millioner normalkubikkmeter, av hydrogen fra naturgass ved dampreformering. Produksjonen er energikrevende og virkningsgraden er på 80-90 prosent.
Elektrolyse, det vil si spalting av vann til hydrogen og oksygen med elektrisitet, blir dyrere.
Norske NEL Hydrogen leverer teknologi til både lokal hydrogenproduksjon i fyllestasjoner for biler, samt til store industrianlegg.
Reinertsen sier at de ikke konkurrerer mot elektrolyse, men mot andre teknologier for hydrogenseparasjon fra naturgass.
Under en hydrogenkonferanse i Trondheim i begynnelsen av november, sa Reinertsen at de ville komme ned i en pris på cirka 10–15 kroner per kilo. Da er det svært konkurransedyktig i forhold til bensin og diesel.
- De har brukt ti år på utviklingen: – Det var gull for ingeniørene våre