Oshaug Metall i Molde har dratt i gang et treårig forskningsprosjekt som de mener vil endre hele næringskjeden. Stikkord er digitalisering, og overføring av 3D-modeller rett til en robot.
Støperibedriften lager propellkomponenter. Det skjer i fire trinn, etter at kunden leverer en 3D-tegning med all geometri på plass. I det første trinnet lager støperiet en modell, gjerne i tre. Fra modellen lages en støpeform av sand med bindemiddel, det er trinn to. I trinn tre skjer støpingen, maskinering og ferdigstilling er fjerde og siste trinn.
Kutter et prosesstrinn
Nå vil ingeniørene hos Oshaug, sammen med NTNU, fjerne hele det første trinnet, modellen blir unødvendig fordi en robot freser ut formen direkte, basert på tegningene. Å lage modellene er tidkrevende, og dyrt.
Hovedkundene til Oshaug Metall er i offshore og maritim industri. Forskningsrådet har gitt støtte til prosjektet under et program for omstilling for de som er sterkt knyttet opp mot oljenæringen.
– Å kunne støpe uten fysiske modeller vil åpne nye markeder for oss. Det er en rekke områder vi ser på der støping ikke er aktuelt med dagens metoder, sier Stein Berg Oshaug, daglig leder i bedriften.
Støpeformene blir kun brukt én gang, det må lages nye for hver støp. Siden de fysiske modellene blir overflødige vil det gjøre støp aktuelt for produkter der det i dag ikke blir vurdert.
Stein Berg Oshaug vurderer støpte fasadeplater til bygg der hver plate kan gjøres unik til overkommelig kost. Et annet alternativ er støpte strukturer tilpasset sikring av anlegg og personell.
Les: Sveiser raskere, billigere og gir lettere konstruksjoner
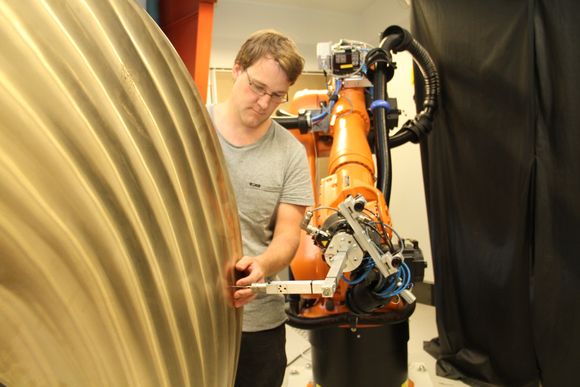
Sømløs integrasjon
Fra NTNU ledes forskningen av Olav Egeland, professor i produksjonsautomatisering ved Institutt for produksjons- og kvalitetsteknikk. Han sier at modellfri støping allerede finnes.
– Men det som tilbys i dag er laget for de som produserer flere tusen enheter. Utfordringen er å få sømløs baneplanlegging fra CAD til robot. I de eksisterende systemene må man gjerne programmere et par dager før det hele er klart. Hvis antallet man produserer er høyt gjør ikke det noe, men med små serier er ikke det aktuelt, sier Egeland.
I tillegg står nøyaktighet høy på listen over prioriteringer. Oshaug Metall er flinke til å støpe med lite monn, da må støpen være nøyaktig. Derfor vil kamerasystemer blir brukt for kontroll og kalibrering. Egeland sier de store robotprodusentene kan levere roboter med tilstrekklig nøyaktighet.
– Dette prosjektet er et godt eksempel på hvordan vi jobber med industrielle systemer, det er Industrie 4.0 i praksis og det er den veien utviklingen går.
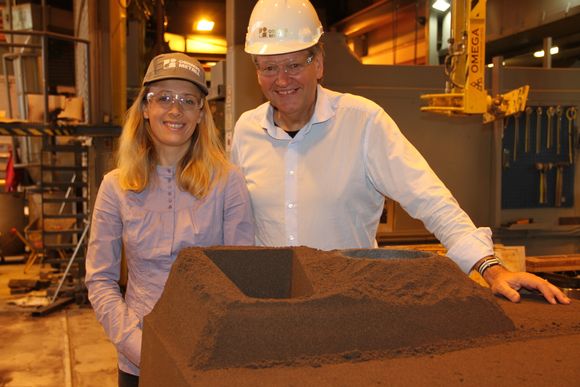
Oksidering kan gi trøbbel
Med unntak av skip som skal pløye seg gjennom is, der propellene som oftes er laget av rustfritt stål, er det en legering av nikkel, aluminium og bronse som gjelder. Det gir utfordringer fordi aluminium oksiderer så raskt. Tynne oksidskjikt blir lett dannet, og svekker det ferdige produktet, om fabrikanten ikke har kontroll på støpeprosessen. Det er ni til ti prosent aluminium i en slik legering, og ved manglende kontroll på støpeprosessen kan oksidsjikt nærmest foldes inn i godset og danne tynne sprekker.
For å få så god kvalitet som mulig er det viktig at støpeprosessen er laminær, ikke turbulent.
– Vi har jobbet mye med fluidmekanikken, det er vår viktigste kjernekompetanse. Med oksid i metallet må man slipe bort mer, opp mot 12 mm er ikke uvanlig. Hos oss er det ikke nødvendig å slipe bort mer enn 1 mm, forteller Oshaug.
Tidligere har bedriften hatt et forskningsprosjekt sammen med Sintef Manufacturing der målet var å automatisere slipingen etter støp. Prosjektet ble vellykket, og resultatene fra det blir brukt i dette nye utviklingsprosjektet.
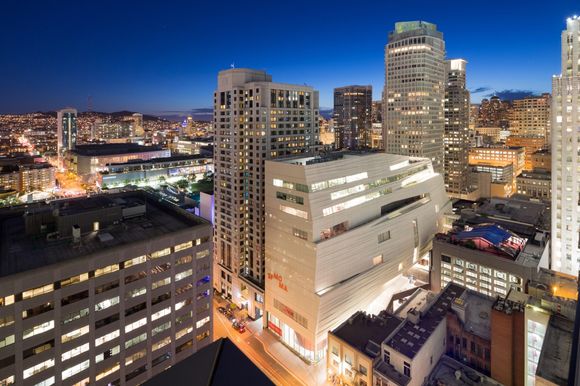
Risikoprosjekter i norsk industri
Innovasjon og utvikling har en viktig plass hos Oshaug Metall, som i dag er eneste støperibedrift i Skandinavia som tar hele prosessen fra tegning til ferdig produkt, de øvrige gjør kun støpejobben. Siden 1998 har bedriften gjennomført 28 forskjellige FoU-prosjekter, det betyr at de til envher tid har minst to prosjekter løpende.
En av utfordringene med støp er størkningskontraksjon som fører til at smelte må ettermates. For NiAl-bronse betyr det at et blad på ett tonn trenger en ettermater med kapasitet på 800 kg.
– I stedet for å bruke vanlig isolasjon til å holde varmen satte vi på en induktiv spole. Det førte til at vi ikke trengte mer enn 100 kg til ettermating. Det gir store besparelser. Prosjektet er nå i avslutningsfasen, der vi vurderer hvordan vi kan hente ut det fulle industrielle og komersielle potensialet av denne teknologien, sier Oshaug.
Totalt går i overkant av fem prosent av omsetningen til forskning. Det er uvanlig mye til norsk industribedrift å være.
– I mine øyne driver de som ikke er aktive på FoU rene risikoprosjekter, uavhengig av bransje. Vi må ligge helt i teknologitoppen for å lykkes, det er en forutsetning.
Vil 3D-printe metall
Når Oshaug titter inn i den teknologiske krystallkulen ser han 3D-print i metall. For sand er han der allerede, støpeformene skal i prosjektet som nå er startet delvis printes, og delvis freses ut. Han viser til Alf Bjørseth og Norsk Titanium som nå er sertifisert for å 3D-printe deler i titan til Boeing i USA.
– Det er en milepæl og et signal om at teknologien er i ferd med å bli moden. Vi ble introduert for 3D metallprinting av Sintef for 13 år siden. Nå nærmer det seg nok, jeg håper vi kan være med på et prosjekt sammen med tunge aktører som for eksempel Rolls Roycel og Brunvoll.
Han tror det bør være mulig å få til noe i løpet av de neste to til tre årene. Metalprinting vil gi muligheter for å bygge lettere konstruksjoner med konstruksjonsprinsipper som i dag bare kan observeres i organisk vokste konstruksjoner.