Produsenten av de velkjente propantankene – de som er til salgs på nær sagt hver eneste bensinstasjon i hele landet – har investert i en utvikling og modernisering av produksjonslinjen. Resultatet er at fleksibiliteten og antall varianter kan økes. Gjennom kontinuerlige forbedringer, i tett samarbeid med Intek Engineering, er syklustiden redusert. Nå kommer en ferdig gasstank ut hvert 14. sekund.
Verdens største – likevel små
Frem til nå har topp, bunn og diameter vært identiske på alle modellene. Det har også det fiskebenmønstrete skallet som omgir trykktanken vært.

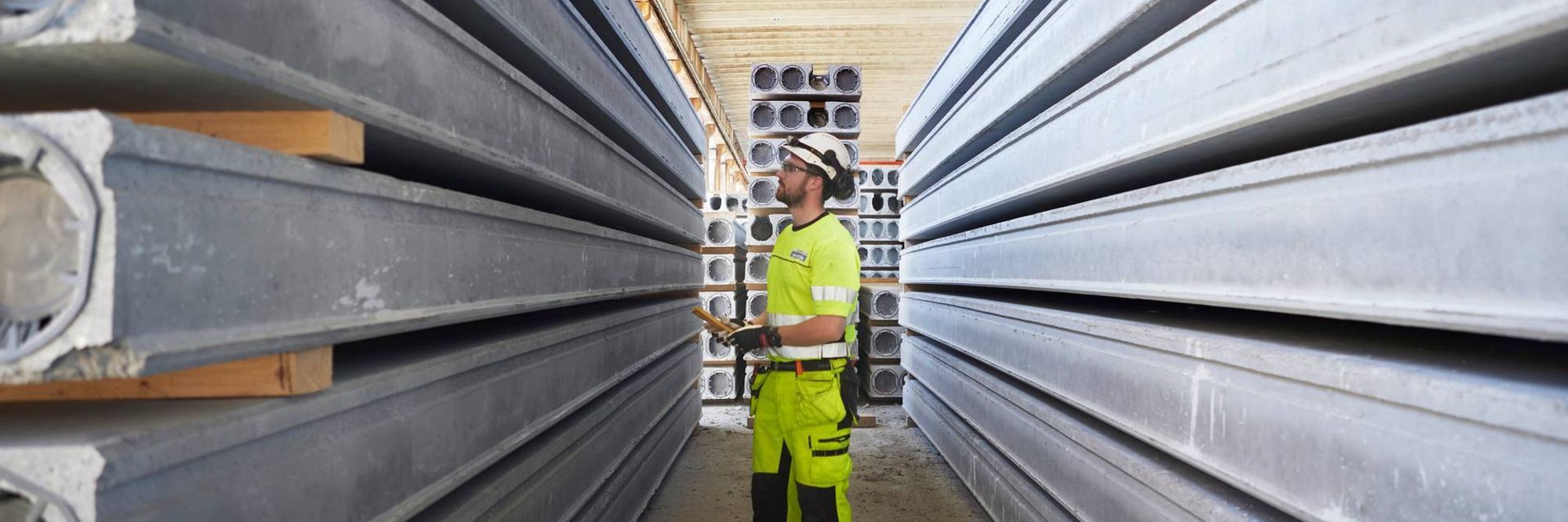
– Vi er verdens største leverandør av komposittbeholdere, men likevel har vi kun to prosent av verdensmarkedet. Nå opplever vi at stadig flere kunder etterspør flere dimensjoner og kanskje annet design, nye produkter kommer til høsten, forteller Ronny Skjølås, produksjonssjef hos Hexagon Ragasco.
Les: Jakter Norges smarteste industribedrift

Inspirert av bilindustrien
Administrerende direktør Skjalg Sylve Stavheim bruker bilindustrien som inspirator og peker på hvor mange varianter de klarer å lage av en og samme modell der forskjellene likevel er små, gjerne i form av hva som blir montert på i siste del av produksjonen.
– Vi kjører nå fjerde generasjons komposittbeholdere, og vi har produktutviklet og forbedret oss mye de siste 15 årene.
Flere varianter - mer kreative
Stavheim forteller at bedriften fremover kommer til å ha fokus på å kunne tilby flere varianter med tilhørende brandingmuligheter for de kundene som ønsker det.
– Vi ønsket å bli mer kreative, samtidig som vi er høyautomatiserte. Det gir oss et konkurransefortrinn.
Prosjektteamet hos komposittprodusenten henvendte seg til et antall mulige leverandører. De falt etter hvert ned på Intek Engineering, som er en del av NCE Raufoss klyngen.
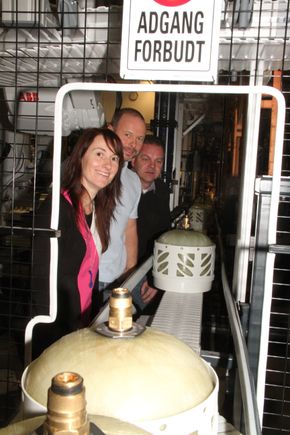
Trangt, veldig trangt
Prosjektteamet hos komposittprodusenten henvendte seg til et antall mulige leverandører. De falt etter hvert ned på Intek Engineering, som er en del av NCE Raufoss klyngen.

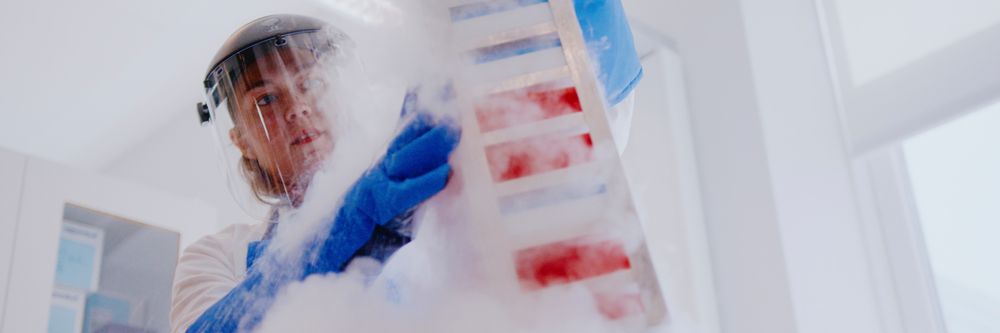
– De kom til oss i mai i fjor, med eget forslag og prisforespørsel. Vi hadde mange runder før endelig løsning ble valgt. Det er trangt, plass viste seg å bli den største utfordringen. Her måles ikke produksjonslokalene i kvadratmeter, men heller i kubikk. Det er bygd tett også i høyden, vi måtte justere på millimeternivå, sier Anita Hager, daglig leder i Intek Engineering.
Simulering var nøkkelen
Nøkkelen for å løse utfordringen var en full simulering av hele anlegget med alt utstyr.
Det var en fordel at Intek kjente systemene godt. De har levert mye av det eksisterende produksjonsutstyret og var også ansvarlige for den siste store oppgraderingen i 2006. Frem til nå har alle produktene hatt samme diameter og samme bunnplate. Nå får Hexagon Ragasco mulighet til å endre langt mer, også diameteren.
For å kunne kjøre flere varianter gjennom linjen var det helt sentralt å få på plass gode vision- og kamerasystemer. Tidligere måtte ventilene inn korrekt posisjonert. Nå er det brukt kameraer, og ventilene blir grepet av roboten og korrekt montert uavhengig av hvordan de kommer inn.
– I tillegg har vi visionsystemer som kontrollerer at O-ring er korrekt plassert og at det er fett på gjengene. Dette er Industrie 4.0 i praksis, og det er grunnleggende enkelt. Operatørene må få data i sanntid rett i synsfeltet. Vi digitaliserer via skjerm, sier Stavheim.
Anita Hager skyter her inn at vellykket automatisering ikke bare handler om de store nyvinningene.
– Det er summen av små trinn, og et godt samarbeid mellom oss og kunden, som gir de gode resultatene. Når vi har en løsning klar, prosjekterer vi den, monterer linjen i våre lokaler og tester. Først når vi vet at det virker, blir det demontert, fraktet til kunden og montert. Da får vi kort innkjøringstid og få feil, sier hun.
Les om: Fremtidens fiskefiletlinje
Hemmelige løsninger
Løsningene som er valgt i den nye delen av produksjonen er så spesielle at Stavheim ikke ønsker den vist frem, Automatisering kan derfor ikke bringe bilder av den nyeste delen av anlegget. Også viklingen av glassfiberen er utført på en egen og smart måte, ikke engang leverandøren av komponentene får komme inn for å se løsningen.
– Vi har hatt dårlige erfaringer med en leverandør som solgte våre løsninger til andre, det ønsker vi ikke, sier Stavheim.