Trondheim: Det er automatisert skreddersøm, nå er en av de to produsjonslinjene fornyet. Produksjonen av Go'morgen-begeret slik kundene kjenner det begynte i 1999. Da var Maskon med å utvikle produksjonslinjen. Senere er den utviklet og forbedret en rekke ganger.
– Men nå var det helt utslitt, det har aldri fungert optimalt og nå begynte det også å bli vanskelig med reservedeler, forteller vedlikeholdssjef Geir Borgen hos Tine.
Det skyldes at designet av begeret ikke er gjort med tanke på produksjon. Nå er Go' morgen et så populært og godt innarbeidet produkt at det var helt uaktuelt å designe begeret på nytt, for å oppnå optimal produksjonsprosess.
Lokal vinner
Tine henvendte seg til Skala Maskon og tyske Oystar A+F. Hovedsakelig fordi begge hadde erfaring med begrene. Prosjektet startet i 2011, og begge ble med helt til kontrakten ble vunnet av Skala Maskon.
– De var først litt i tvil om de i det hele tatt ville ha dette oppdraget. De tenkte litt, men så kom de tilbake og sa ja. Tyskerne jobbet parallelt med en annen løsning. De tapte hovedsakelig fordi de ikke produserer skjeapplikasjoner selv og ville ha dem eksternt. Da hadde vi ikke kommet lenger enn for den andre linjen som stammer fra 2007, sier Borgen.
– Så er det jo artig at en lokal bedrift kom opp med en bedre løsning, legger han til.
Han forteller at Tine hadde to viktige krav: oppetiden skulle økes og antall komponenter skulle ned.
Den gamle linjen hadde kun en overløfter, en robot som tar de ferdige begrene og plasserer dem i en lav pappeske. Så hadde den to skjeapplikasjoner, som henter skjeene og limer dem fast på begeret.
Les også: Robotene ut av buret
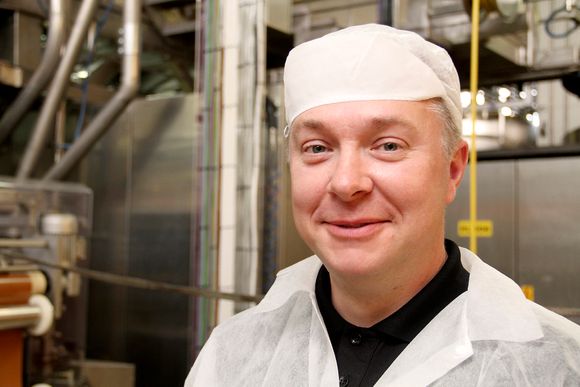
Fire moduler
Den nye linjen har fire moduler der hver enhet har både overløfter og skjeapplikasjon. Begrene kommer på et transportbånd og blir styrt inn mot den modulen som skal brukes. Tre moduler hadde vært tilstrekkelig for dagens produksjon, men siden fyllemaskinen ikke kan stoppe uten store konsekvenser valgte de en løsning der det er en ekstra modul som kan tas i bruk om en av de andre skulle svikte.
– Det hadde vært så mange feil med den gamle overløfteren at det nå kom et krav om at det måtte være rom for feil uten produksjonsstans, sier Rune Reinås, salgsansvarlig for maskiner hos Skala Maskon.
Han legger til at de i utviklingen fikk mange innspill fra Omron, som de brukte som underleverandør i prosjektet.
Kjell Baardsgaard fra Omron forteller at Skala Maskon var de første til å ta i bruk Omrons nye robot til dette Tine-prosjektet.
Les: Robot blir raskt lønnsom hos Nortura
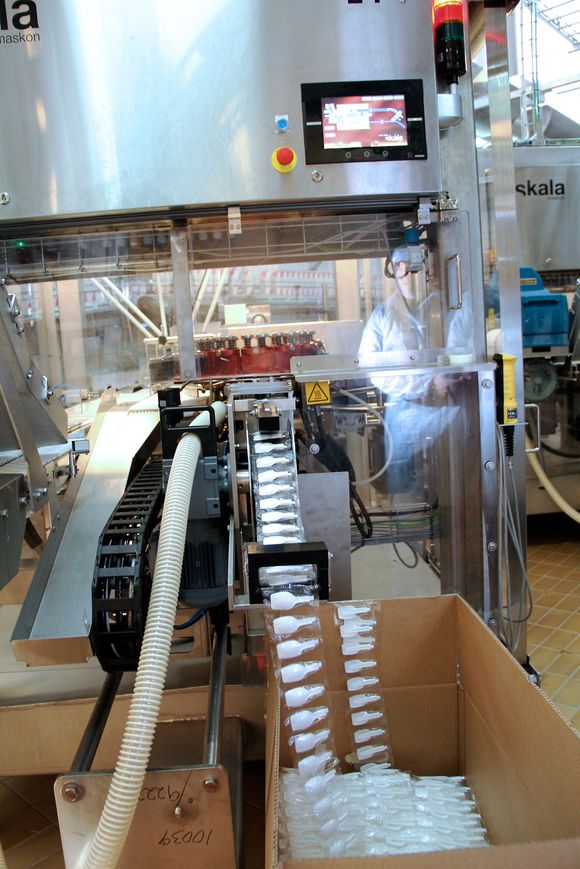
Bruker deltarobot
– Det er en deltarobot og veldig mange av produktene i den nye SYSMAC-plattformen er med. Det er NJ-kontrolleren, NA-operatørpanelet, samt MX2 frekvensomformere og NX bus-system på EtherCAT med integrert sikkerhetssystem og I/O, sier Baardsgaard.
En deltarobot består av tre armer som er koblet til et universalledd. Det er bruken av parallellogrammer i armene som er spesielt for deltaroboter, det gjør det mulig å opprettholde orienteringen til verktøyet.
Med denne løsningen er det unødvendig med egen styring til roboten, det er integrert i kontrolleren. Reinås forteller at dette var det andre prosjektet med den nye kontrolleren.
– Det første var til Norbitech på Røros, og det førte til en heftig utvikling av programvaren, sier Reinås.
Kontraktssummen for den nye linjen var 9,6 millioner, med noen tillegg endte det på rett over 10 millioner kroner. Men automasjonsutstyret er faktisk ikke så dyrt.
– Nei, det utgjør rundt 10 prosent av kontraktssummen, resten er arbeid og mekanikk, sier Reinås.
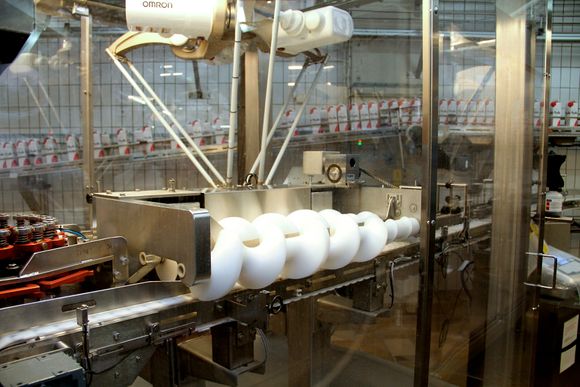
Høyere presisjon
Så langt ser dette ut til å ha blitt en suksess. En lett modifisert variant for andre produkter er allerede solgt til Tine på Tretten, og for Omron har dette vært en av de største kontraktene noensinne.
Borgen forteller at prosjektet startet med at samtlige 22 på vedlikeholdsgruppa ble involvert i en idédugnad der kom det opp hva de ønsket, og ikke minst hva de ikke ville ha på det nye anlegget.
– Den viktigste endringen var nok at vi har fjernet 12–15 remhjul og noen ganske kostbare remmer som førte begrene gjennom applikatoren. En annen viktig forbedring er at hastigheten på begeret gjennom applikatoren er kraftig redusert, det gir høyere presisjon på plassering av skje, sier Reinås.
Den nye linjen har i stedet en skive som bretter opp begeret når den snurrer rundt, og åpner for at skjeen kan limes fast. Linjen har vært i drift siden februar. Erlen Høen Lein, automatiker som jobber med denne linjen forteller at den nye linjen ble montert en fredag og allerede mandagen etter var de klar for produksjon.
Les om: Fremtidens industri krever endringer
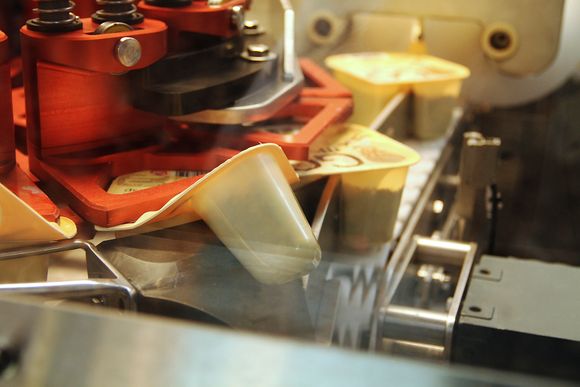
Imponert
– Vi har kjørt en oppetidstest, den viser godt over 99 prosent, i kontrakten er kravet 95 prosent. Erfaringsmessig går det ikke veldig bra i starten, men her har det ikke vært stort, sier Lein.
Borgen legger til at hans erfaring som vedlikeholdssjef er at det fort går et år før en ny linje er ferdig. Her har det kun vært noen få modifikasjoner og han regner anlegget som «oppe og går» etter knapt fire måneder.
– Alle har jo fått et godt forhold til anlegget fordi automatikere og operatører har fått være med fra starten og blitt lyttet til.
– Jeg er imponert, spesielt fordi dette er skreddersøm, avslutter Borgen.