Hansen Protection, som nylig vant en større kontrakt om leveranse av flere tusen drakter til Statoil, har brukt både tid og penger på automatiserte løsninger. Men automatisert produksjon av redningsdrakter er ikke lett – så langt har ingen klart det.
Hansen Protection har brukt åtte år i forsknings- og utviklingsprogrammet SFI Norman (se faktaboks), der blant andre også Ekornes var med.
Har eksperimentert
– Vi har eksperimentert med ulike sømautomater. Fleksibiliteten i stoffet er den største utfordringen. Vi har prøvd mye, men knapt noen på verdensmarkedet har lyktes. Den som er kommet lengst er Ekornes, sier Frithjof Kylstad, ansvarlig for produksjon, innkjøp og lager og bedriftens prosjektleder for SFI Norman-deltakelsen.

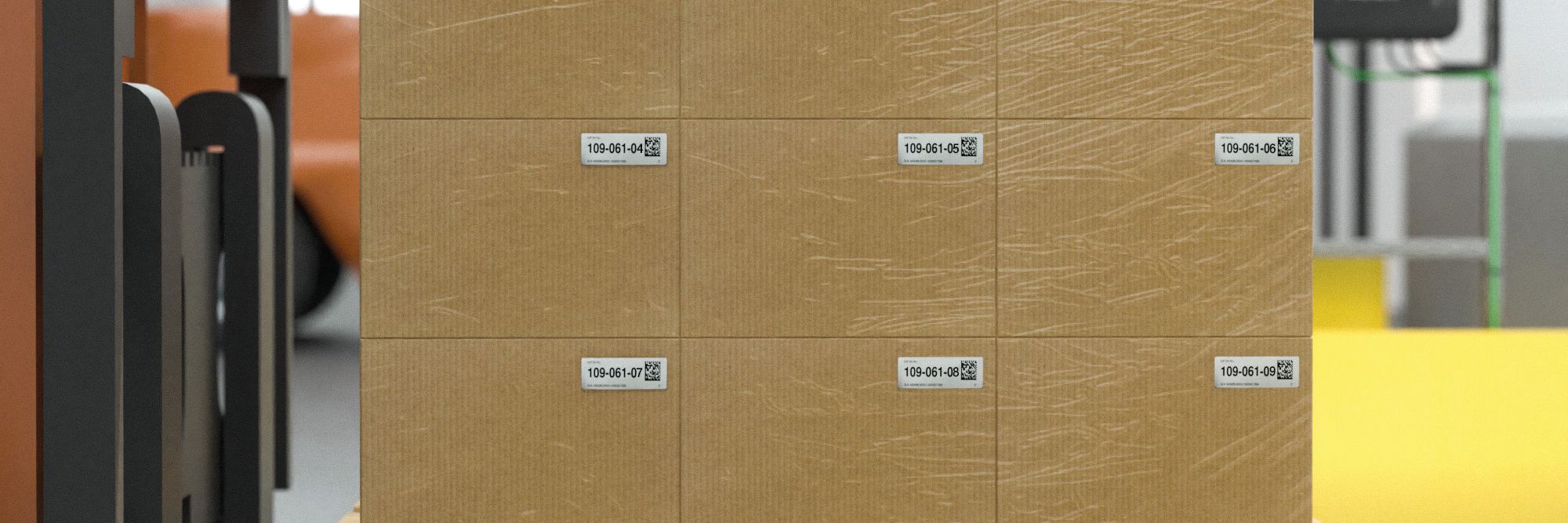
Kylstad sier at SFI Norman ga dem god uttelling på produktutvikling og Lean-produksjon, men mindre på automatisert produksjon. Bedriften har ikke gitt opp, og er stadig på utkikk etter automatiserte løsninger, og han følger med på maskinsiden for å se om det er noe de kan utnytte.
– Automatisering er viktig for å sikre norsk produksjon. Vi ser jo at industrien i lavkostland blir bedre og bedre for hvert år som går.
Nå sier Kylstad at Statoil-ordren er så stor og har en slik varighet at den vil utløse ytterligere arbeid for å øke graden av automatisering. Men bedriften vil konsentrere seg om andre deler av produksjonen enn søm.
Satser på enkeltkomponener
– Vi tror ikke en fullautomatisert produksjonslinje er mulig i overskuelig fremtid. Nå vil vi heller se på områder og komponenter. En mulighet er å standardisere komponentene, det vil gi færre varianter, og dermed kan vi automatisere deler av produksjonen.
Kylstad tror automatisert fremstilling av deler av draktene vil gi størst gevinst. Han ser kombinasjon av kvalitet og redusert gjennomløpstid som de viktigste gevinstene ved en slik utvikling. Bedriften starter et prosjekt i disse dager der målet er å finne egnete komponenter. Da skal alle draktene analyseres fra A til Å, med deltakere fra design, produksjon og service. Automatisering blir et tema, også søm. Prosjektet vil pågå et par års tid.
– Men vi tror ikke det er så mye å hente på søm i overskuelig fremtid. Der har vi nok mer å hente på å samarbeide med maskinleverandører, som for eksempel Amatec.
Det er skjæring og kutting som er mest automatisert til nå. Det arbeidet startet så tidlig som midt på 80-tallet, og maskinen som i dag brukes stammer fra 2012. Der trekkes tekstilene frem, dekkes av en tynn plastfolie før luften suges ut. Dermed holdes stoffet fast ved hjelp av undertrykk. Alle mål og mønstre er lagret i maskinen som skjærer med kniv.
– Et alternativ er laserkutting, men varmen har en tendens til å smelte snittflatene.
Les undersaken: Start med lavthengende frukter
Automatisert test av tetthet
Alle draktene må gjennom grundig testing. De må være absolutt vanntette og skal tilfredsstille strenge standarder. For drakter til helikopterbruk har Luftfarttilsynet egne krav og egne kontrollører som følger med.
I dag pumpes draktene opp med trykkluft. Mens de minner mest om en hydrogenfylt ballong, blir de bestrøket med en tynn såpeløsning. Selv det minste hull vil da føre til bobler, og feilen er lokalisert. Men jobben er manuell.
– Vi skal jobbe mer med testing for å finne gode automatiserte løsninger for de prosessene.
Så er det en større IT-investering på gang. To konkurrenter kniver om kontrakten, Kylstad håper å ha en avgjørelse før jul. Målet er å utnytte serienumrene bedre og få langt mer av dokumentasjon og produksjonsdata samlet.
.png)
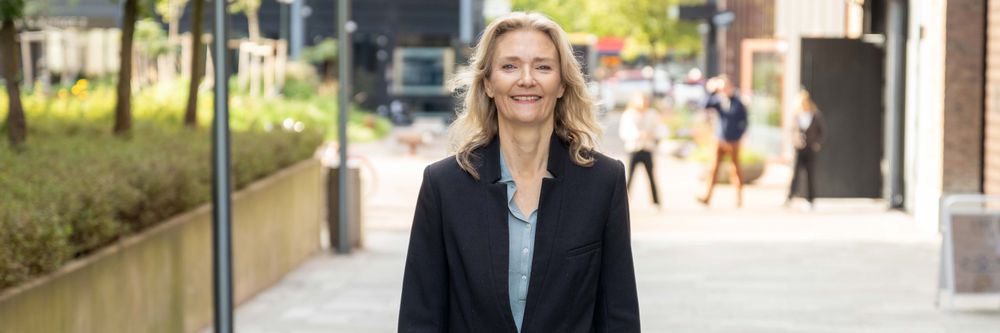
– Vi skal forbedre datafangsten gjennom hele produksjonen. Det vil redusere mye manuelt arbeid. Vi har valgt ikke å bruke RFID, men velger i stedet en kombinasjon av strekkode og QR-kode. Det er en omfattende prosess og vil påvirke hele bedriften.
Så konklusjonen er da at for Hansen Protection er økt automatisering et mål, men en fullautomatisert linje er urealistisk. Det blir stykkevis automatisering.
– Ja, det kan du si. Det er det eneste realistiske i denne bransjen. Så vidt jeg kan se er det ingen av konkurrentene våre som har kommet lenger enn oss, sier Kylstad.