Her er det meste av varehåndteringen automatisert, logistikksenteret er i dag Europas mest avanserte og moderne anlegg av sin type.
Disponent Ove H. Bjørgum, som også var prosjektleder for det nye senteret, sier det er sterkt prispress i bransjen og at de trengte logistikkløsninger med lavest mulig kostnader. Det var også behov for økt kapasitet. Det nye logistikksenteret ble prosjektert før kjøpet av Ica skjedde, dermed er kapasitet blitt ytterligere viktigere.
De har lyktes. Produksjonen er mer enn tredoblet.
Anlegget er levert av tyske Witron som vant til slutt over en rekke andre tilbydere, blant annet Knapp og Dematic.
– Witron hadde det beste tilbudet, samt at de hadde levert en rekke anlegg med en god «track record».
Les også: "Fast track" gir bedre matvarer
Temperatursoner
Anlegget er delt inn i ulike temperatursoner for tørrvarer, frukt og grønt, kjølevarer og frossenvarer. Det er helautomatisk plukk for de aller fleste varene og halvautomatisk for varer som er for små til at de kan håndteres uten menneskelig plukk.
En liten del plukkes fortsatt på den gamle måten med plukktruck, men dette gjelder kun et fåtall varer som enten er for store for maskineriet, eller hvor forpakningen er for ustabil. Eksempler er toalettpapir og tørkepapir som kommer innpakket i store «plastposer».
Det halvautomatiske anlegget er et såkalt sone-til-sone system der esken som skal til kunden går fra plukksone til plukksone for å få med de varene den skal ha. Operatørene bemanner sonene der de mest frekvente varene ligger nærmest plukkstasjonen, og plukket blir styrt etter lys som indikerer hvor det skal plukkes fra og hvilket antall. Når esken til kunden er ferdig, blir den automatisk veid og vil gå til en kontrollstasjon om vekten avviker fra den beregnete verdien.

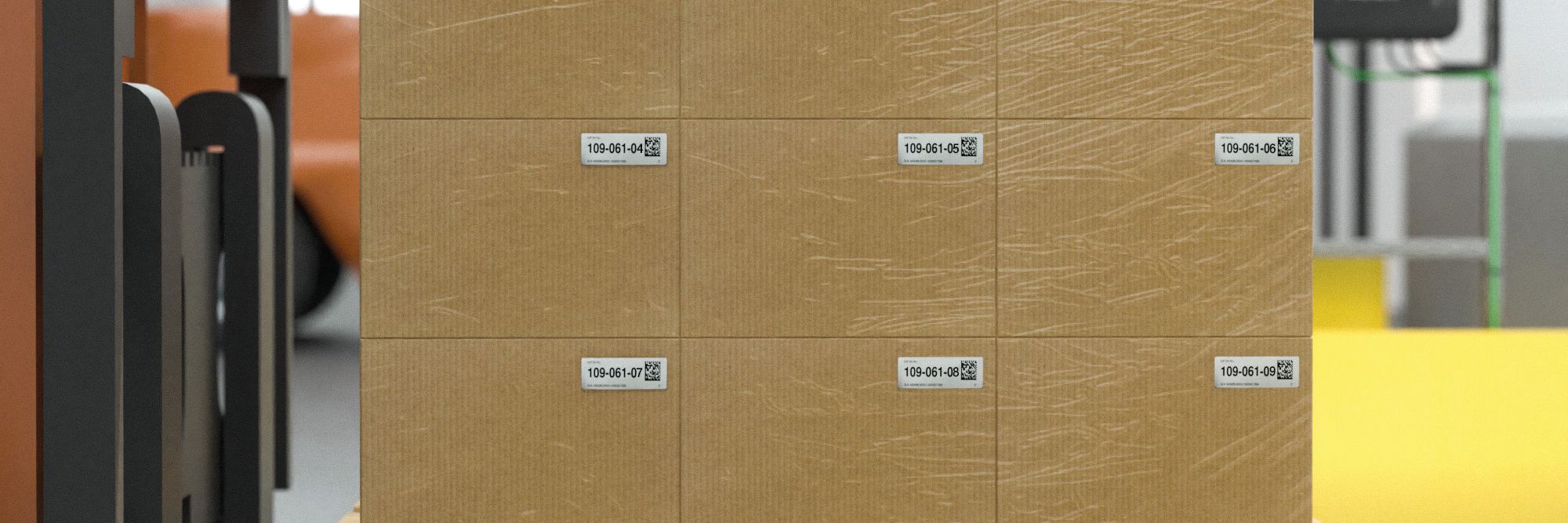
– Men feilplukk er det ikke mange av. Leverandøren garanterer at det ikke skal være mer enn én feilplukk for hver 20 000 vare. Dette har man erfaring med, det fungerer godt.
En av varene som tidligere ble håndtert helautomatisk er nå flyttet til den manuelle halvautomatiske plukkavdelingen. Det er olivenolje i glassflasker.
– Vi hadde et uhell, og noen flasker knuste. Vi brukte uker på å få all oljen bort fra ruller, kraner, reimer, etc. og rense skikkelig.
Les: Fremtidens fiskefiletlinje
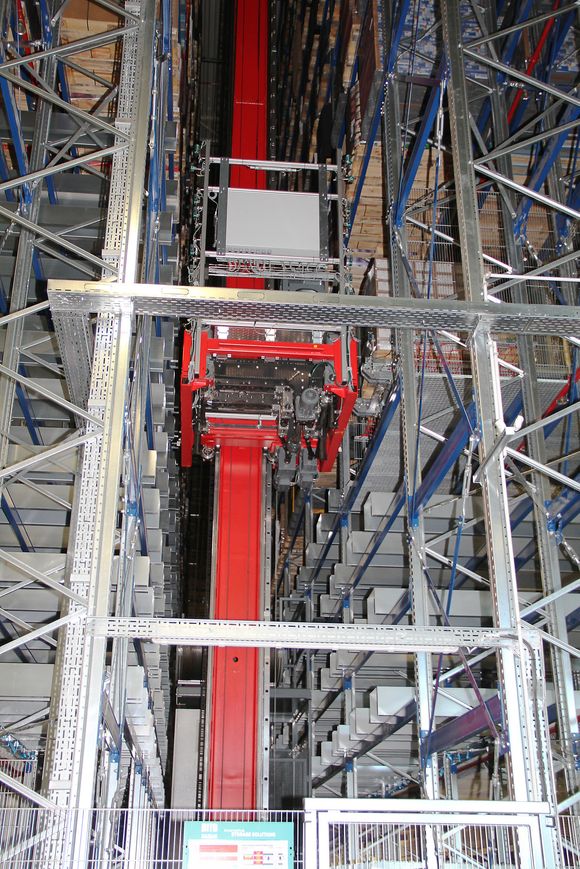
Skummel stabiliseringsfase
Automatisering ble oppfordret til å lage en reportasje om logistikksenteret til Coop av en leser. Denne leseren mente det hadde vært en spesielt vanskelig start på anlegget. Det avviser Bjørgum kontant.
– Ethvert prosjekt av denne typen går gjennom de samme fasene. I oppstartfasen er det alltid mange feil. Det er slik det er, og vi har også hatt vår del av slike problemer. I ettertid har nok likevel innkjøringen skjedd med mindre vanskeligheter enn hva andre aktører har opplevd.

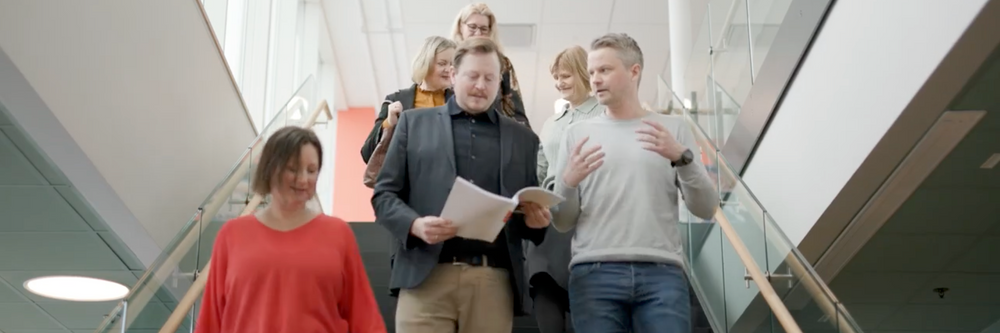
Coop og Witron valgte å se hver av de fire temperatursonene som et eget prosjekt, og de startet forsiktig. I en slik opptrapping er det mange hensyn å ta, sier Bjørgum. Man må sikre at det er tilstrekkelig volum til å avdekke svakheter og feil, men samtidig sørge for at det ikke er mer enn at anlegget allikevel til enhver tid kan takle det uten at kundene blir skadelidende. Så mantraet var en fot på gassen og en fot på bremsen. Når all tørrvareplukk var overført fra det gamle lageret, begynte så opptrappingen av neste temperatursone og så videre.
Bjørgum forteller at slike oppstarter gjerne kan deles inn i fire faser. Først oppstartfasen, der det naturlig er mye feil og justeringer. Deretter følger stabiliseringsfasen, så forbedringsfasen før senteret kommer inn i den ordinære driftsfasen.
– Stabiliseringsfasen er skummel. «Alle» tror vi er ferdige, men det er vi jo ikke. Da kommer feil som opptrer sjelden eller som følge av menneskelige feil og mangel på erfaring. I fjor høst hadde vi noen uker der det ble betydelige forsinkelser til mange av kundene. Dette var selvfølgelig svært uheldig og belastende for våre kunder, men det må sies at det var lite sammenlignet med tilsvarende prosjekter opplever.
Nå er logistikksenteret i fase tre, forbedringsfasen, som er den siste før ordinær driftsfase.
– Det er fortsatt noen lavthengende frukter igjen, og utenfra virker det nok som om vi er i driftsfasen nå. Dit kommer vi på vårparten neste år.

Opptatt av menneskene
Bjørgum mener at det viktigste som skjer når en bedrift som Coop skal øke kapasiteten og modernisere ikke er de tekniske installasjonene eller det nye bygget.
– Jeg fikk hele tiden spørsmål om hvordan det gikk med automatiseringen og hvordan det gikk med bygget. Men ingen spurte om hvordan det gikk med organisasjonsutvikling, kommunikasjon og forventningsstyring, eller med implementering av endringer hos kunder og leverandører.
Alle ansatte kom fra det gamle lageret. Det var manuelt arbeid som ikke krevde kompetanse, og det var enkeltmannsarbeid. Ingen behøvde å snakke med hverandre. Nå er det lagarbeid som krever kompetanse.
– Vi startet med noe så banalt som å kreve at folk hilser på hverandre. Det er helt sentralt for å få et slikt system til å virke at bedriftskulturen er god. Ledere må gå fra kommandostil, der de kan mer enn sine underordnete, til veiledning, der mange kan mer enn dem. Det har vært en lang reise å endre gamle holdninger og tankesett.
For Bjørgum har det vært viktig at de ansatte har god forståelse for hvordan anlegget virker. Nå er det to som driver opplæring på fulltid. Dette er ikke en formalisert utdanning, men en bedriftsintern opplæring for Coop. I tillegg til noen spesialister og ledelsen er det en gruppe teknikere på anlegget. De er ikke ansatt av Coop, men av Witron.
– Jeg ønsker å få myndighet, ansvar og eierskap så langt ned i organisasjonen som mulig. Bare slik kan vi sikre kontinuerlig forbedring og eierskap.
Til det nye anlegget er det utviklet en egen IT-løsning som brukes av driftsoperatørene til å melde avvik og forbedringsforslag. Meldingen går automatisk til de som kan gjøre noe med det.
– Det gir oss en veldig stor datafangst som benyttes til å gjøre forbedringer. Noe av det mest spennende med dette er jo å få teknologien til å fungere sammen med menneskene.
Les om: Robotene ut av buret
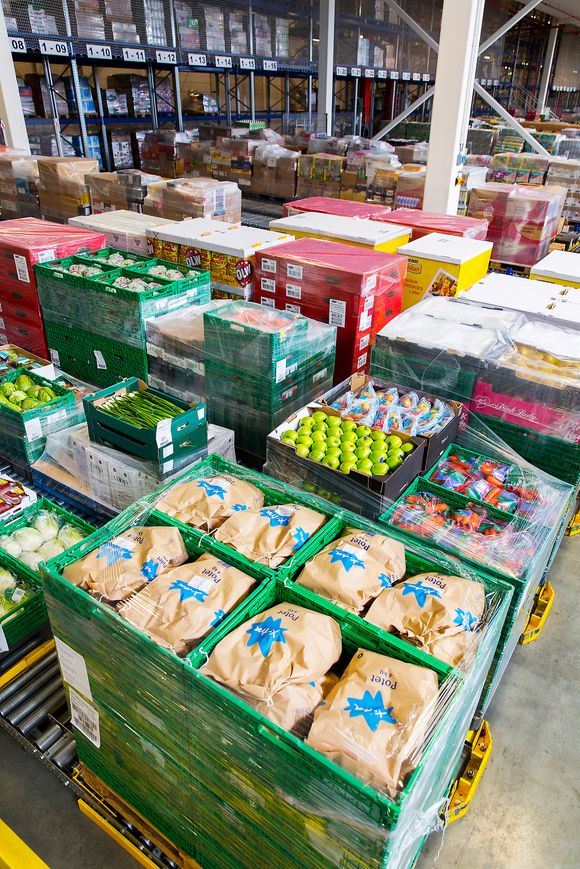
Skape forståelse
Coop har måttet ha en lang rekke besøk av leverandører for å skape forståelse for nye behov. Det automatiserte anlegget fører til andre krav enn tidligere til forpakning og til merking.
– Vi viser dem anlegget, da får de forståelse og dermed gjør de nødvendige endringer.
Fortsatt gjenstår justeringer, tilpasninger og opplæring. Men for Bjørgum er det ikke tvil om at det nye anlegget er en suksess.
– På verdensbasis er denne bransjen fortsatt tungt manuelt drevet. Når det gjelder produktivitet innen tørrvarer, er vi på femteplass av de 35 anleggene som Witron har installert av denne versjonen. Og vi har fortsatt forbedringsmuligheter, sier Bjørgum.